9473PC 3M, 9473PC Datasheet - Page 8
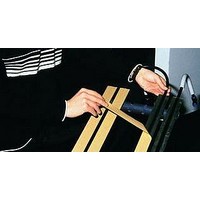
9473PC
Manufacturer Part Number
9473PC
Description
TAPE, FOAM, CLEAR, 2INX60YD
Manufacturer
3M
Datasheet
1.4943F.pdf
(10 pages)
Specifications of 9473PC
Roll Length
60yard
Leaded Process Compatible
No
Pack Quantity
1
Tape Type
Foam
Width
2"
Color
Clear
Lead Free Status / RoHS Status
Lead free / RoHS Compliant
3M
Design and Tape Selection Considerations
Choose the right tape for the substrate: Adhesives must flow onto the substrate surfaces in order to achieve intimate
contact area and allow the molecular force of attraction to develop. The degree of flow of the adhesive on the substrate
is largely determined by the surface energy of the substrate.
Use the right tape thickness: The necessary thickness of tape depends on the rigidity of substrates and their flatness
irregularity. While the 3M™ VHB™ Tapes will conform to a certain amount of irregularity, they will not flow to fill
gaps between the materials. For bonding rigid materials with normal flatness, consider use of tapes with thickness of 45
mils (1.1 mm) or greater. As the substrate flexibility increases thinner tapes can be considered.
Use the right amount of tape: Because 3M™ VHB™ Tapes are viscoelastic by nature their strength and stiffness is a
function of the rate at which they are stressed. They behave stronger with relatively faster rate of stress load (dynamic
stresses) and will tend to show creep behavior with stress load acting over a long period of time (static stresses). As a
general rule, for static loads, approximately four square inches of tape should be used for each pound of weight to be
supported in order to prevent excessive creep. For dynamic loads, the dynamic performance characteristics provided on
page 4 should be useful, factoring in the appropriate safety factors.
Allow for thermal expansion/contraction: 3M™ VHB™ Tapes can perform well in applications where two bonded
surfaces may expand and contract differentially. Assuming good adhesion to the substrates, the tapes can typically
tolerate differential movement in the shear plane up to 3 times their thickness.
Bond Flexibility: While an advantage for many applications where allowing differential movement is a benefit, the
tape bonds are typically more flexible than alternative bonding methods. Suitable design modifications or periodic use
of rigid fasteners or adhesives may be needed if additional stiffness is required.
Severe Cold Temperature: Applications which require performance at severe cold temperatures must be thoroughly
evaluated by the user if the intended use will subject the tape product to high impact stresses. A technical bulletin
“3M™ VHB™ Tape Cold Temperature Performance” (70-0707-3991-0) is available for additional information.
™
This illustration demonstrates the effect of surface energy on adhesive interfacial contact. High surface energy
materials draw the adhesive closer for high bond strength.
VHB
NOTES: There are a wide variety of formulations, surfaces finishes and surface treatments available on substrate materials which can affect adhesion. This chart is intended
100%
to provide only a rough estimate of the adhesion levels which can be expected on some common materials relative to a reference surface such as aluminum.
Light abrasion of surface will significantly increase adhesion levels on many materials, except when using tapes 4952/4932.
50%
Relationship of Adhesion and Surface Energy for 3M™ VHB™ Tape Adhesive Families
0%
™
Tapes
Aluminum
Stainless Steel
Copper
Zinc
Tin
Lead
Anodized Aluminum
Glass
High surface energy
400-1100
HIGH
Adhesive
Kapton
Phenolic
Nylon
Alkyd Enamel
Polyester
Epoxy Paint
Polyurethane
— Substrate
42-50
®
Surface Energy (Dynes/cm)
- 8 -
ABS
Polycarbonate (Lexan
PVC
Noryl
Acrylic
Polane
Powder Paint
®
MEDIUM
®
Paint
38-39
Low surface energy
®
)
Adhesive
PVA
Polystyrene
Acetal
Kynar
Powder Paint
36-37
®
Paint
— Substrate
NOTE: Low surface energy
adhesive may be less
affected by surface energy.
NOTE: Foam type can
affect and/or limit maximum
adheisve strength.
EVA
Polyethylene
Polypropylene
Tedlar
Silicone
PTFE
LOW
18-33
®