LTC1922EG-1 Linear Technology, LTC1922EG-1 Datasheet - Page 14
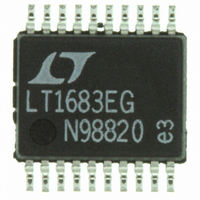
LTC1922EG-1
Manufacturer Part Number
LTC1922EG-1
Description
IC CTRLR PWM SYNC 20SSOP
Manufacturer
Linear Technology
Datasheet
1.LTC1922EG-1PBF.pdf
(24 pages)
Specifications of LTC1922EG-1
Pwm Type
Voltage/Current Mode
Number Of Outputs
1
Frequency - Max
1MHz
Duty Cycle
99%
Buck
No
Boost
No
Flyback
No
Inverting
No
Doubler
No
Divider
No
Cuk
No
Isolated
Yes
Operating Temperature
-40°C ~ 85°C
Package / Case
20-SSOP
Frequency-max
1MHz
Lead Free Status / RoHS Status
Contains lead / RoHS non-compliant
Voltage - Supply
-
Available stocks
Company
Part Number
Manufacturer
Quantity
Price
Company:
Part Number:
LTC1922EG-1
Manufacturer:
IBM
Quantity:
942
Part Number:
LTC1922EG-1
Manufacturer:
LT
Quantity:
20 000
OPERATIO
LTC1922-1
2. The LTC1922-1 can either synchronize other PWMs, or
be synchronized to an external frequency source or PWM
chip. See Figure 6 for details.
14
3. Slope compensation is required for most peak current
mode controllers in order to prevent subharmonic oscilla-
tion of the current control loop. In general, if the system
duty cycle exceeds 50% in a fixed frequency, continuous
current mode converter, an unstable condition exists
within the current control loop. Any perturbation in the
current signal is amplified by the PWM modulator result-
ing in an unstable condition. Some common manifesta-
tions of this include alternate pulse nonuniformity and
pulse width jitter. Fortunately, this can be addressed by
adding a corrective slope to the current sense signal or by
subtracting the same slope from the current command
signal (error amplifier output). In theory, the current
doubler output configuration does not require slope com-
pensation since the output inductor duty cycles only
approach 50%. However, transient conditions can mo-
mentarily cause higher duty cycles and therefore, the
possibility for unstable operation. The exact amount of
required slope compensation is easily programmed by the
LTC1922-1 with the addition of a single external resistor
(see Figure 7). The LTC1922-1 generates a current that is
proportional to the instantaneous voltage on C
C
1.25 C
T
OF SLAVE(S) IS
C
T
C
T
FREQUENCY
EXTERNAL
T
SOURCE
OF MASTER.
Figure 6b. SYNC Input from an External Source
LTC1922-1
MASTER
Figure 6a. SYNC Output (Master Mode)
U
SYNC
5.1k
5 SLAVES
AMPLITUDE > 1.8V
12.5ns < PW < 0.4/
UP TO
1k
•
•
•
1k
1k
5.1k
5.1k
5.1k
SYNC
SYNC
SYNC
LTC1922-1
LTC1922-1
LTC1922-1
SLAVES
C
T
C
1922 F06b
T
C
C
T
T
C
C
1922 F06a
T
T
T
,
Current Sensing and Overcurrent Protection
Current sensing provides feedback for the current mode
control loop and protection from overload conditions. The
LTC1922-1 is compatible with either resistive sensing or
current transformer methods. Internally connected to the
LTC1922-1 CS pin are two comparators that provide
pulse-by-pulse and overcurrent shutdown functions re-
spectively. (See Figure 8)
(33 A/V
approximately 125 A and is output from the CS pin. A
resistor connected between CS and the external current
sense resistor sums in the required amount of slope
compensation. The value of this resistor is dependent on
several factors including minimum V
frequency, current sense resistor value and output induc-
tor value. An illustrative example with the design equation
is provided below.
Example: V
Transformer turns ratio (N) = V
V
R
f
R
(2 • 2.2 A • 100k • 125 A • 3)
R
to account for tolerances in I
SW
OUT
CS
SLOPE
SLOPE
C
= 300kHz, i.e., transformer f = f
= 0.025
T
(CT)
= 3
V
I
L = 2.2 H
= V
= 500 , choose the next higher standard value
OUT
Figure 7. Slope Compensation Circuitry
IN
OUT
). Thus, at the peak of C
O
= 36V to 72V
LTC1922-1
= 40A
• R
= 3.3V
33k
I =
CS
V(C
/(2 • L • f
33k
T
)
CS
SLOPE
ADDED
T
CURRENT SENSE
• 125 A • N) = 3.3V • 0.025/
WAVEFORM
SLOPE
R
SLOPE
IN(MIN)
, R
IN
SW
T
, V
, this current is
CS
/2 = 150kHz
• D
OUT
, N and L.
1922 F07
R
BRIDGE
CURRENT
CS
MAX
, switching
/