LTC1709EG-7 Linear Technology, LTC1709EG-7 Datasheet - Page 20
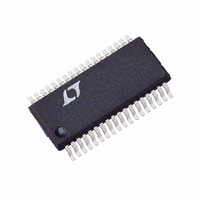
LTC1709EG-7
Manufacturer Part Number
LTC1709EG-7
Description
IC SW REG STEP-DOWN SYNC 36-SSOP
Manufacturer
Linear Technology
Type
Step-Down (Buck)r
Datasheet
1.LTC1709EG-7.pdf
(28 pages)
Specifications of LTC1709EG-7
Internal Switch(s)
No
Synchronous Rectifier
Yes
Number Of Outputs
2
Voltage - Output
1.3 ~ 3.5 V
Current - Output
3A
Voltage - Input
4 ~ 36 V
Operating Temperature
-40°C ~ 85°C
Mounting Type
Surface Mount
Package / Case
36-SSOP
Lead Free Status / RoHS Status
Contains lead / RoHS non-compliant
Power - Output
-
Frequency - Switching
-
Available stocks
Company
Part Number
Manufacturer
Quantity
Price
Company:
Part Number:
LTC1709EG-7
Manufacturer:
LT
Quantity:
392
Part Number:
LTC1709EG-7
Manufacturer:
LT/凌特
Quantity:
20 000
Company:
Part Number:
LTC1709EG-7#PBF
Manufacturer:
Linear Technology
Quantity:
135
APPLICATIO S I FOR ATIO
LTC1709-7
If the external frequency (f
lator frequency f
pulling up the PLLFLTR pin. When the external frequency
is less than f
down the PLLFLTR pin. If the external and internal fre-
quencies are the same but exhibit a phase difference, the
current sources turn on for an amount of time correspond-
ing to the phase difference. Thus the voltage on the
PLLFLTR pin is adjusted until the phase and frequency of
the external and internal oscillators are identical. At this
stable operating point the phase comparator output is
open and the filter capacitor C
LTC1709-7 PLLIN pin must be driven from a low imped-
ance source such as a logic gate located close to the pin.
The loop filter components (C
current pulses from the phase detector and provide a
stable input to the voltage controlled oscillator. The filter
components C
acquires lock. Typically R
0.1 F.
Minimum On-Time Considerations
Minimum on-time, t
that the LTC1709-7 is capable of turning on the top
MOSFET. It is determined by internal timing delays and the
gate charge required to turn on the top MOSFET. Low duty
cycle applications may approach this minimum on-time
limit and care should be taken to ensure that:
20
PLLIN
EXTERNAL
OSC
Figure 7. Phase-Locked Loop Block Diagram
50k
0SC
LP
, current is sunk continuously, pulling
0SC
and R
FREQUENCY
U
DETECTOR
DETECTOR
ON(MIN)
DIGITAL
PHASE/
PHASE
, current is sourced continuously,
LP
U
PLLIN
LP
, is the smallest time duration
determine how fast the loop
=10k and C
LP
) is greater than the oscil-
LP
2.4V
, R
holds the voltage. The
W
LP
) smooth out the
LP
is 0.01 F to
PLLFLTR
R
10k
LP
U
1709 F07
OSC
C
LP
If the duty cycle falls below what can be accommodated by
the minimum on-time, the LTC1709-7 will begin to skip
cycles resulting in variable frequency operation. The out-
put voltage will continue to be regulated, but the ripple
current and ripple voltage will increase.
The minimum on-time for the LTC1709-7 is generally less
than 200ns. However, as the peak sense voltage de-
creases, the minimum on-time gradually increases. This is
of particular concern in forced continuous applications
with low ripple current at light loads. If the duty cycle drops
below the minimum on-time limit in this situation, a
significant amount of cycle skipping can occur with corre-
spondingly larger ripple current and voltage ripple.
If an application can operate close to the minimum
on-time limit, an inductor must be chosen that has a low
enough inductance to provide sufficient ripple amplitude
to meet the minimum on-time requirement. As a general
rule, keep the inductor ripple current of each phase equal
to or greater than 15% of I
FCB Pin Operation
The FCB pin can be used to regulate a secondary winding
or as a logic level input. Continuous operation is forced
when the FCB pin drops below 0.8V. During continuous
mode, current flows continuously in the transformer pri-
mary. The secondary winding(s) supply current only when
the bottom, synchronous switch is on. When primary load
currents are low and/or the V
synchronous switch may not be on for a sufficient amount
of time to transfer power from the output capacitor to the
secondary load. Forced continuous operation will support
secondary windings providing there is sufficient synchro-
nous switch duty factor. Thus, the FCB input pin removes
the requirement that power must be drawn from the
inductor primary in order to extract power from the
auxiliary winding(s). With the loop in continuous mode,
the auxiliary output(s) may nominally be loaded without
regard to the primary output load.
t
ON MIN
V f
V
IN
OUT
OUT(MAX)
IN
/V
OUT
at V
ratio is low, the
IN(MAX)
.