PM6600 STMicroelectronics, PM6600 Datasheet - Page 30
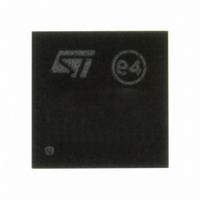
PM6600
Manufacturer Part Number
PM6600
Description
IC LED DRIVR WHT BCKLT 24-VFQFPN
Manufacturer
STMicroelectronics
Type
Backlight, White LEDr
Datasheet
1.PM6600TR.pdf
(60 pages)
Specifications of PM6600
Topology
PWM, Step-Up (Boost)
Number Of Outputs
6
Internal Driver
Yes
Type - Primary
Backlight
Type - Secondary
White LED
Frequency
200kHz ~ 1MHz
Voltage - Supply
4.7 V ~ 28 V
Voltage - Output
36V
Mounting Type
Surface Mount
Package / Case
24-VFQFN, 24-VFQFPN
Operating Temperature
-40°C ~ 85°C
Current - Output / Channel
32mA
Internal Switch(s)
Yes
Number Of Segments
60
Operating Supply Voltage
4.7 V to 28 V
Maximum Power Dissipation
2.3 W
Maximum Operating Temperature
+ 85 C
Mounting Style
SMD/SMT
Minimum Operating Temperature
- 40 C
For Use With
497-8414 - BOARD EVAL BASED ON PM6600
Lead Free Status / RoHS Status
Lead free / RoHS Compliant
Efficiency
-
Lead Free Status / Rohs Status
Details
Available stocks
Company
Part Number
Manufacturer
Quantity
Price
Company:
Part Number:
PM6600
Manufacturer:
FUJITSU
Quantity:
2 402
Company:
Part Number:
PM6600TR
Manufacturer:
ST
Quantity:
11 965
Company:
Part Number:
PM6600TR
Manufacturer:
st
Quantity:
5 145
Operation description
7.4
7.4.1
30/60
System stability
The boost section of the PM6600 is a fixed frequency, peak current-mode converter. During
normal operation, a minimum voltage selection circuit compares all the voltage drops across
the active current generators and provides the minimum one to the error amplifier. The
output voltage of the error amplifier determines the inductor peak current in order to keep its
inverting input equal to the reference voltage (400 mV typ). The compensation network
consists of a simple RC series (R
The calculation of R
dynamic performance of the boost converter and is strictly related to the operating
conditions.
Loop compensation
The compensation network can be quickly calculated using equations 4 through 9. Once
both R
order to get the optimal dynamic performance from the application.
The first parameter to be fixed is the switching frequency. Normally, a high switching
frequency allows reducing the size of the inductor but increases the switching losses and
negatively affects the dynamic response of the converter. For most of applications, the fixed
value (660 kHz) represents a good trade-off between power dissipation and dynamic
response, allowing to save an external resistor at the same time. In low-profile applications,
the inductor value is often kept low to reduce the number of turns; an inductor value in the
4.7 µH-15 µH range is a good starting choice.
Even if the loop bandwidth of the boost converter should be chosen as large as possible, it
should be set to 20% of the switching frequency, taking care not to exceed the CCM-mode
right half-plane zero (RHPZ).
Equation 7
Equation 8
Where V
Note that, the lower the inductor value (or the lower the switching frequency) the higher the
bandwidth can be achieved. The output capacitor is directly involved in the loop of the boost
converter and must be large enough to avoid excessive output voltage drop in case of a
sudden line transition from the maximum to the minimum input voltages (ΔV
exceed 50-100 mV):
COMP
IN,min
and C
is the minimum input voltage, I
COMP
COMP
have been determined, a fine-tuning phase may be required in
f
and C
U
≤
0
Doc ID 14248 Rev 7
2 .
COMP
M =
COMP
⋅
2
M
⋅ π
V
2
V
R
is fundamental to achieve optimal loop stability and
IN
L
OUT
- C
f
,
U
min
=
≤
COMP
0
0
2 .
2 .
R =
OUT
⋅
⋅
⎛
⎜ ⎜
⎝
) between the COMP pin and ground.
f
SW
V
V
V
IN
I
is the overall output current,
OUT
OUT
OUT
,
min
2
⋅ π
⎞
⎟ ⎟
⎠
2
⎛
⎜ ⎜
⎝
L
V
I
OUT
OUT
⎞
⎟ ⎟
⎠
OUT
should not
PM6600