S1048-TAPE-1X100-FT Tyco Electronics, S1048-TAPE-1X100-FT Datasheet - Page 4
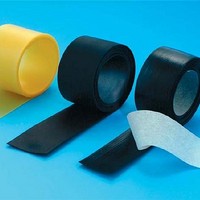
S1048-TAPE-1X100-FT
Manufacturer Part Number
S1048-TAPE-1X100-FT
Description
TAPE, SEALANT, THERMOPLASTIC, 1INX100FT
Manufacturer
Tyco Electronics
Specifications of S1048-TAPE-1X100-FT
Tape Backing Material
Thermoplastic
Roll Length
100ft
Adhesive Material
Thermoplastic
Tape Type
Sealing
Width
1"
Product
Tape
Size
1 in x 100 ft
Description/function
Hot Melt Polyolefin Adhesive
Lead Free Status / RoHS Status
Lead free / RoHS Compliant
Page 4
NOTE 4
If this document is printed it becomes uncontrolled. Check for the latest revision.
SOLVENT/FLUID RESISTANCE
Immerse three weighed specimens in each of the fluids specified. The volume of the fluids shall be not less
than 20 times that of the specimens. After the immersion, lightly wipe the specimens and air dry for 30 to 60
minutes at room temperature. Reweigh the specimens and calculate the percent weight uptake.
B)
Recover a 6-inch length of the specified heat shrinkable tubing on a glass-laminated plastic or a metal
tube 1 inch in diameter. Apply heat with a Thermofit 500A Thermogun equipped with a TG 13 reflector
and operating at 288 to 343°C (550 to 650°F). Cool the recovered tubing to room temperature. After
cooling, lightly abrade the outside of the recovered tubing and the insides of three 1-1/2 inch lengths of
the specified 1-1/2 inch diameter expanded tubing with No. 320 emery cloth. Wipe with a clean cloth or
paper towel wet with methyl ethyl ketone and allow sufficient time to dry. Spiral wrap the adhesive
tape, with a 50% overlap to produce a double thickness of adhesive, over the recovered tubing. Place a
strip of 3/4-inch-wide masking tape lengthwise over the adhesive tape to hold it in place and to provide
unbonded ends to insert into tensile tester. (Figure A).
Place three 1-1/2 inch lengths of the tubing, abraded on the inside, over the adhesive, as shown in Figure
A, and recover as described above. Continue heating for 30 seconds after the tubing has recovered.
Place the assembly in an oven for 10 minutes at 150 ± 3°C (302 ± 5°F) to assure uniform heating. Cool
to room temperature, and cut along one edge of the masking tape to remove the bonded assembly from
the mandrel (Figure B). Cut a specimen 1 inch wide (Figure C) from the center of each double
thickness.
Insert the unbonded ends of each specimen in the jaws of a tensile tester operating at a jaw separation
speed of 2 inches per minute. Make readings of peel strength at every 1/2 inch of jaw separation after 1
inch initial separation. The average of five readings shall define peel strength.
C)
Abrade an 6-inch length of 1-inch diameter aluminum pipe (2024 T-3 or equivalent) or steel pipe, (ASA-
B36.10-1939 or equivalent) with No. 320 emery cloth and wipe with a clean cloth or paper towel wet
with methyl ethyl ketone. Spiral wrap the adhesive tape on the pipe, with a 50% overlap to produce a
double thickness of adhesive. Place a strip of 3/4-inch-wide masking tape lengthwise over the adhesive
to hold it in place and to provide unbonded ends to insert into tensile tester. (Figure D)
Abrade, clean, recover and oven-heat three 1-1/2-inch lengths of 1-1/2 inch diameter
RNF-100 as described in Section B above. After cooling to room temperature, cut tubing into
1-inch wide sections (Figure D). Cut each specimen along the edge of the masking tape to free
unbonded ends of the tubing.
Place the specimen in a tensile testing machine, with the specimen around the positioning mandrel and
the free end of the specimen inserted into the tensile testing machine jaw. (Figure E) Construct the
holding fixture so that the yoke is free to rotate during testing. Test with a jaw-separation speed of 2
inches per minute. Take readings of peel strength at every 1/2 inch of jaw separation after 1 inch initial
separation. The average of five readings shall define peel strength.
Heat Shrinkable Tubing to Heat Shrinkable Tubing
Heat Shrinkable Tubing to Aluminum and Steel
SPECIFICATION RT-1050/3, Issue 4