A4940KLPTR-T Allegro Microsystems Inc, A4940KLPTR-T Datasheet - Page 11
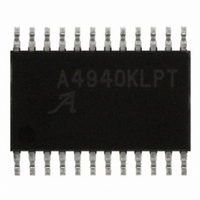
A4940KLPTR-T
Manufacturer Part Number
A4940KLPTR-T
Description
FULL BRIDGE MOSFET PRE-DRIVER
Manufacturer
Allegro Microsystems Inc
Datasheet
1.A4940KLPTR-T.pdf
(14 pages)
Specifications of A4940KLPTR-T
Configuration
H Bridge
Input Type
Non-Inverting
Delay Time
35ns
Number Of Configurations
1
Number Of Outputs
4
Voltage - Supply
5.5 V ~ 50 V
Operating Temperature
-40°C ~ 150°C
Mounting Type
Surface Mount
Package / Case
24-TSSOP Exposed Pad, 24-eTSSOP, 24-HTSSOP
Lead Free Status / RoHS Status
Lead free / RoHS Compliant
Current - Peak
-
High Side Voltage - Max (bootstrap)
-
Lead Free Status / RoHS Status
Lead free / RoHS Compliant
Other names
620-1319-2
Available stocks
Company
Part Number
Manufacturer
Quantity
Price
Company:
Part Number:
A4940KLPTR-T
Manufacturer:
ALLEGRO
Quantity:
356
Part Number:
A4940KLPTR-T
Manufacturer:
ALLEGRO/雅丽高
Quantity:
20 000
A4940
Supply Decoupling
Because this is a switching circuit, there are current spikes from
all supplies at the switching points. As with all such circuits, the
power supply connections should be decoupled with a ceramic
capacitor, typically 100 nF, between the supply pin and ground.
These capacitors should be connected as close as possible to the
device supply pins, VDD and VBB, and the ground pin, GND.
Power Dissipation
In applications where a high ambient temperature is expected the
on-chip power dissipation may become a critical factor. Careful
attention should be paid to ensure the operating conditions allow
the A4940 to remain in a safe range of junction temperature.
The power consumed by the A4940, P
given
where N is the quantity of MOSFETs switching during a PWM
cycle. N = 1 for slow decay with diode recirculation, N = 2 for slow
decay with synchronous rectification or fast decay with diode recir-
culation, and N = 4 for fast decay with synchronous rectification.
Layout Recommendations
Careful consideration must be given to PCB layout when designing
high frequency, fast switching, high current circuits. The following
Figure 2. Supply routing suggestions
P
SWITCHING
P
P
CPUMP
CPUMP
P
Ratio = 10 / (R
BIAS
P
I
av
D
= P
= V
= [(2 × V
= (V
= Q
= Q
BIAS
BB
GATE
GATE
BB
× I
– V
+P
GATE
BB
× N × f
× V
Controller Supply Ground
BB
REG
CPUMP
) – V
REG
+ 10)
) × I
REG
PWM
× N × f
R
+ P
av
DEAD
) × I
SWITCHING
PWM
av
D
, can be estimated by :
× Ratio
VREG
VDD
RDEAD
AGND
for V
for V
A4940
VBB
BB
BB
GHB
GHA
GND
GLA
GLB
Automotive Full Bridge MOSFET Driver
SA
SB
< 15 V
> 15 V
Optional reverse battery protection
are recommendations regarding some of these considerations:
• The A4940 ground, GND, and the high-current return of the ex-
• The exposed thermal pad should be connected to the GND pin
• Minimize stray inductance by using short, wide copper traces at
• Consider the use of small (100 nF) ceramic decoupling capaci-
• The ground connection to RDEAD should be connected inde-
• Supply decoupling for VBB, VREG, and VDD should be con-
Note that the above are only recommendations. Each application
is different and may encounter different sensitivities. A driver
running a few amps will be less susceptible than one running with
150 A and each design should be tested at the maximum current
to ensure any parasitic effects are eliminated.
ternal MOSFETs should return separately to the negative side of
the motor supply filtering capacitor. This minimizes the effect
of switching noise on the device logic and analog reference.
and may form part of the Controller Supply ground (see figure 2).
the drain and source terminals of all power MOSFETs. This in-
cludes motor lead connections, the input power bus, and the com-
mon source of the low-side power MOSFETs. This will minimize
voltages induced by fast switching of large load currents.
tors across the sources and drains of the power MOSFETs to
limit fast transient voltage spikes caused by the inductance of
the circuit trace.
pendently directly to the AGND pin. This sensitive component
should never be connected directly to the supply common or to
a common ground plane. It must be referenced directly to the
AGND pin.
nected to the Controller Supply ground which is independently
connected close to the GND pin. The decoupling capacitors should
also be connected as close as possible to the relevant supply pin.
Power Ground
115 Northeast Cutoff
1.508.853.5000; www.allegromicro.com
Allegro MicroSystems, Inc.
Worcester, Massachusetts 01615-0036 U.S.A.
+ Supply
Supply
Common
Motor
11