LM2653MTC-ADJ/NOPB National Semiconductor, LM2653MTC-ADJ/NOPB Datasheet - Page 8
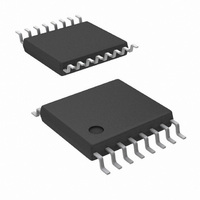
LM2653MTC-ADJ/NOPB
Manufacturer Part Number
LM2653MTC-ADJ/NOPB
Description
IC REGULATOR SWITCHING 16-TSSOP
Manufacturer
National Semiconductor
Type
Step-Down (Buck)r
Datasheet
1.LM2653MTCX-ADJNOPB.pdf
(12 pages)
Specifications of LM2653MTC-ADJ/NOPB
Internal Switch(s)
Yes
Synchronous Rectifier
Yes
Number Of Outputs
1
Voltage - Output
1.5 ~ 5 V
Current - Output
1.5A
Frequency - Switching
300kHz
Voltage - Input
4 ~ 14 V
Operating Temperature
-40°C ~ 125°C
Mounting Type
Surface Mount
Package / Case
16-TSSOP
Power - Output
893mW
Msl
MSL 1 - Unlimited
Power Dissipation Pd
893mW
Supply Voltage Range
4V To 14V
Termination Type
SMD
Driver Case Style
TSSOP
No. Of Pins
16
Rohs Compliant
Yes
Filter Terminals
SMD
Input Voltage Primary Max
14V
Leaded Process Compatible
Yes
No. Of Outputs
1
For Use With
LM2653-ADJEVAL - EVALUATION BOARD FOR LM2653-ADJ
Lead Free Status / RoHS Status
Lead free / RoHS Compliant
Other names
*LM2653MTC-ADJ
*LM2653MTC-ADJ/NOPB
LM2653MTC-ADJ
*LM2653MTC-ADJ/NOPB
LM2653MTC-ADJ
Available stocks
Company
Part Number
Manufacturer
Quantity
Price
Company:
Part Number:
LM2653MTC-ADJ/NOPB
Manufacturer:
NS/TI
Quantity:
1 100
www.national.com
Operation
CAPACITOR section for more information.) Toggling the in-
put supply voltage or the shutdown pin can reset the device
from the latched protection mode.
Design Procedure
This section presents guidelines for selecting external com-
ponents.
INPUT CAPACITOR
A low ESR aluminum, tantalum, or ceramic capacitor is
needed betwen the input pin and power ground. This capaci-
tor prevents large voltage transients from appearing at the
input. The capacitor is selected based on the RMS current
and voltage requirements. The RMS current is given by:
The RMS current reaches its maximum (I
V
the voltage rating should be at least 25% higher than the
maximum input voltage. If a tantalum capacitor is used, the
voltage rating required is about twice the maximum input
voltage. The tantalum capacitor should be surge current
tested by the manufacturer to prevent shorted by the inrush
current. It is also recommended to put a small ceramic
capacitor (0.1 µF) between the input pin and ground pin to
reduce high frequency spikes.
INDUCTOR
The most critical parameters for the inductor are the induc-
tance, peak current and the DC resistance. The inductance
is related to the peak-to-peak inductor ripple current, the
input and the output voltages:
A higher value of ripple current reduces inductance, but
increases the conductance loss, core loss, current stress for
the inductor and switch devices. It also requires a bigger
output capacitor for the same output voltage ripple require-
ment. A reasonable value is setting the ripple current to be
30% of the DC output current. Since the ripple current in-
creases with the input voltage, the maximum input voltage is
always used to determine the inductance. The DC resistance
of the inductor is a key parameter for the efficiency. Lower
DC resistance is available with a bigger winding area. A good
tradeoff between the efficiency and the core size is letting the
inductor copper loss equal 2% of the output power.
OUTPUT CAPACITOR
The selection of C
output voltage ripple. The output ripple in the constant fre-
quency, PWM mode is approximated by:
The ESR term usually plays the dominant role in determining
the voltage ripple. A low ESR aluminum electrolytic or tanta-
lum capacitor (such as Nichicon PL series, Sanyo OS-CON,
Sprague 593D, 594D, AVX TPS, and CDE polymer alumi-
IN
equals 2V
OUT
. For an aluminum or ceramic capacitor,
OUT
(Continued)
is driven by the maximum allowable
OUT
/2) when
8
PGOOD FLAG
The PGOOD flag goes low whenever the overvoltage or
undervoltage latch protection is enabled.
num) is recommended. An electrolytic capacitor is not rec-
ommended for temperatures below −25˚C since its ESR
rises dramatically at cold temperature. A tantalum capacitor
has a much better ESR specification at cold temperature and
is preferred for low temperature applications.
The output voltage ripple in constant frequency mode has to
be less than the sleep mode voltage hysteresis to avoid
entering the sleep mode at full load:
BOOST CAPACITOR
A 0.1 µF ceramic capacitor is recommended for the boost
capacitor. The typical voltage across the boost capacitor is
6.7V.
SOFT-START CAPACITOR
A soft-start capacitor is used to provide the soft-start feature.
When the input voltage is first applied, or when the SD(SS)
pin is allowed to go high, the soft-start capacitor is charged
by a current source (approximately 2 µA). When the SD(SS)
pin voltage reaches 0.6V (shutdown threshold), the internal
regulator circuitry starts to operate. The current charging the
soft-start capacitor increases from 2 µA to approximately
10 µA. With the SD(SS) pin voltage between 0.6V and 1.3V,
the level of the current limit is zero, which means the output
voltage is still zero. When the SD(SS) pin voltage increases
beyond 1.3V, the current limit starts to increase. The switch
duty cycle, which is controlled by the level of the current limit,
starts with narrow pulses and gradually gets wider. At the
same time, the output voltage of the converter increases
towards the nominal value, which brings down the output
voltage of the error amplifier. When the output of the error
amplifier is less than the current limit voltage, it takes over
the control of the duty cycle. The converter enters the normal
current-mode PWM operation. The SD(SS) pin voltage is
eventually charged up to about 2V.
The soft-start time can be estimated as:
During start-up, the internal circuit is monitoring the soft-start
voltage. When the softstart voltage reaches 2V, the under-
voltage and overvoltage protections are enabled.
If the output voltage doesn’t rise above 80% of the normal
value before the soft-start reaches 2V. The undervoltage
protection will kick in and shut the device down. You can
avoid this by either increasing the value of the soft-start
capacitor, or using a LDELAY capacitor.
LDELAY CAPACITOR
As mentioned in the operation section, the LDELAY capaci-
tor sets the time delay between the output voltage goes
below 80% of its nominal value and the undervoltage latch
protection is enabled.
Charging the CDELAY by a 5 µA current source up to 2V
sets the delay time. Therefore, T
The undervoltage protection is disabled by tying the LDELAY
pin to the ground.
T
SS
= C
SS
V
RIPPLE
* 0.6V/2 µA + C
<
20mV * V
SS
DELAY
OUT
* (2V−0.6V)/10 µA
= C
/V
FB
DELAY
* 2V/5µA.