LM2737MTC National Semiconductor, LM2737MTC Datasheet - Page 11
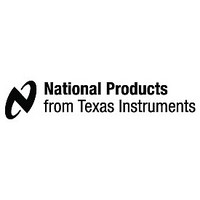
LM2737MTC
Manufacturer Part Number
LM2737MTC
Description
IC,SMPS CONTROLLER,VOLTAGE-MODE,BICMOS,TSSOP,14PIN,PLASTIC
Manufacturer
National Semiconductor
Datasheet
1.LM2737MTC.pdf
(22 pages)
Specifications of LM2737MTC
Rohs Compliant
NO
Available stocks
Company
Part Number
Manufacturer
Quantity
Price
Company:
Part Number:
LM2737MTC
Manufacturer:
nstion
Quantity:
370
Company:
Part Number:
LM2737MTC
Manufacturer:
NS
Quantity:
1 194
Part Number:
LM2737MTC
Manufacturer:
NS/国半
Quantity:
20 000
Company:
Part Number:
LM2737MTC/NOPB
Manufacturer:
MICREL
Quantity:
27
Part Number:
LM2737MTC/NOPB
Manufacturer:
TI/德州仪器
Quantity:
20 000
Company:
Part Number:
LM2737MTCX
Manufacturer:
MAXIM
Quantity:
50 000
Part Number:
LM2737MTCX
Manufacturer:
NS/国半
Quantity:
20 000
Company:
Part Number:
LM2737MTCX/NOPB
Manufacturer:
SONY
Quantity:
6 242
Part Number:
LM2737MTCX/NOPB
Manufacturer:
NS/国半
Quantity:
20 000
Application Information
DESIGN CONSIDERATIONS
The following is a design procedure for all the components
needed to create the circuit shown in Figure 3 in the Ex-
ample Circuits section, a 5V in to 1.2V out converter, capable
of delivering 10A with an efficiency of 85%. The switching
frequency is 300kHz. The same procedures can be followed
to create the circuit shown in Figure 3, Figure 4, and to
create many other designs with varying input voltages, out-
put voltages, and output currents.
INPUT CAPACITOR
The input capacitors in a Buck switching converter are sub-
jected to high stress due to the input current waveform,
which is a square wave. Hence input caps are selected for
their ripple current capability and their ability to withstand the
heat generated as that ripple current runs through their ESR.
Input rms ripple current is approximately:
The power dissipated by each input capacitor is:
Here, n is the number of capacitors, and indicates that power
loss in each cap decreases rapidly as the number of input
caps increase. The worst-case ripple for a Buck converter
occurs during full load, when the duty cycle D = 50%.
In the 5V to 1.2V case, D = 1.2/5 = 0.24. With a 10A
maximum load the ripple current is 4.3A. The Sanyo
10MV5600AX aluminum electrolytic capacitor has a ripple
current rating of 2.35A, up to 105˚C. Two such capacitors
make a conservative design that allows for unequal current
sharing between individual caps. Each capacitor has a maxi-
mum ESR of 18mΩ at 100 kHz. Power loss in each device is
then 0.05W, and total loss is 0.1W. Other possibilities for
input and output capacitors include MLCC, tantalum,
OSCON, SP, and POSCAPS.
INPUT INDUCTOR
The input inductor serves two basic purposes. First, in high
power applications, the input inductor helps insulate the
input power supply from switching noise. This is especially
important if other switching converters draw current from the
same supply. Noise at high frequency, such as that devel-
oped by the LM2727 at 1MHz operation, could pass through
the input stage of a slower converter, contaminating and
possibly interfering with its operation.
An input inductor also helps shield the LM2727 from high
frequency noise generated by other switching converters.
The second purpose of the input inductor is to limit the input
current slew rate. During a change from no-load to full-load,
the input inductor sees the highest voltage change across it,
equal to the full load current times the input capacitor ESR.
This value divided by the maximum allowable input current
slew rate gives the minimum input inductance:
(Continued)
11
In the case of a desktop computer system, the input current
slew rate is the system power supply or "silver box" output
current slew rate, which is typically about 0.1A/µs. Total input
capacitor ESR is 9mΩ, hence ∆V is 10*0.009 = 90 mV, and
the minimum inductance required is 0.9µH. The input induc-
tor should be rated to handle the DC input current, which is
approximated by:
In this case I
TDK SLF12575T-1R2N8R2, a 1.2µH device that can handle
8.2Arms, and has a DCR of 7mΩ.
OUTPUT INDUCTOR
The output inductor forms the first half of the power stage in
a Buck converter. It is responsible for smoothing the square
wave created by the switching action and for controlling the
output current ripple. (∆I
selecting between tradeoffs in efficiency and response time.
The smaller the output inductor, the more quickly the con-
verter can respond to transients in the load current. As
shown in the efficiency calculations, however, a smaller in-
ductor requires a higher switching frequency to maintain the
same level of output current ripple. An increase in frequency
can mean increasing loss in the FETs due to the charging
and discharging of the gates. Generally the switching fre-
quency is chosen so that conduction loss outweighs switch-
ing loss. The equation for output inductor selection is:
Plugging in the values for output current ripple, input voltage,
output voltage, switching frequency, and assuming a 40%
peak-to-peak output current ripple yields an inductance of
1.5µH. The output inductor must be rated to handle the peak
current (also equal to the peak switch current), which is (Io +
0.5*∆I
152HC is 1.5µH, is rated to 15Arms, and has a DCR of 4mΩ.
OUTPUT CAPACITOR
The output capacitor forms the second half of the power
stage of a Buck switching converter. It is used to control the
output voltage ripple (∆V
fast load transients.
In this example the output current is 10A and the expected
type of capacitor is an aluminum electrolytic, as with the
input capacitors. (Other possibilities include ceramic, tanta-
lum, and solid electrolyte capacitors, however the ceramic
type often do not have the large capacitance needed to
supply current for load transients, and tantalums tend to be
more expensive than aluminum electrolytic.) Aluminum ca-
pacitors tend to have very high capacitance and fairly low
ESR, meaning that the ESR zero, which affects system
stability, will be much lower than the switching frequency.
The large capacitance means that at switching frequency,
the ESR is dominant, hence the type and number of output
capacitors is selected on the basis of ESR. One simple
formula to find the maximum ESR based on the desired
output voltage ripple, ∆V
ripple, ∆I
o
). This is 12A for a 10A design. The Coilcraft D05022-
o
, is:
IN-DC
is about 2.8A. One possible choice is the
o
o
) and to supply load current during
o
) The inductance is chosen by
and the designed output current
www.national.com