TLE6287GPNT Infineon Technologies, TLE6287GPNT Datasheet
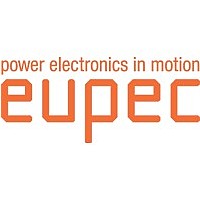
TLE6287GPNT
Specifications of TLE6287GPNT
TLE6287GPNT Summary of contents
Page 1
...
Page 2
Motor Control Development Kit Revision History:2003-06 V 1.0 Previous Version:- Page Subjects (major changes since last revision) 1.0 June 2003: First Release References Infineon C868 User’s Manual http://www.infineon.com/cmc_upload/documents/048/247/ UM_c868_BA_singlepage_v1.0.pdf Infineon TLE6280GP Datasheet http://www.infineon.com/cmc_upload/documents/014/220/TLE6280GP_P6_1.pdf We Listen to Your Comments Any information ...
Page 3
Introduction This user manual describes the MCDK, Motor Control Development Kit reference design board and its functions. The MCDK reference design provides a turnkey solution for driving 3-phase low voltage brushless DC and AC induction motors, which are usually ...
Page 4
... Supports Hall-Effect sensors or sensor-less control • Extension for alternative MCU like XC164 • Small foot print: 5¼” x 3” dimension (133.4mm x 76.2mm) • SW development tools: Keil Compiler + Debugger or Mini Debugger http://www.keil.com + free reference software User’s Manual Motor Control Development Kit ...
Page 5
Assembly Current Sensor Bridge Driver DC Supply Hall Signals RS232 Figure 1 Assembly of the MCDK Board User’s Manual Motor Control Development Kit Power Transistors EEPROM Expansion I/Os for Alternate MCU 5 MCDK Overview Motor Wires Pot for speed ...
Page 6
Hardware Design The hardware is designed with maximum versatility and flexibility to meet fluctuating motor drive needs: • CPU selections between C868 and alternatives like C164, XC164 and TriCore. • Power Transistor Packages compatible in both DPAK and D2PAK ...
Page 7
Period Reg. CT1P Offset Reg. CT1OF Input Compare Timer 16-bit Compare Timer 16-bit F Control CP Compare Co Input F Control CP Timer Period Reg. Period Reg. Figure 3 Block Diagram of the CAPCOM6E PWM Unit (with C868) User’s Manual ...
Page 8
Board Configurations The MCDK board is pre-configured during production. The following table shows the factory setting for circuit breaks and jumpers: – CB1: Close – CB2: Close – CB3: Open – CB4: Open – CB5: Close – CB6: Open ...
Page 9
Jumper Settings Jumper setting is more flexible, users can change “on-the-fly” to meet specific applications. Table 2 Jumper setting for bootstrap mode JP1: Bootstrap Mode Selection Table 3 Jumper setting for logic power ...
Page 10
Get Started 5.1 Run the Demo The EEPROM on the board has been pre-programmed with a BLDC motor control reference demo, the microcontroller C868 will boot from the EEPROM and automatically fetch then execute the code after power-up. The ...
Page 11
Utilize an Alternative Microcontroller The expansion I/O connector, JP9, allows users to apply an alternative microcontroller to drive the motor, for example, the Infineon C166 series microcontrollers with integrated CAPCOM6(E) PWM units such as the XC164. The signals of ...
Page 12
The expansion I/Os provide all the necessary signals for external microcontroller to access the EEPROM, RS232 interface and motor drive circuits. There are two ways to utilize an alternate microcontroller: One is to design a mezzanine board that can plug ...
Page 13
Appendix 1: Layout Figure 4 Assembly Bottom Figure 5 Assembly Top User’s Manual Motor Control Development Kit Appendix 1: Layout 13 V 1.0, 2003-06 ...
Page 14
Figure 6 Bottom Figure 7 Top User’s Manual Motor Control Development Kit Appendix 1: Layout 14 V 1.0, 2003-06 ...
Page 15
Figure 8 Mask bottom Figure 9 Mask top User’s Manual Motor Control Development Kit Appendix 1: Layout 15 V 1.0, 2003-06 ...
Page 16
Figure 10 Silk Bottom Figure 11 Silk Top User’s Manual Motor Control Development Kit Appendix 1: Layout 16 V 1.0, 2003-06 ...
Page 17
Appendix 2: BOM Table 8 Bill of Material for MCDK Reference Design Designator CB1->CB6 C1->C3 C4->C6 C7 C8, C19 C9 C10, C11 C16 C17, C18 C20, C21, C23, C25, C26, C27, C29, C31, C32, C33, C35, C36 C22, C24 ...
Page 18
Table 8 Bill of Material for MCDK Reference Design Designator M1->M6 OZ1 PB1 POT1 POT2 P1 - MALE R1->R6 R13->R18, R27, R33, R34 R19, R31 R20 R21 R22 R24 R25, R26, R32, R36 R28 R29 R30 R35 R37 R38, R39 ...
Page 19
Table 8 Bill of Material for MCDK Reference Design Designator User’s Manual Motor Control Development Kit Quantity Part Type Footprint 1 EEPROM SOIC8 64K 2.7V 1 TLE4274GS P-SOT223-4-1 V33 1 LM6132AIM SOIC8 -ND 1 TLE6280GP ...
Page 20
Appendix 3: Schematics User’s Manual Motor Control Development Kit Appendix 3: Schematics 20 V 1.0, 2003-06 ...
Page 21
Appendix 4: Waveforms Figure 12 Waveforms of PWM and Hall Pattern Signals Driving a 3-phase BLDC motor (Measured with a Mixed Signal Oscilloscope). User’s Manual Motor Control Development Kit Appendix 4: Waveforms Phase A POS0 (H0) POS1 (H1) POS2 ...
Page 22
... Published by Infineon Technologies AG ...