lm2502sm National Semiconductor Corporation, lm2502sm Datasheet - Page 21
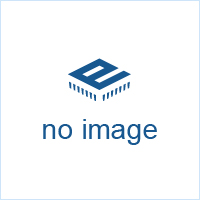
lm2502sm
Manufacturer Part Number
lm2502sm
Description
Mobile Pixel Link Mpl Display Interface Serializer And Deserializer
Manufacturer
National Semiconductor Corporation
Datasheet
1.LM2502SM.pdf
(27 pages)
Available stocks
Company
Part Number
Manufacturer
Quantity
Price
Company:
Part Number:
lm2502sm/NOPB
Manufacturer:
Texas Instruments
Quantity:
10 000
Company:
Part Number:
lm2502smX/NOPB
Manufacturer:
Texas Instruments
Quantity:
10 000
LM2502 Features and Operation
between 3 and 25 MHz. See Table 10 below, Multiplier/
Divisor times CLK rate must also be less than 76.8 MHz. The
76.8 MHz limitation is based on the semiconductor process
used on this implementation — it is not an MPL limitation.
Line rate should also be selected such that it is faster than
the input load rate when bursting data across the link. Oth-
erwise 8/10 X Line rate must be greater than the input load
rate to the Master. At the maximum raw data rate of 307
Mbps, the maximum information rate is 245 Mbps. Thus the
parallel load rate at the Master input must not exceed 15.4
Mega Transfers per second sustained (of 16 data bits). The
Master can accommodate up to four words at a higher rate
due to internal FIFOs.
Configuration pins (PLL_CON[2:0], and M/S*) are used to
determine the mode of which the part is operating in. In the
Slave configuration the PLL block is disabled. The Slave
PLL_CON pins are required to set up the proper divisor for
Application Information
SYSTEM CONSIDERATIONS
When employing the MPL SERDES chipset in place of a
parallel bus, a few system considerations must be taken into
account. Before sending commands (ie initialization com-
mands) to the display, the SERDES must be ready to trans-
mit data across the link. The MPL link must be powered up,
and the PLL must be locked. Also a review of the Slave
output timing should be completed to insure that the timing
parameters provided by the Slave output meet the require-
ments of the LCD driver input. Specifically, pulse width on
CSn*, RD* / WR*, data valid time, and bus cycle rate should
be reviewed and checked for inter-operability. Additional de-
tails are provided next:
The MPL link should be started up as follows: The chipset
should be powered up first, V
first, it may be at the same time as V
power up, the PD* inputs should be held LOW and released
once power is stable and within specification. The Slave PD*
may be released first or at the same time as the Master. CLK
should be applied prior to releasing PD*.
Before data can be sent across the MPL serial link, the link
must be ready for transmission. The CLK needs to be ap-
plied to the device, and the PLL locked. This is controlled by
a keep-off counter set for 4096 cycles. After the PLL has lock
(Continued)
PLLCON2
0
0
0
0
1
1
1
1
PLLCON1
0
0
1
1
0
0
1
1
DDIO
PLLCON0
should not be powered up
0
1
0
1
0
1
0
1
DD
/V
DDA
CLK X 2
CLK X 4
CLK X 6
CLK X 7
CLK X 8
CLK X 9
CLK X 10
or lag. During
TABLE 10. PLL_CON Settings
Multiplier
(Master)
MC out
21
the CLK pin. Slave PLL_CON[2:0] pins do not need to be set
the same as the Master, this allows for clock multiplication /
division to be supported for the output clock reference signal.
RESET
On both the Master and the Slave, the PD* pin resets the
logic. The PD* pins should be held low until the power supply
has ramped up and is stable and within specifications. The
Slave PD
as the Master. This will ensure that the Slave sees the start
up sequence from the Master.
MASTER/SLAVE SELECTION
The M/S* pin is used to configure the device as either a
Master or Slave device. When the M/S* pin is a Logic High,
the Master configuration is selected. The Driver block is
enabled for the MC line, and the MD lines. When the M/S*
pin is a Logic Low, the Slave configuration is selected. The
Receiver block is enabled for the MC line, and the MD lines.
and the counter expired, an additional 40 clock cycles are
required for the calibration of the MPL link. After this, data
may now be written to the device.
It takes 5MC Cycles to send a 16-bit CPU Write including the
serial overhead. The MC cycle time is calculated based on
the PLL_CON[2:0] setting and also the input clock fre-
quency. For example, a 19.2MHz input CLK and a 4X
PLLCON setting yields a MC frequency of 76.8MHz. Thus it
takes 65.1ns to send the word in serial form. To allow some
idle time between transmissions (this will force a bit sync per
word if the gap is long enough in between), the load rate on
the Master input should not be faster than 6MC cycles, or
every 78ns in our example to support a data pipe line. This is
sometimes referred to as the bus cycle time (time between
commands).
The Slave output times is also a function of MC cycles. Note
that in i80 mode, the width of the WR
the width of the CS
less of the pulse width applied to the Master input. System
designers need to check compatibility with the display driver
to ensure this pulse width meets its requirement. If it is too
fast, select a lower PLLCON setting or apply a slower input
clock.
The CLK input must be free running and not gapped. If the
clock is stopped a RESET (PD* = Low) cycle should be done
and the link brought up again.
MC / 2
MC / 4
MC / 6
MC / 7
MC / 8
MC / 9
MC / 10
CLKout
Divisor
(Slave)
*
pin should be driven High first or at the same time
*
) pulse low is three MC cycles regard-
13 MHz
6 MHz
3 MHz
3 MHz
3 MHz
3 MHz
3 MHz
CLK Input
Minimum
*
pulse (in m68 mode
25 MHz
19.2 MHz
12.8 MHz
10.97 MHz
9.60 MHz
8.53 MHz
7.68 MHz
(Reserved)
(MC % 76.8
CLK Input
Maximum
MHz)
www.national.com