ATS667LSGTN-T Allegro Microsystems Inc, ATS667LSGTN-T Datasheet - Page 8
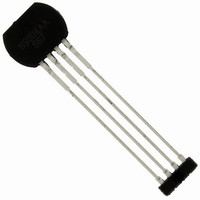
ATS667LSGTN-T
Manufacturer Part Number
ATS667LSGTN-T
Description
3-WIRE TRUE 0-SPEED HI ACCURACY GTS
Manufacturer
Allegro Microsystems Inc
Type
Special Purposer
Datasheet
1.ATS667LSGTN-T.pdf
(14 pages)
Specifications of ATS667LSGTN-T
Sensing Range
70% of Air Gap Trip, 30% of Air Gap Release
Voltage - Supply
4 V ~ 24 V
Current - Supply
12mA
Current - Output (max)
25mA
Output Type
Digital, Open Collector
Features
Gear Tooth Type
Operating Temperature
-40°C ~ 150°C
Package / Case
4-SIP
Operating Supply Voltage (min)
4V
Operating Supply Voltage (typ)
5/9/12/15/18V
Operating Supply Voltage (max)
24V
Output Current
20mA
Package Type
SIP Module(SG)
Pin Count
4
Mounting
Through Hole
Operating Temp Range
-40C to 150C
Operating Temperature Classification
Automotive
Lead Free Status / RoHS Status
Lead free / RoHS Compliant
Lead Free Status / RoHS Status
Lead free / RoHS Compliant
Other names
620-1328-2
ATS667LSG
Hall Technology
The ATS667 contains a single-chip differential Hall-effect sensor
IC, a samarium cobalt pellet, and a flat ferrous pole piece (con-
centrator). As shown in figure 1, the Hall IC supports two Hall
elements, which sense the magnetic profile of the ferrous gear
target simultaneously, but at different points (spaced at a 2.2 mm
pitch), generating a differential internal analog voltage, V
that is processed for precise switching of the digital output signal.
The Hall IC is self-calibrating and also possesses a tempera-
ture compensated amplifier and offset cancellation circuitry. Its
voltage regulator provides supply noise rejection throughout the
operating voltage range. Changes in temperature do not greatly
affect this device due to the stable amplifier design and the offset
compensation circuitry. The Hall transducers and signal process-
ing electronics are integrated on the same silicon substrate, using
a proprietary BiCMOS process.
Target Profiling During Operation
An operating device is capable of providing digital information
that is representative of the mechanical features of a rotating gear.
The waveform diagram in figure 3 presents the automatic transla-
tion of the mechanical profile, through the magnetic profile that
it induces, to the digital output signal of the ATS667. No addi-
tional optimization is needed and minimal processing circuitry is
required. This ease of use reduces design time and incremental
Figure 1. Relative motion of the target is detected by the dual Hall
elements mounted on the Hall IC.
Figure 2. This left-to-right (pin 1 to pin 4) direction of target rotation results
in a high output state when a tooth of the target gear is nearest the
package face (see figure 3). A right-to-left (pin 4 to pin 1) rotation inverts
the output signal polarity.
Hall Effect Device
Target (Gear)
Hall Element 2
Dual-Element
Rotating Target
(Pin 4 Side)
South Pole
North Pole
True Zero-Speed, High Accuracy Gear Tooth Sensor IC
1
4
(Pin 1 Side)
(Concentrator)
Element Pitch
Hall Element 1
Hall IC
Pole Piece
Back-biasing
Rare-earth Pellet
Case
Branded Face
of Package
Functional Description
PROC
,
assembly costs for most applications.
Determining Output Signal Polarity
In figure 3, the top panel, labeled Mechanical Position, represents
the mechanical features of the target gear and orientation to the
device. The bottom panel, labeled IC Output Signal, displays the
square waveform corresponding to the digital output signal that
results from a rotating gear configured as shown in figure 2, and
electrically connected as in figure 6. That direction of rotation (of
the gear side adjacent to the package face) is: perpendicular to
the leads, across the face of the device, from the pin 1 side to the
pin 4 side. This results in the IC output switching from low state
to high state as the leading edge of a tooth (a rising mechanical
edge, as detected by the IC) passes the package face. In this con-
figuration, the device output switches to its high polarity when a
tooth is the target feature nearest to the package. If the direction
of rotation is reversed, so that the gear rotates from the pin 4 side
to the pin 1 side, then the output polarity inverts. That is, the out-
put signal goes high when a falling edge is detected, and a valley
is nearest to the package.
Figure 3. The magnetic profile reflects the geometry of the target, allowing
the ATS667 to present an accurate digital output response.
sensed earlier
+B
Mechanical Position (Target movement pin 1 to pin 4)
Target Magnetic Profile
Package Orientation to Target
IC Internal Differential Analog Signal, V
IC Internal Switch State
IC Output Signal, V
This tooth
Branded Face
B
B
RP(#1)
On
OP(#1)
Pin 4
Side
OUT
(Package Top View)
Sensor Branded Face
115 Northeast Cutoff
1.508.853.5000; www.allegromicro.com
Back-Biasing
Allegro MicroSystems, Inc.
Worcester, Massachusetts 01615-0036 U.S.A.
Off
Pellet
Target
(Gear)
IC
B
B
RP(#2)
On
OP(#2)
PROC
Pin 1
Side
Hall Element Pitch
Off
This tooth
sensed later
8