DC1298A-LA Linear Technology, DC1298A-LA Datasheet - Page 26
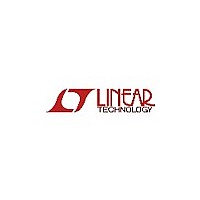
DC1298A-LA
Manufacturer Part Number
DC1298A-LA
Description
BOARD EVAL LTM9002-LA
Manufacturer
Linear Technology
Type
Baseband Receiverr
Specifications of DC1298A-LA
Design Resources
Demo Circuit 1298A Schematic
Frequency
0Hz ~ 300MHz
Features
LTM9002 14bit Dual Receiver Subsystem, DC-25MHz LPF
Tool / Board Applications
Wireless Connectivity-ZigBee, RF, Infrared, USB
Mcu Supported Families
LTM9002
Development Tool Type
Hardware - Eval/Demo Board
For Use With/related Products
LTM9002
Lead Free Status / RoHS Status
Not applicable / Not applicable
LTM9002
APPLICATIONS INFORMATION
the output busses are swapped and channel A comes
out on DBx; channel B comes out on DAx. To multiplex
both channels onto a single output bus, connect MUX,
CLKA and CLKB together (see the Timing Diagram for
the multiplexed mode.) The multiplexed data is available
on either data bus – the unused data bus can be disabled
with its OE pin.
Supply Sequencing
The V
auxiliary DAC while the V
ADC. The amplifi er, ADC and the DAC are separate integrated
circuits within the LTM9002; however, there are no supply
sequencing considerations beyond standard practice. It is
recommended that the amplifi er, ADC and DAC all use the
same low noise, 3.0V supply, but V
a different voltage level if desired. Both rails can operate
from the same 3.0V linear regulator but place a ferrite bead
between the V
can be used without additional supply sequencing circuitry
if they have common input supplies.
Grounding and Bypassing
The LTM9002 requires a printed circuit board with a
clean unbroken ground plane; a multilayer board with an
internal ground plane is recommended. The pinout of the
LTM9002 has been optimized for a fl ow-through layout
so that the interaction between inputs and digital outputs
is minimized. A continuous row of ground pads facilitate
a layout that ensures that digital and analog signal lines
are separated as much as possible.
The LTM9002 is internally bypassed with the ADC, (V
amplifi er and DAC (V
ground (GND). The digital output supply (OV
to OGND. Additional bypass capacitance is optional and
may be required if power supply noise is signifi cant.
The differential inputs should run parallel and close to each
other. The input traces should be as short as possible to
minimize capacitance and to minimize noise pickup.
26
CC
pin provides the supply to the amplifi er and the
CC
and V
CC
DD
) supplies returning to a common
DD
pins. Separate linear regulators
pin provides the supply to the
CC
may be operated from
DD
) is returned
DD
) and
Heat Transfer
Most of the heat generated by the LTM9002 is transferred
through the bottom-side ground pads. For good electrical
and thermal performance, it is critical that all ground pins
are connected to a ground plane of suffi cient area with as
many vias as possible.
Recommended Layout
The high integration of the LTM9002 makes the PC board
layout very simple and easy. However, to optimize its electri-
cal and thermal performance, some layout considerations
are still necessary.
• Use large PCB copper areas for ground. This helps
• Use multiple ground vias. Using as many vias as
• Separate analog and digital traces as much as pos-
The quality of the paste print is an important factor in
producing high yield assemblies. It is recommended to
use a type 3 or 4 printing no-clean solder paste. The solder
stencil design should follow the guidelines outlined in
Application Note 100.
The LTM9002 employs gold-fi nished pads for use with
Pb-based or tin-based solder paste. It is inherently Pb-free
and complies with the JEDEC (e4) standard. The materi-
als declaration is available online at http://www.linear.
com/leadfree/mat_dec.jsp.
to dissipate heat in the package through the board
and also helps to shield sensitive on-board analog
signals. Common ground (GND) and output ground
(OGND) are electrically isolated on the LTM9002, but
can be connected on the PCB underneath the part to
provide a common return path.
possible helps to improve the thermal performance
of the board and creates necessary barriers separat-
ing analog and digital traces on the board at high
frequencies.
sible, using vias to create high-frequency barriers.
This will reduce digital feedback that can reduce the
signal-to-noise ratio (SNR) and dynamic range of the
LTM9002.
9002f