LT1316CMS8#TR Linear Technology, LT1316CMS8#TR Datasheet - Page 7
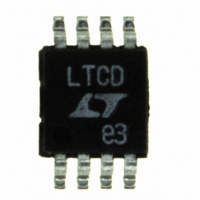
LT1316CMS8#TR
Manufacturer Part Number
LT1316CMS8#TR
Description
IC CONV DC/DC STEP UP 8MSOP
Manufacturer
Linear Technology
Type
Step-Up (Boost)r
Datasheet
1.LT1316CS8PBF.pdf
(16 pages)
Specifications of LT1316CMS8#TR
Internal Switch(s)
Yes
Synchronous Rectifier
No
Number Of Outputs
1
Voltage - Output
1.23 ~ 30 V
Current - Output
500mA
Voltage - Input
1.5 ~ 12 V
Operating Temperature
0°C ~ 70°C
Mounting Type
Surface Mount
Package / Case
8-MSOP, Micro8™, 8-uMAX, 8-uSOP,
Lead Free Status / RoHS Status
Contains lead / RoHS non-compliant
Power - Output
-
Frequency - Switching
-
Available stocks
Company
Part Number
Manufacturer
Quantity
Price
APPLICATIONS
then adding in the amount of overshoot that will occur due
to turn-off delay of the power transistor. This turn-off
delay is approximately 300ns.
Example:
Calculating Duty Cycle
For a boost converter running in continuous conduction
mode, duty cycle is constrained by V
to the equation:
where V
saturation voltage 0.2V.
If the duty cycle exceeds the LT1316’s minimum specified
duty cycle of 0.73, the converter cannot operate in con-
tinuous conduction mode and must be designed for
discontinuous mode operation.
Inductor Selection and Peak Current Limit for
Continuous Conduction Mode
Peak current and inductance determine available output
power. Both must be chosen properly. If peak current or
inductance is increased, output power increases. Once
output power or current and duty cycle are known, peak
current can be set by the following equation, assuming
continuous mode operation:
Inductance can now be calculated using the peak current:
Peak switch current = DC current limit from graph +
V
L = 33 H
= 18.2mA
(100mA – 18.2mA) 82mA
DC =
I
Set peak switch current to 100mA for: V
Overshoot = V
Refer to R
R
PEAK
IN
SET
/L(turn-off delay)
D
V
=
V
= diode voltage drop 0.4V and V
33k
OUT
OUT
2(I
1 – DC
SET
OUT
– V
– V
graph and locate
IN
)
SAT
/L(turn-off delay) = (2/33 H)(300ns)
U
IN
+ V
+ V
INFORMATION
D
U
D
IN
W
and V
OUT
IN
SAT
= 2V,
U
according
= switch
(1)
where t
As a result of equations 1 and 2, ripple current during
switching will be 40% of the peak current (see Figure 2).
Using these equations at the specified I
delivering approximately 60% of its maximum output
power. In other words, the part is operating on a 40%
reserve. This is a safe margin to use and can be decreased
if input voltage and output current are tightly controlled.
For some applications, this recommended inductor size
may be too large. Inductance can be reduced but available
output power will decrease. Also, ripple current during
switching will increase and may cause discontinuous
operation. Discontinuous operation occurs when
inductor current ramps down to zero at the end of each
switch cycle (see Figure 4). Shown in Figure 5 is minimum
inductance vs peak current for the part to remain in
continuous mode.
L =
100mA/DIV
INDUCTOR
CURRENT
SW PIN
5V/DIV
V
0mA
OFF
Figure 5. Minimum Inductance vs Peak Current
for Continuous Mode Operation
OUT
1000
100
0.4(I
Figure 4. Discontinuous Mode Operation
= 2 s and V
10
10
– V
5V TO 12V
PEAK
IN
2V TO 5V
+ V
)
PEAK CURRENT (mA)
D
D
= 0.4V.
(t
2 s/DIV
OFF
5V TO 18V
100
)
1316 F05
OUT
1000
1316 F04
, the part is
LT1316
7
(2)