ISL6721EVAL3Z Intersil, ISL6721EVAL3Z Datasheet - Page 3
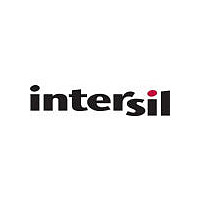
ISL6721EVAL3Z
Manufacturer Part Number
ISL6721EVAL3Z
Description
EVAL BOARD 3 FOR ISL6721
Manufacturer
Intersil
Specifications of ISL6721EVAL3Z
Lead Free Status / RoHS Status
Lead free / RoHS Compliant
duty cycle assumption of 40% corresponding to low line,
the minimum number of primary turns can be obtained
from Equation 4.
The number of turns on each secondary winding is
derived by the voltage seen across the respective
windings, which would be a diode drop (assumed to be
0.5V) greater than the nominal output voltage. In order
to generate output voltages that are close to the
specified values, the number of turns were rounded to
the following numbers:
• N
• N
• N
The outputs of the two secondary windings are calculated
in Equation 5.
Based on Equation 5, the actual maximum duty cycle can
be calculated as shown in Equation 6.
Now the actual maximum operation flux density can be
computed using Equation 2, to be approximately 123mT.
From the datasheet figures, the approximate core losses
for a 120mT change in flux density is about 1.24W.
To determine the wire gauge for the windings, skin effect
is an important consideration. The skin effect can be
calculated as shown in Equation 7.
Assuming a typical current density J
circular mils, the minimum effective cross-sectional area
of the primary windings can be computed to be 0.65,
where I
computed with an assumed typical efficiency of 86%.
Using 2 layers of 27AWG bifilar windings for the primary
winding, a current density of 1.6A per 500 circular mils
can be achieved. On similar lines, 2 layers of 27AWG
unifilar windings were used for the 12V output, and 1
layer of double-stranded 27AWG windings was used for
the 18V output.
The copper losses can be estimated by calculating the DC
and AC resistances, based on the core geometry and the
size of the wires selected. A detailed evaluation gives a
V
N
V
D
p
SEC1
SEC2
D
A
max
min
min
Skin
p
sec1
sec2
= 8 T
=
=
=
=
=
=
INAV
V
------------------------------------------------------ -
= 11 T
= 16 T
--------------------------------------- -
V
I
----------- -
12V
18V
in
--------------
J
in
in
2837
V
m
F
av
min
min
sec
dB
sw
+
is the average input current, that can be
+
=
1
•
I
max
I
•
1
=
2
•
2.58 500cirmils
---------------------------------------------- -
D
N
⋅
⋅
N
max
--------------------------
DCR
DCR
sec
•
p
300
2837
A
•
1
•
e
L1
×10
L2
1A
=
T
sw
----------------------- -
21.6 11
+
+
12.7 8
3
V
V
=
=
f
f
3
=
=
•
5.18
21.6 0.4
---------------------------------------------------- -
•
12.7V
18.75V
0.175 31e 6
=
≅
•
0.43
0.65
•
m
mils
•
3.3e 6
of 1A per 500
–
mm
Application Note 1491
–
2
=
5.3Turns
(EQ. 8)
(EQ. 7)
(EQ. 5)
(EQ. 6)
(EQ. 4)
copper loss estimate of about 0.68W. Assuming Eddy
current losses to be approximately half the copper
losses, the total loss in the transformer amounts to about
2.26W. The final transformer schematic is shown in
Figure 4 and the stack-up of the windings is illustrated in
Figure 5.
The main switching MOSFET was selected with
consideration of voltage and current stresses seen by the
device, and other factors such as thermal package and
cost. The peak voltage was assumed to be twice the
maximum input voltage, due to the ring during the
resonant reset period at a frequency set primarily by the
magnetizing and leakage inductance of the transformer,
the output capacitance, C
the transformer winding capacitance and other parasitic
elements on the node. With a maximum specified input
voltage of 52.8V, providing a design margin of 30%, a
150V device such as 2SK3593-01 need to be used. The
MOSFET losses comprise of conduction, switching and
gate drive losses. The conduction losses due to the FET
r
The switching losses due to the overlap between the
voltage and current waveforms is about 890mW
according to Equation 10, where x is typically a factor
between 4 and 6.
dsON
P
cond
FIGURE 5. TRANSFORMER WINDING STACK-UP
can be estimated as shown in Equation 9:
=
INSULATION TAPE
INSULATION TAPE
FIGURE 4. TRANSFORMER SCHEMATIC
16T X2 -27 AWG
11T X1 -27 AWG
11T X1 -27 AWG
8T X2 -27 AWG
6T X1 -30 AWG
8T X2 -27 AWG
I
PRIMARY
AUXILIARY
2
inRMS max
PR IMARY
8T
6T
•
R
dsON
oss
=
of the switching MOSFET,
2.58
PRIMARY – LAYER 1, PIN 2 TO 4
SECONDARY 18V, PIN 7 TO 8
SECONDARY 12V, - LAYER 1
SECONDARY 12V, - LAYER 2
PRIMARY – AUXILIARY WINDING
PRIMARY – LAYER 2, PIN 1 TO 3
SECONDARY
2
SECONDARY
•
37.5mΩ
18V
16T
12V
11T
=
250
(EQ. 9)
AN1491.0
mW