NCP5810DMUTXG ON Semiconductor, NCP5810DMUTXG Datasheet - Page 11
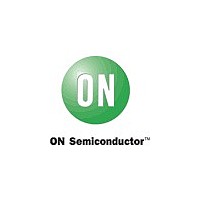
NCP5810DMUTXG
Manufacturer Part Number
NCP5810DMUTXG
Description
IC, DUAL DC/DC CONVERTER, µDFN-12
Manufacturer
ON Semiconductor
Datasheet
1.NCP5810DGEVB.pdf
(14 pages)
Specifications of NCP5810DMUTXG
Primary Input Voltage
4.6V
No. Of Outputs
2
Output Voltage
4.6V
No. Of Pins
12
Operating Temperature Range
-40°C To +85°C
Switching Frequency Max
1700kHz
Termination Type
SMD
Mounting Style
SMD/SMT
Package / Case
UDFN EP
Lead Free Status / RoHS Status
Lead free / RoHS Compliant
Lead Free Status / RoHS Status
Lead free / RoHS Compliant
Available stocks
Company
Part Number
Manufacturer
Quantity
Price
Company:
Part Number:
NCP5810DMUTXG
Manufacturer:
ON
Quantity:
28 800
Part Number:
NCP5810DMUTXG
Manufacturer:
ON/安森美
Quantity:
20 000
voltage operation setup. For example, if one needs V
= -5.4 V, V
zener diodes include but are not limited to:
Enable
converter. An active high logic level on this pin enables the
device. A built-in pull-down resistor disables the device if
the pin is left open.
True Shut Down
and truly isolates the battery from the output. The True shut
down eliminates the leakage current from the battery to the
load and significantly reduces battery consumption during
disable condition, thus increasing battery life.
Inrush Current Limiting Circuitry
unknown whether the output capacitor COUTP is charged
or discharged. If the output capacitor is discharged, a
common boost converter shows high inductor inrush
current at start-up. The internal circuitry of the NCP5810D
has been carefully designed to limit the amplitude of the
inrush current at start-up.
Thermal Shutdown
the power section of the device is disabled. Normal
operation will resume when the junction temperature drops
below 150°C (nom).
Design Procedure
Buck-Boost Inverter Output Voltage Setting
adjusted using external feedback resistors, and can be set
from -2 V down to -15 V. Unlike for the boost converter,
the lower feedback resistor R2 does not use the ground as
a reference but uses the reference voltage (nom 1.265 V).
R2 is placed between the feedback pin FBN (nom 632 mV)
and the reference pin REF. As for the boost converter, the
current flowing out of the feedback resistors must be as low
as possible to ensure high efficiency in low load conditions.
Nevertheless the feedback resistor impedance must not be
Zener voltage must choose to be 25 % above steady state
ON SEMICONDUCTOR: MM3Z6V8T1
This input logic allows enabling and disabling the
When in disable condition, the switch MP0 is turned off
Before the NCP5810D boost converter is turned on, it is
When the IC junction temperature exceeds 165°C (nom),
The output voltage of the buck-boost inverter is also
Z
R2
= 5.4 + 25 % = 6.8 V. Some recommended
Figure 17. Zener Protection
FBN
7
SWN
C6
R1
10
L2
4.7 μH
D1
4.7 μF
C4
MM3Z_XX
VOUTN
D2
http://onsemi.com
OUTN
NCP5810D
11
too high to keep good voltage accuracy. Therefore it is
recommended to use values in the 10 kW to 100 kW range
for the lower resistor R2. The upper feedback resistor R1
can calculated using the following equation:
56 kW ±1% is selected of R2, R1 should be selected
according to the following equation:
Components Selection
Inductor Selection
considered when selecting an inductor, the absolute value
of the inductor, the saturation current and the DCR. During
normal operation, the NCP5810D is intended to operate in
Continuous Conduction Mode (CCM). The two equations
below can be used to calculate the peak current for each
converters:
For the boost converter
For the buck-boost inverter
current, L the inductor value, F the switching frequency,
and D
current. A good approximation is to use h = 0.8 from the
boost and h = 0.75 for the buck-boost inverter. It is
important to ensure that the inductor current rating is high
enough such that it not saturate. As the inductor size is
reduced, the peak current for a given set of conditions
increases along with higher current ripple so it is not
possible to deliver maximum output power at lower
inductor values. Finally an acceptable DCR must be
selected regarding losses in the coil and must be lower than
300 mW to limit excessive voltage drop. In addition, as
DCR is reduced, overall efficiency will improve. The
inductor value should range between 2.7 mH and 6.8 mH,
typically for each DC/DC converter, it is recommended to
use a 4.7 mH low profile inductor. Some recommended
inductors include but are not limited to:
For example, should one need –5.4 V for V
Three different electrical parameters need to be
Where V
The global converter efficiency h varies with load
X
R
the duty cycle.
I
1
I
PEAK_N
PEAK_P
+ 56
IN
But : V
So: R
R
is the battery voltage, I
1
+
+
+ R
h
h
1
1 ) 2
FBN
I
N
P
OUT_N
2
+ R
I
OUT_P
+
(1 * D
(1 * D
1.265
2
V
V
V
OUTN
REF
5.4
2
FBN
D
1 )
N
P
N
)
)
* V
+ 536 kW "1%
* V
)
)
2
2
2
REF
V
V
FBN
OUT_X
V
IN
IN
V
REF
L
L
OUTN
P
N
D
D
P
N
is the load
F
OUTN
F
, if a