LTC1922EG-1#PBF Linear Technology, LTC1922EG-1#PBF Datasheet - Page 18
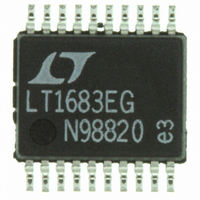
LTC1922EG-1#PBF
Manufacturer Part Number
LTC1922EG-1#PBF
Description
IC CTLR PWM SYNC 20SSOP
Manufacturer
Linear Technology
Datasheet
1.LTC1922EG-1PBF.pdf
(24 pages)
Specifications of LTC1922EG-1#PBF
Pwm Type
Voltage/Current Mode
Number Of Outputs
1
Frequency - Max
1MHz
Duty Cycle
99%
Buck
No
Boost
No
Flyback
No
Inverting
No
Doubler
No
Divider
No
Cuk
No
Isolated
Yes
Operating Temperature
-40°C ~ 85°C
Package / Case
20-SSOP
Frequency-max
1MHz
Lead Free Status / RoHS Status
Lead free / RoHS Compliant
Voltage - Supply
-
Available stocks
Company
Part Number
Manufacturer
Quantity
Price
OPERATIO
LTC1922-1
18
Selecting the Power Stage Components
Perhaps the most critical part of the overall design of the
converter is selecting the power MOSFETs, transformer,
inductors and filter capacitors. Tremendous gains in effi-
ciency, transient performance and overall operation can
be obtained as long as a few simple guidelines are followed
with the phase shifted full-bridge topology.
Power Transformer
This guide is aimed at selecting readily available standard
“off the shelf” transformers. The basic requirements,
however, apply to custom transformer designs as well.
Switching frequency, core material characteristics, series
resistance and input/output voltages all play an important
role in transformer selection. Close attention also needs to
be paid to leakage and magnetizing inductances as they
play an important role in how well the converter will
achieve ZVS. Planar magnetics are very well suited to
these applications because of their excellent control of
these parameters.
Turns Ratio
The required turns ratio for a current doubler secondary is
given below. Depending on the magnetics selected, this
value may need to be reduced slightly.
Turns ratio formula:
where:
Magnetizing, Output, and Leakage Inductors
A lower value of magnetizing and output inductance will
improve the ability of the converter to achieve ZVS over the
full range of loads and reduce the size of the external
commutating inductor. One of the trade-offs is increased
primary referred ripple current which has a small negative
V
D
N
IN(MIN)
MAX
2 •
= Maximum duty cycle of controller
V
= Minimum V
IN MIN
(
V
OUT
U
)
•
D
MAX
IN
for operation
impact on efficiency. Other factors to consider are switch-
ing frequency and required maximum duty cycle. A lower
value of magnetizing inductance will require a longer time
to reset the core, cutting into the available duty cycle
range. As switching frequencies increase, this becomes
more significant. In general, the magnetizing inductance
value should be the lowest value required in order to
achieve the necessary maximum duty cycle at the chosen
switching frequency. Output inductor value determines
the magnitude of output ripple current and therefore the
ripple voltage along with the output capacitors. Generally
speaking, the output inductance should be minimized as
much as possible in order to improve transient response.
In addition, output capacitance ESR should be minimized
as much as possible. Using the equations below, plug in
the manufacturers magnetizing inductance value and a
“starting value” of commutating inductance (1% of L
to verify that a sufficient max duty cycle can be achieved
at the desired switching frequency. Next, use equation (2)
to determine what the absolute minimum required L
to guarantee ZVT over the entire load range. One or two
iterations may be required in order to arrive at the final
selections.
where:
MAX DC vs L
T
L
MAX DC
L
R
COM
COM
I
= transformer reset time (worst case)
O MAX
(
vs ZVS vs Load
L
)
L
•
f
2
SW
COM
f
–
4 3
SW
/
f
•
SW
2
L
at f
•
MAG
L
C
•
MAG
SW
OSS
T
R
2
;
•
•
V
•
N
IN
L
D
MAG
2
• • •
2
2
D N
•
f
SW
2
L
COM
V
IN
COM
L
MAG
L
(1)
(2)
is
)