TB6556FG(O,EL,DRY) Toshiba, TB6556FG(O,EL,DRY) Datasheet
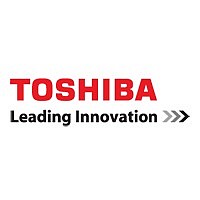
TB6556FG(O,EL,DRY)
Specifications of TB6556FG(O,EL,DRY)
Related parts for TB6556FG(O,EL,DRY)
TB6556FG(O,EL,DRY) Summary of contents
Page 1
... TOSHIBA Bi-CMOS Integrated Circuit Silicon Monolithic 3-Phase Full-Wave Sine-Wave PWM Brushless Motor Controller Features • Sine-wave PWM control • Built-in triangular-wave generator (carrier cycle = f /252 (Hz)) osc • Built-in lead angle control function (0° to 58° steps) External setting/automatic internal setting • ...
Page 2
Block Diagram System clock generator X 15 out HU 21 Position detector Regulator 1 CC GND refout Power-on reset RES ...
Page 3
Pin Description Pin No. Symbol Description 21 HU Positional signal input pin Positional signal input pin Positional signal input pin W Rotation direction signal input 18 CW/CCW pin 11 RES Reset-signal-input pin 2 V ...
Page 4
Input/Output Equivalent Circuits Pin Description Symbol Positional signal input pin U HU Positional signal input pin V HV Positional signal input pin W HW Forward/reverse switching input pin CW/CCW L: Forward (CW) H: Reverse (CCW) Reset input RES L: Stops ...
Page 5
Pin Description Symbol When LA is fixed externally, connect LL to GND and input the setting voltage to the LA pin. Lead angle setting signal Input voltage range 5.0 V input pin (V LA ...
Page 6
Pin Description Symbol Clip upper limit for 5.0 V Upper limit for LA UL When LL > UL fixed at LL value. Setting dead time input pin Digital Td L: 3.8 µs ...
Page 7
Pin Description Symbol Reference voltage signal 5 ± 0.5 V (max 30 mA) V refout output pin Digital Reverse-rotation-detection REV signal output pin Push-pull output: ± (max) Digital FG signal output pin FG Push-pull output: ± ...
Page 8
Absolute Maximum Ratings Characteristics Supply voltage Input voltage Turn-on signal output current Power dissipation Operating temperature Storage temperature Note 1: V pin LA ( out Note 2: V pin: HU, HV, HW, ...
Page 9
... AMP OFS ∆L LA limit setting difference ∆U LA peak hold output PH OUT current T LA (0) Lead angle correction T LA (2. ( monitor V ( Note 5: Toshiba does not implement testing before shipping Test Test Condition ⎯ = open V refout = ⎯ HU, HV, HW CW/CCW, OS, Td, RES in ⎯ HU, HV, HW, CW/CCW, RES, OS, Td, SS Modulation factor maximum ⎯ ...
Page 10
Note 6: T OFF OS = HIGH Turn-on signal ( Turn-on signal ( LOW Turn-on signal ( Turn-on signal ( 0. OFF OFF 0.78 V ...
Page 11
Functional Description 1. Basic operation The motor is driven by the square-wave turn-on signal based on a positional signal. When the positional signal reaches number of rotations higher, the rotor position is estimated according to ...
Page 12
Correcting the lead angle The lead angle can be corrected in the turn-on signal range from 0 to 58° in relation to the induced voltage. Analog input from LA pin ( divided by 32): 0 ...
Page 13
Internal protection • Positional signal abnormality protection Output is turned off when the positional signal is HHH or LLL; otherwise restarted. • Low power supply voltage protection (V For power supply on/off outside the operating voltage range, ...
Page 14
Operation Flow Positional signal Position (Hall IC) detector Voltage instruction System clock Oscillator generator (Note) 92% 100% Phase U Counter Phase V Phase matching Phase Sine-wave pattern W (modulation signal) Triangular wave (carrier frequency) Driven by square wave 2.1 V ...
Page 15
The modulation waveform is generated using Hall signals. The modulation waveform is then compared with the triangular wave and a sine-wave PWM signal is generated. The time (electrical degrees: 60°) from the rising (or falling) edges of the three Hall ...
Page 16
Timing Charts H u Hall signal H v (input signal FG (output Turn-on signal W when driven by square wave X (output Modulation waveform when driven by sine wave (inside of ...
Page 17
Operating Waveform When Driven by Square Wave Hall signal Output waveform stabilize the bootstrap voltage, the lower outputs (X, Y, and Z) are always turned ...
Page 18
Operating Waveform When Driven by Sine-Wave PWM Generation inside of IC Phase U Phase V Phase W Output waveform Inter-line voltage V UV (U- (V- (W-U) When driven by a ...
Page 19
Example of Application Circuit (R2/R1 System clock generator 15 X out 21 HU Position detector Regulator GND 23 V refout Power-on ...
Page 20
Package Dimensions Weight: 0.63 g (typ.) 20 TB6556F/FG 2007-07-17 ...
Page 21
... Application Circuits The application circuits shown in this document are provided for reference purposes only. Thorough evaluation is required, especially at the mass production design stage. Toshiba does not grant any license to any industrial property rights by providing these examples of application circuits. 5. Test Circuits Components in the test circuits are used only to obtain and confirm the device characteristics. These components and circuits are not guaranteed to prevent malfunction or failure from occurring in the application equipment ...
Page 22
... The information contained herein is presented only as a guide for the applications of our products. No responsibility is assumed by TOSHIBA for any infringements of patents or other rights of the third parties which may result from its use. No license is granted by implication or otherwise under any patents or other rights of TOSHIBA or the third parties ...