ADA4891-3 Analog Devices, ADA4891-3 Datasheet - Page 20
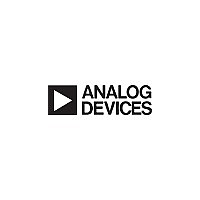
ADA4891-3
Manufacturer Part Number
ADA4891-3
Description
Low Cost CMOS, High Speed, Rail-to-Rail Amplifier (Triple)
Manufacturer
Analog Devices
Datasheet
1.ADA4891-3.pdf
(24 pages)
Specifications of ADA4891-3
-3db Bandwidth
220MHz
Slew Rate
170V/µs
Vos
2.5mV
Ib
2pA
# Opamps Per Pkg
3
Input Noise (nv/rthz)
9nV/rtHz
Vcc-vee
2.7V to 5.5V
Isy Per Amplifier
4.4mA
Packages
Mini-SO,SOP
ADA4891-1/ADA4891-2/ADA4891-3/ADA4891-4
LAYOUT, GROUNDING, AND BYPASSING
POWER SUPPLY BYPASSING
Power supply pins are additional op amp inputs, and care must
be taken so that a noise-free, stable dc voltage is applied. The
purpose of bypass capacitors is to create a low impedance path
from the supply to ground over a range of frequencies, thereby
shunting or filtering the majority of the noise to ground. Bypassing
is also critical for stability, frequency response, distortion, and
PSRR performance.
If traces are used between components and the package, chip
capacitors of 0.1 μF (X7R or NPO) are critical and should be
placed as close as possible to the amplifier package. The 0508
case size for such a capacitor is recommended because it offers
low series inductance and excellent high frequency performance.
Larger chip capacitors, such as 0.1 μF capacitors, can be shared
among a few closely spaced active components in the same
signal path. A 10 μF tantalum capacitor is less critical for high
frequency bypassing, but it provides additional bypassing for
lower frequencies.
GROUNDING
When possible, ground and power planes should be used. Ground
and power planes reduce the resistance and inductance of the
power supply feeds and ground returns. If multiple planes are
used, they should be stitched together with multiple vias. The
returns for the input, output terminations, bypass capacitors,
and R
Ground vias should be placed at the side or at the very end of
the component mounting pads to provide a solid ground return.
The output load ground and the bypass capacitor grounds should
be returned to a common point on the ground plane to minimize
parasitic inductance and to help improve distortion performance.
INPUT AND OUTPUT CAPACITANCE
Parasitic capacitance can cause peaking and instability and,
therefore, should be minimized to ensure stable operation.
High speed amplifiers are sensitive to parasitic capacitance between
the inputs and ground. A few picofarads of capacitance reduce
the input impedance at high frequencies, in turn increasing the
gain of the amplifier and causing peaking of the frequency
response or even oscillations, if severe enough. It is recommended
that the external passive components that are connected to the
input pins be placed as close as possible to the inputs to avoid
parasitic capacitance.
In addition, the ground and power planes under the pins of
the ADA4891 should be cleared of copper to prevent parasitic
capacitance between the input and output pins to ground. This
is because a single mounting pad on a SOIC footprint can add
as much as 0.2 pF of capacitance to ground if the ground or
power plane is not cleared under the ADA4891 pins. In fact, the
ground and power planes should be kept at a distance of at least
0.05 mm from the input pins on all layers of the board.
G
should all be kept as close to the ADA4891 as possible.
Rev. C | Page 20 of 24
INPUT-TO-OUTPUT COUPLING
To minimize capacitive coupling between the inputs and outputs
and to avoid any positive feedback, the input and output signal
traces should not be parallel. In addition, the input traces should
not be close to each other. A minimum of 7 mils between the
two inputs is recommended.
LEAKAGE CURRENTS
In extremely low input bias current amplifier applications, stray
leakage current paths must be kept to a minimum. Any voltage
differential between the amplifier inputs and nearby traces sets
up a leakage path through the PCB. Consider a 1 V signal and
100 GΩ to ground present at the input of the amplifier. The
resultant leakage current is 10 pA; this is 5× the typical input
bias current of the amplifier. Poor PCB layout, contamination,
and the board material can create large leakage currents. Common
contaminants on boards are skin oils, moisture, solder flux, and
cleaning agents. Therefore, it is imperative that the board be
thoroughly cleaned and that the board surface be free of
contaminants to take full advantage of the low input bias
currents of the ADA4891.
To significantly reduce leakage paths, a guard ring/shield should
be used around the inputs. The guard ring circles the input pins
and is driven to the same potential as the input signal, thereby
reducing the potential difference between pins. For the guard ring
to be completely effective, it must be driven by a relatively low
impedance source and should completely surround the input
leads on all sides, above and below, using a multilayer board
(see Figure 66).
The 5-lead SOT-23 package for the ADA4891-1 presents a
challenge in keeping the leakage paths to a minimum. The
pin spacing is very tight, so extra care must be used when
constructing the guard ring (see Figure 67 for the recom-
mended guard ring construction).
GUARD RING
OUT
–V
+IN
S
ADA4891-1
INVERTING
Figure 67. Guard Ring Layout, 5-Lead SOT-23
Figure 66. Guard Ring Configurations
INVERTING
–IN
+V
S
GUARD RING
OUT
–V
+IN
S
NONINVERTING
ADA4891-1
NONINVERTING
+V
–IN
S