TB62779FNG Toshiba, TB62779FNG Datasheet - Page 4
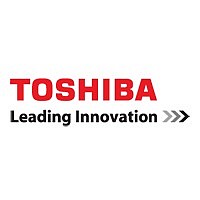
TB62779FNG
Manufacturer Part Number
TB62779FNG
Description
Manufacturer
Toshiba
Datasheet
1.TB62779FNG.pdf
(21 pages)
Specifications of TB62779FNG
Package
VSOP20
# Outputs
9
Vout Max
29V
Io
5.0 to 40mA
Io Accuracy
±6.0%
Features Error Detection
-
Features Gain Control
-
Features Pwm Dimming
7-bit
Other Features & Functions
2-wire interface
Rohs Compatible Product(s) (#)
Available
Available stocks
Company
Part Number
Manufacturer
Quantity
Price
Part Number:
TB62779FNG
Manufacturer:
TOSHIBA/东芝
Quantity:
20 000
Company:
Part Number:
TB62779FNG(O,EL)
Manufacturer:
LINEAR
Quantity:
192
6. Programming the TB62779FNG
Though the specification of these signal lines is similar to that of the I2C bus, these lines are only used to program data to
the TB62779FNG and bi-directional data transfers are not performed. The TB62779FNG should basically be programmed
using one of the following formats: (1) Serial Packet Format in Normal Programming Mode or (2) Serial Packet Format in
Special Mode 1.
1) Serial Packet Format in Normal Programming Mode
【Typical】
a) Data Programming Timing 1
Note: As shown in the above timing diagram, output data changes to 1 when the PWM counter reaches its terminal count
2) Serial Packet Format in Special Mode 1
When the sub-address is specified to 1000XXXX, all the channels are selected in order. Make sure that data for all nine
channels are provided.
(If data for more than nine channels are provided, the 10th and subsequent data are treated as invalid. If data for less than
nine channels are provided, those data are written to the channels in order and the remaining channels retain the previous
data.)
To put the TB62779FNG back into Normal mode, a Start condition should be transmitted first.
In Special Mode 1, the sub address is set with a value of 8 x slave instruction/IC.
S
S
S Slave 1
The TB62779FNG can be programmed by the DATA signal on the SDA pin (pin 2) and CLK signal on the SCK pin (pin 3).
Slave 1(IC1)
Slave 1(IC1)
Slave 2(IC2)
Address
Slave
after the Period condition is shifted in. Therefore, even after the P condition, the next packet should not be shifted in
before the PWM counter reaches its terminal count. Otherwise, the data programmed before the P condition is
overwritten with the next data. After the P condition, an interval of about 3.0 ms (128 PWM cycles) is required before
shifting in the next packet.
address
A
S: Start command; A: Acknowledge command; P: Period command
Slave
8 bits
Sub-address 1
Sub-address 1
A
Sub-address 2
Sub-address 1
Sub-Address(channel select)
IC1 Configuration Period
A
8bits(1000XXXX)
Data 1
A
PWM
PWM
A
IOUT(Data1)
IOUT(Data2)
Sub-address 2 A
(Channel select)
121 122
121 122
Sub-address
A
8 bits
123
123
/OUTR0
Data 2
Data
124
Output data changes to 1 when a logical AND of the
terminal count of the PWM counter(127) and the
Period(P) condition signal becomes 1.
Output data changes to 1 when a logical AND of the
terminal count of the PWM counter(127) and the
Period(P) condition signal becomes 1.
124
A
125 126
125 126
P S
A
/OUTG0
Data
Slave 2
127
127
A
0
0
A
PWM
IC2 Configuration Period
IOUT(Data1)
A
Sub-address 1
/OUTB0
1
1
Data
4
121 122
2
2
A
3
3
configuration)
A
/OUTR1
Data byte
123
Data 1
Data
(PWM
8 bits
Output data changes to 1 when a logical AND of the
terminal count of the PWM counter(127) and the
Period(P) condition signal becomes 1.
124
A P
A
125 126
124
124
/OUTG1
Data
125 126
125 126
127
A
127
127
0
/OUTB1
Data
1
A
2
A
P
Terminal Count of
the PWM Counter
/OUTR2
3
changes to 1.
Output Data
Data
Yes
(Period)
P
A
TB62779FNG
/OUTG2
124
Data
2010-07-21
No
125 126
Previous data
A
/OUTB2
127
Data
A
P