220189-3 Tyco Electronics, 220189-3 Datasheet - Page 3
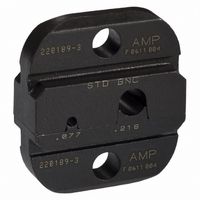
220189-3
Manufacturer Part Number
220189-3
Description
Crimp Tool Die
Manufacturer
Tyco Electronics
Series
PRO-CRIMPER IIr
Type
Dier
Datasheet
1.220189-1.pdf
(5 pages)
Specifications of 220189-3
Features
"O" / Military
Crimp Application
Coaxial
Connector Type
BNC
Crimp Handle
A9996-ND
Crimp Or Cable Size
RG/U-55, 58, 141, 142, 223, 303, 400, Belden 88240
Product
Tool Component
Description/function
O Military Type
Fits Cable/wire
55, 55A, 55B, 58, 58A, 58B, 58C, 141, 141A, 142, 142A, 142B, 223, 303, 400, Belden 88240, Berk-Tek BTDC-58, Comm/Scope 2135
For Use With
50 Ohm BNC RF/Coaxial Connectors
Lead Free Status / RoHS Status
na
Lead Free Status / RoHS Status
na, Not applicable / Not applicable
Other names
A24777
5. CRIMP HEIGHT ADJUSTMENT
The tool frame assembly ratchet mechanism features
an adjustment wheel with numbered settings. If the
crimp height is not acceptable, adjust the ratchet as
follows:
6. MAINTENANCE AND INSPECTION
6.1. Daily Maintenance
It is recommended that each operator of the tool with
the die assembly be made aware of, and responsible
for, the following four steps of daily maintenance:
Rev J
2. Slide the ferrule forward over the braid until the
ferrule butts against the shoulder on the connector
body.
3. Place the ferrule in the ferrule crimping chamber
of the anvil die so that the shoulder on the
connector body butts against the edge of the die.
See Figure 3.
4. Holding the assembly in place, close the tool
handles until the ratchet releases.
5. Remove crimped assembly from the crimping
dies.
1. Remove the lockscrew from the ratchet
adjustment wheel.
2. With a screwdriver, adjust the ratchet wheel
from the opposite side of the tool.
3. Observe the ratchet adjustment wheel. If a
tighter crimp is required, rotate the adjustment
wheel COUNTERCLOCKWISE to a
higher--numbered setting. If a looser crimp is
required, rotate the adjustment wheel
CLOCKWISE to a lower--numbered setting.
4. Replace the lockscrew.
5. Make a sample crimp and measure the crimp
height. If the crimp height is acceptable, secure the
lockscrew. If the dimension is unacceptable,
remove lockscrew and continue to adjust the
ratchet, and again measure a sample crimp.
1. Remove dust, moisture, and other contaminants
with a clean, soft brush, or a clean, soft, lint--free
cloth. Do NOT use any objects that could damage
the dies or tool.
2. Make sure that the proper die retaining screws
are in place and secured.
3. Make certain that all surfaces are protected with
a THIN coat of any good SAE 20 motor oil.
(Figure 4)
6.2. Periodic Inspections
Regular inspections should be performed by quality
control personnel. A record of scheduled inspections
should remain with the dies and/or be supplied to
supervisory personnel responsible for the dies.
Though recommendations call for at least one
inspection per month, the inspection frequency should
be based on amount of use, working conditions,
operator training and skill, and established company
standards. These inspections should be performed in
the following sequence:
A. Visual Inspection
B. Gaging the Crimping Chamber
This inspection requires the use of a plug gage
conforming to the diameters provided in Figure 5. TE
does not manufacture, or market, these gages.
Proceed as follows:
4. When the dies are not in use, mate and store
them in a clean, dry area.
1. Remove all lubrication and accumulated film by
immersing the dies in a suitable commercial
degreaser.
2. Make certain all die retaining screws and die
components are in place and secured. If
replacements are necessary, refer to Section 7,
REPLACEMENT.
3. Inspect the crimp area for flattened, chipped,
worn, cracked, or broken areas. If damage is
evident, the dies must be replaced (see Section 7,
REPLACEMENT).
1. Mate the dies until it is evident that they have
bottomed. Hold the dies in this position by holding
the tool handles closed with moderate pressure.
Lockscrew (Typ)
Ratchet
Adjustment
Wheel
Screwdriver
Figure 4
408- 2786
3 of 5