TL75 Fluke Electronics, TL75 Datasheet - Page 46
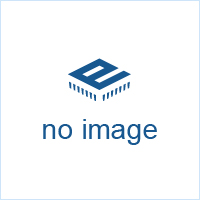
TL75
Manufacturer Part Number
TL75
Description
TEST LEAD SET HARD POINT
Manufacturer
Fluke Electronics
Series
Hard Point™r
Datasheet
1.BP880.pdf
(72 pages)
Specifications of TL75
Current Rating
10A
Termination
Banana Plug, Sheathed, Right Angle
Color
Black and Red - Plugs, Probes and Wire
Cable Length
48.000" (1219.20mm)
Ratings
CAT IV, 600V; CAT III, 1000V
Wire Insulation Material
PVC
Includes
Pin Tip
Lead Free Status / RoHS Status
Lead free by exemption / RoHS compliant by exemption
Voltage - Max
-
Impedance
-
Other names
855705
Available stocks
Company
Part Number
Manufacturer
Quantity
Price
Part Number:
TL750L05
Manufacturer:
TI/德州仪器
Quantity:
20 000
Company:
Part Number:
TL750L05CDR
Manufacturer:
TexasInstrum
Quantity:
1 520
Part Number:
TL750L05CDR
Manufacturer:
TI/德州仪器
Quantity:
20 000
Part Number:
TL750L05CDRG4
Manufacturer:
T
Quantity:
20 000
Company:
Part Number:
TL750L05CKC
Manufacturer:
TI
Quantity:
3 488
Company:
Part Number:
TL750L05CKCS
Manufacturer:
DIODES
Quantity:
20 000
Company:
Part Number:
TL750L05CKTTR
Manufacturer:
TI
Quantity:
50 210
Company:
Part Number:
TL750L05CKVUR
Manufacturer:
TI
Quantity:
50 210
Part Number:
TL750L05CP
Manufacturer:
TI/德州仪器
Quantity:
20 000
Part Number:
TL750L08CDR
Manufacturer:
TI/德州仪器
Quantity:
20 000
6
Features – Ti40 and Ti50 Series Imagers
Fluke Ti40, Ti45,
Ti50, Ti55
Fluke Ti40FT, Ti45FT,
Ti50FT, Ti55FT
Complete package
The IR FlexCam thermal imagers are
delivered as a complete package.
Thermal Imaging
Features
Choice of 3 interchangeable lenses to cover every application
Large 5” high contrast color LCD for a clear picture independent of
lighting conditions
Fully radiometric for detailed temperature analysis and tracking
SmartFocus for best image quality and accurate temperature measurements
Windows
Personalized instrument set-up for multiple use
CompactFlash memory cards to store over 1000 IR images plus fully
radiometric temperature data
SmartView reporting and analysis software included
AutoCapture for making intermittent problems visible
On-board analysis functions
User defined text annotations for simplified reporting
Built-in visible light (digital) camera
IR-Fusion blending thermal and visible light images to easily pinpoint
suspect components
IR/Visible Alarm
Laser pointer for easy targeting
Flash and torch light for high quality images in dark environments
180° articulating flexible lens to view images in every situation
FlexCam
®
CE based menu structure for ease of use
Ti40 and Ti50 Series IR
professionals demanding the best
®
Thermal Imagers
The thermal imagers for
To find the best thermal imaging solution
for your application go to our Thermal
Imaging Web Selection Guide at
www.fluke.com/thermal_imaging
FIND problems faster with
Fluke thermal imagers.
Reduce costs and maximize uptime
with our complete range of imaging
solutions. They combine the largest,
sharpest images in the industry with
innovative, easy-to-use features. Fluke
Ti40 and Ti50 Series reveal more
with IR Fusion
infrared and visible light images in
one display. Fluke puts powerful
technology within your reach.
FT model
FT model
FT model
FT model
Picture-
picture
Ti0
only
in-
•
•
•
•
•
•
•
•
•
FT model
FT model
FT model
FT model
FT model
®
Ti5
Technology—merging
•
•
•
•
•
•
•
•
•
•
•
•
FT model
FT model
FT model
FT model
FT model
Ti50
•
•
•
•
•
•
•
•
•
FT model
FT model
FT model
FT model
FT model
Ti55
•
•
•
•
•
•
•
•
•
•
•
•
IR-Fusion
IR-Fusion technology simultaneously
captures pixel-for-pixel infrared and vis-
ible light images and allows full image
optimization with 5 different on-camera
as well as software viewing modes. With
the integrated laser pointer visible on
the images, precise and accurate (faulty)
component identification is very easy.
Full IR
Alpha Blending
Full Visible Light
Application note, literature code
2764017:
Thermography at Ford’s
Dearborn Stamping Plant
The Dearborn
Stamping Plant
has had thermal
cameras on site
in the past, but
has not met
the objectives
of a successful
thermography
program. Today,
DSP’s thermog-
raphy program
is a model for
the rest of Ford,
and the program
came on line in a matter of weeks.
Want to read more? Download
this and other application notes
at www.fluke.com/library
™
Technology
Thermography at Ford’s
Dearborn Stamping Plant:
From start to best-in-Ford in
30 days—and still accelerating
The Dearborn Stamping Plant has had thermal cameras
on site in the past, but has not met the objectives of a
successful thermography program. Today, DSP’s ther-
mography program is a model for the rest of Ford, and
the program came on line in a matter of weeks.
caption
F r o m t h e F l u k e D i g i t a l L i b r a r y @ w w w . f l u k e . c o m / l i b r a r y
Picture-in-Picture
IR/Visible Alarm
Lately, there has been a stream
of visitors to the Dearborn
Stamping Plant (DSP) housed in
the historic Ford Rouge Center
in Dearborn, Michigan. What’s
the attraction? The DSP opera-
tion, which manufactures sub-
assembly doors and hoods for
the popular Ford F-150 pickup
truck, achieved a perfect score in
a recent independent audit of its
weld effectiveness. That makes
the plant best in company—
perhaps the best period—when
it comes to the precision with
which it forms and welds sub-
assemblies. Executives from Ford
Motor Company corporate offices
and management from other Ford
operations want to know how
they do it.
tion-monitoring program using
thermography or thermal imag-
ing. Thermography itself isn’t
new to DSP or new to Ford
operations, but the DSP thermog-
raphy program is unique. After
only 30 days, the program scored
higher in an insurance audit
than any other Ford thermogra-
phy program had ever scored. It
continued to work even when
new thermography team mem-
bers came on board. In the best
tradition of Ford’s commitment to
continuous improvement, DSP’s
thermography program keeps
getting better. And possibly the
most distinctive aspect: the pro-
gram is designed around a sys-
tems approach and supported by
a systems solution. That means
it has the potential to be quickly
and easily replicated and the
possibility of being deployed
with equal success and equiva-
lent return on investment in any
Ford operation.
A significant factor is a condi-
Application Note