ADP3810AR-16.8 Analog Devices Inc, ADP3810AR-16.8 Datasheet - Page 7
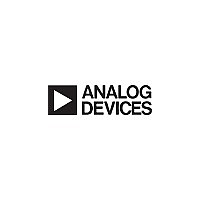
ADP3810AR-16.8
Manufacturer Part Number
ADP3810AR-16.8
Description
Manufacturer
Analog Devices Inc
Type
Battery Chargerr
Datasheet
1.ADP3810AR-16.8.pdf
(14 pages)
Specifications of ADP3810AR-16.8
Output Voltage
16.8V
Operating Supply Voltage (min)
2.7V
Operating Supply Voltage (max)
16V
Operating Temp Range
-40C to 85C
Package Type
SOIC N
Mounting
Surface Mount
Pin Count
8
Operating Temperature Classification
Industrial
Lead Free Status / Rohs Status
Not Compliant
The ADP3810/ADP3811 does not include circuitry to detect
nation schemes are required, a low cost micro controller can be
ADP3810, with its accurate reference and internal resistors, ac-
reducing the battery's run time and the end equipment's operat-
ing time.
charge
common for NiCad and NiMH batteries. If such charge termi-
added to the system to monitor the battery voltage and tempera-
ture. A PWM output from the microcontroller can subsequently
feedback loop.
Each GM stage is designed to be asymmetrical so that each am-
plifier can only source current. The outputs are tied together at
the CaMP node and loaded with an internal constant current
sink of approximately 100 IJA. Whichever amplifier sources
more current controls the voltage at the CaMP node and there-
fore controls the feedback. This scheme is a realization of an
analog "OR" function where GMI or GM2 has control of the
dc-dc converter and the charging circuitry. Whenever the cir-
cuit is in full current limiting or full voltage limiting, the respec-
tive GM stage sources an identical amount of current to the
fixed current sink. The other GM stage sources zero current
and is out of the loop. In the transition region, both GM stages
source some of the current to comprise the full amount of the
current sink. The high gains of GMI and GM2 ensure a
smooth but sharp transition from current control to voltage con-
trol. Figure 24 shows a graph of the transition from current to
voltage mode, that was measured on the circuit in Figure 23 as
detailed below. Notice that the current stays at its full pro-
grammed leveluntil the battery is within 200 mV of the final pro-
grammed voltage (10 V in this case), which maintains fast
charging through almost all of the battery voltage range. This
improves the speed of charging compared to a scheme that re-
duces the current at lower battery voltages.
The second element in a battery charging system is some form
of a dc-dc converter. To achieve high efficiency, the dc-dc con-
verter can be an isolated off-line switching power supply, or it
can be an isolated or nonisolated Buck or other type of switch-
ing power supply. For lower efficiency requirements, a linear
regulator fed from a wall adapter can be used. In the above dis-
cussion, the current, loUT,controls the duty cycle of a switching
supply; but in the case of the linear regulator, louT controls the
pass transistor drive. Examples of these topologies are shown
later in this data sheet. If an off-line supply such as a flyback
converter is used, and isolation between the control logic and
the ADP3810/ADP3811 is required, an optocoupler can be in-
serted between the ADP38 10/ADP38 I I output and the control
input of the primary side PWM.
Charge Termination
If the system is charging a Lilon battery, the main criteria to de-
termine charge termination is the absolute battery voltage. The
complishes this task. The ADP3810's guaranteed accuracy
specification of :t I % of the final battery voltage ensures that a
Lilon battery will not be overcharged. This is especially impor-
tant with Lilon batteries because overcharging can lead to cata-
strophic failure. It is also important to insure that the battery be
charged to a voltage equal to its optimal final voltage (typically
4.2 V per cell). Stopping at less than I % of full-scale results in
a battery that has not been charged to its full mAh capacity,
REV. 0
current loop, the higher louT reduces the duty cycle of the dc-dc
converter and causes the battery voltage to fall, balancing the
termination
criteria
such as -!::'v/!:J.t or !:J.T/!:J.t,which
are
-7-
batteries. When VCTRL rises above 0.1 V, the buffer sources
VCTRL from 0.0 V. to 1.2 V results in a charge current range
final battery voltage by appropriately selecting the external resis-
:tl % instead of:t2% for the ADP3811.
VCTRL Input and Charge Current Programming Range
The voltage on the VCTRL input determines the charge current
level. This input is buffered by an internal single supply ampli-
fier (labeled BUFFER) to allow easy programmability of VCTRL.
For example, for a fixed charge current, VCTRL can be set by a
resistor divider from the reference output. If a microcontroller
is setting the charge current, a simple RC filter on VCTRL e nables
the voltage to be set by a PWM output from the micro. Of
course, a digital-to-analog converter could also be used, but the
high impedance input makes a PWM output the economical
choice. The bias current of VCTRL is typically 25 nA, which
flows out of the pin.
The guaranteed input voltage range of the buffer is from 0.0 V
to 1.2 V. When VCTRL is in the range of 0.0 V to 0.1 V, the out-
put of the internal amplifier is fixed at 0.1 V. This corresponds
to a charge current of 100 mA for Res
The graph of charge current versus VCTRL in Figure 7 shows this
relationship. Figure I shows a diode in series with the buffer's
output and a 1.5 MQ resistor from VREF to this output. The
diode prevents the amplifier from sinking current, so for small
input voltages the buffer has an open output. The 1.5 MQ
resistor forms a divider with the internal 80 kQ resistor to fix the
output at 0.1 V, i.e., about 10% of the maximum current. This
corresponds to the typical trickle charge current level for NiCad
current and the output follows the input. The total range of
from 100 mA to 1.2 A (for Res
program the VCTRL input to set the charge current. The high
higher frequency compensation (fc
pensation values is given later in this data sheet.
ADP3810 and ADP3811 Differences
The main difference between the ADP381 0 and the ADP3811
is illustrated in Figure I. The resistors RI and R2 are external
for the ADP3811 and internal for the ADP3810. The ADP3810
is specifically designed for Lilon battery charging, and thus, the
internal resistors are precision thin-film resistors laser trimmed
for Lilon cell voltages. Four different final voltage options are
available in the ADP3810: 4.2 V, 8.4 V, 12.6 V, and 16.8 V.
For slightly different voltages to accommodate different LiIon
chemistries, please contact the factory. The ADP3811 does not in-
clude the internal resistors, allowing the designer to choose any
tors. Because the ADP381 0 is specifically for Lilon batteries,
the reference is trimmed to a tighter accuracy specification of
impedance of VCTRL enables the inclusion of an RC filter to in-
tegrate a PWM output into a dc control voltage.
Compensation
The voltage and current loops have significantly different natu-
ral and crossover frequencies in a battery charger application, so
the two loops most likely need different pole/zero feedback com-
pensation. Figure I shows a single RC network from the
CaMP node to ground. This is primarily for low frequency
compensation (fc< 100 Hz) of the voltage loop. Since the
CaMP node is shared by both GM stages, this compensation
also affects the current loop. The internal 200 Q resistor does
change the zero location of the compensation for the current
loop with respect to the voltage loop. To provide a separate
series RC may be needed. A detailed calculation of the com-
ADP3810/ADP3811
=
0.25 Q, R3 = 20 kQ). Larger
-
I kHz-I 0 kHz), a second
=
0.25Q, R3 = 20kQ.