LMZ14201TZ-ADJ/NOPB National Semiconductor, LMZ14201TZ-ADJ/NOPB Datasheet - Page 12
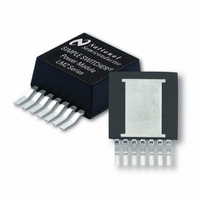
LMZ14201TZ-ADJ/NOPB
Manufacturer Part Number
LMZ14201TZ-ADJ/NOPB
Description
IC BUCK SYNC ADJ 1A TO-PMOD-7
Manufacturer
National Semiconductor
Series
SIMPLE SWITCHER®r
Type
Point of Load (POL) Non-Isolated with UVLOr
Datasheet
1.LMZ14201TZX-ADJNOPB.pdf
(18 pages)
Specifications of LMZ14201TZ-ADJ/NOPB
Output
0.8 ~ 6 V
Number Of Outputs
1
Power (watts)
6W
Mounting Type
Surface Mount
Voltage - Input
6 ~ 42 V
Package / Case
TO-PMOD-7, Power Module
1st Output
0.8 ~ 6 VDC @ 1A
Size / Dimension
0.40" L x 0.54" W x 0.18" H (10.16mm x 13.77mm x 4.57mm)
Power (watts) - Rated
6W
Operating Temperature
-40°C ~ 125°C
Efficiency
90%
Approvals
EN
Operating Temperature (max)
125C
Operating Temperature (min)
-40C
Pin Count
7
Mounting
Surface Mount
Case Length
10.16mm
Case Height
4.57mm
Screening Level
Automotive
Lead Free Status / RoHS Status
Lead free / RoHS Compliant
3rd Output
-
2nd Output
-
Lead Free Status / Rohs Status
Compliant
Other names
LMZ14201TZ-ADJTR
Available stocks
Company
Part Number
Manufacturer
Quantity
Price
Company:
Part Number:
LMZ14201TZ-ADJ/NOPB
Manufacturer:
INFINEON
Quantity:
100
Part Number:
LMZ14201TZ-ADJ/NOPB
Manufacturer:
TI/德州仪器
Quantity:
20 000
www.national.com
If ΔV
this equals 240 mV and f
C
≥
Additional bulk capacitance with higher ESR may be required
to damp any resonant effects of the input capacitance and
parasitic inductance of the incoming supply lines.
R
Many designs will begin with a desired switching frequency in
mind. For that purpose the following equation can be used.
f
This can be rearranged as
R
The selection of RON and f
tations in the on-time and off-time for the COT control section.
The on-time of the LMZ14201 timer is determined by the re-
sistor R
t
The inverse relationship of t
switching frequency as V
such that the on-time at maximum V
The on-timer has a limiter to ensure a minimum of 150 ns for
t
governed by the following equation:
f
This equation can be used to select R
frequency is desired so long as the minimum on-time of 150
ns is observed. The limit for R
R
If R
termined in (14) a lower frequency should be selected. Alter-
natively, V
frequency unchanged.
Additionally note, the minimum off-time of 260 ns limits the
maximum duty ratio. Larger R
lected in any application requiring large duty ratio.
Discontinuous Conduction and Continuous Conduction
Modes
At light load the regulator will operate in discontinuous con-
duction mode (DCM). With load currents above the critical
conduction point, it will operate in continuous conduction
mode (CCM). When operating in DCM the switching cycle
begins at zero amps inductor current; increases up to a peak
value, and then recedes back to zero before the end of the
off-time. Note that during the period of time that inductor cur-
rent is zero, all load current is supplied by the output capacitor.
The next on-time period starts when the voltage on the at the
FB pin falls below the internal reference. The switching fre-
quency is lower in DCM and varies more with load current as
compared to CCM. Conversion efficiency in DCM is main-
tained since conduction and switching losses are reduced
with the smaller load and lower switching frequency. Operat-
ing frequency in DCM can be calculated as follows:
f
In CCM, current flows through the inductor through the entire
switching cycle and never falls to zero during the off-time. The
switching frequency remains relatively constant with load cur-
rent and line voltage variations. The CCM operating frequen-
cy can be calculated using equation 7 above.
SW(CCM)
ON
ON
SW(MAX)
SW(DCM)
IN
ON
ON
ON
0.9μF
. This limits the maximum operating frequency, which is
≥
ON
= (1.3 * 10
RESISTOR SELECTION
≊
≥
IN
1A * 3.3V/24V * (1– 3.3V/24V) / (400000 * 0.240 V)
calculated in (11) is less than the minimum value de-
V
V
is 1% of V
ON
≊
O
= V
IN(MAX)
≊
V
/ (1.3 * 10
and the input voltage V
IN(MAX)
V
O
O
O
*(V
/ (V
/ (1.3 * 10
-10
* 150 nsec / (1.3 * 10
IN
* R
-1)*10μH*1.18*10
IN
IN(MAX)
can also be limited in order to keep the
for a 24V input to 3.3V output application
ON
-10
) / V
* f
-10
* 150 nsec) (13)
SW
IN
SW(CCM)
IN
* R
ON
SW(CCM)
is varied. R
= 400 kHz.
ON
(12)
and V
ON
ON
can be calculated as follows:
) (10)
IN
(lower F
(11)
. It is calculated as follows:
20
must be confined by limi-
IN
IN
*I
-10
ON
gives a nearly constant
is greater than 150 ns.
O
ON
) (14)
/(V
if a certain operating
should be selected
SW
IN
–V
) should be se-
O
)*R
ON
2
(15)
12
Following is a comparison pair of waveforms of the showing
both CCM (upper) and DCM operating modes.
The approximate formula for determining the DCM/CCM
boundary is as follows:
I
Following is a typical waveform showing the boundary condi-
tion.
The inductor internal to the module is 10 μH. This value was
chosen as a good balance between low and high input voltage
applications. The main parameter affected by the inductor is
the amplitude of the inductor ripple current (I
calculated with:
I
Where V
mined from equation 10.
If the output current I
I
aware that the lower peak of I
eration is required.
POWER DISSIPATION AND BOARD THERMAL
REQUIREMENTS
For the design case of V
(MAX)
thermal resistance from case to ambient of less than:
θ
DCB
LR P-P
L
CA
, the higher and lower peak of I
< (T
≊
= 85°C , and T
V
=V
O
J-MAX
*(V
O
IN
*(V
V
IN
is the maximum input voltage and f
IN
CCM and DCM Operating Modes
–V
IN
— T
V
= 12V, V
- V
IN
Transition Mode Operation
O
)/(2*10 μH*f
= 24V, V
AMB(MAX)
O
)/(10µH*f
JUNCTION
O
O
is determined by assuming that I
= 3.3V, I
IN
) / P
O
= 24V, V
= 3.3V, I
SW
= 125°C, the device must see a
SW(CCM)
LR
IC-LOSS
*V
must be positive if CCM op-
IN
O
LR
) (17)
= 1 A / 0.25 A
*V
O
O
can be determined. Be
- θ
= 0.29 A
= 3.3V, I
IN
JC
) (16)
(18)
30114612
30114614
LR
O
). I
SW
= 1A, T
LR
is deter-
can be
AMB
O
=