HT46R12A Holtek Semiconductor Inc., HT46R12A Datasheet - Page 11
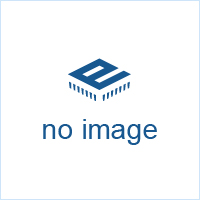
HT46R12A
Manufacturer Part Number
HT46R12A
Description
Ht46r12a -- A/d Type 8-bit Otp Mcu
Manufacturer
Holtek Semiconductor Inc.
Datasheet
1.HT46R12A.pdf
(48 pages)
The A/D converter interrupt is initialised by setting the
A/D converter request flag (ADF; bit 6 of the INTC1),
caused by an end of A/D conversion. When the interrupt
is enabled, the stack is not full and the ADF is set, a sub-
routine call to location 018H will occur. The related inter-
rupt request flag, ADF, will be reset and the EMI bit
cleared to disable further interrupts.
During the execution of an interrupt subroutine, other in-
terrupt acknowledgements are held until the RETI in-
struction is executed or the EMI bit and the related
interrupt control bit are set to 1, if the stack is not full. To
return from the interrupt subroutine, a RET or RETI
instruction may be executed. The RETI instruction will set
the EMI bit to re-enable an interrupt service, but the RET
will not.
Interrupts, occurring in the interval between the rising
edges of two consecutive T2 pulses, will be serviced on
the latter of the two T2 pulses, if the corresponding inter-
rupts are enabled. In the case of simultaneous requests
the following table shows the priority that is applied.
These can be masked by resetting the EMI bit.
The EMI, EC0I, EC1I, EEI, ET0I, ET1I, and EADI bits
are all used to control the enable/disable status of the in-
terrupts. These bits prevent the requested interrupt from
being serviced. Once the interrupt request flags, C0F,
C1F, EIF, T0F, T1F, ADF are set, they remain in the
INTC1 or INTC0 register until the interrupts are serviced
or cleared by a software instruction. It is recommended
that a program does not use the CALL subroutine within
the interrupt subroutine. Interrupts often occur in an un-
predictable manner or need to be serviced immediately in
some applications. If only one stack is left and enabling
the interrupt is not well controlled, the original control se-
quence will be damaged if the CALL operates within the
interrupt subroutine.
Oscillator Configuration
Rev. 1.00
Comparator 0 output interrupt
Comparator 1 output interrupt
External Interrupt - from PC1
Timer/Event Counter 0 overflow
Timer/Event Counter 1 overflow
A/D converter completed overflow
Interrupt Source
System Oscillator
Priority Vector
1
2
3
4
5
6
00CH
004H
008H
010H
014H
018H
11
There are two types of system oscillator circuits within the
microcontroller. These are an RC oscillator and a Crys-
tal oscillator, the choice of which is determined via a
configuration option.
If an RC oscillator is used, an external resistor between
OSC1 and VSS is required and whose resistance
should range from 24k
used to monitor the system frequency at 1/4 the system
frequency or can be used to synchronize external cir-
cuitry. The RC oscillator provides the most cost effec-
tive means of oscillator implementation, however, the
frequency of oscillation may vary with VDD, tempera-
ture and process variations. It is, therefore, not recom-
mended for use in timing sensitive applications where
an accurate oscillator frequency is desired.
If a Crystal oscillator is used, a crystal connected be-
tween OSC1 and OSC2 is required. No other external
components are required. Instead of a crystal, a resona-
tor can also be connected between OSC1 and OSC2 to
obtain a frequency reference, but two external capaci-
tors connected between OSC1, OSC2 and ground are
required, if the oscillating frequency is less than 1MHz.
When the system enters the Power-down mode the sys-
tem oscillator is stopped to conserve power.
The WDT oscillator is a free running on-chip RC oscillator,
and no external components are required. Even if the sys-
tem enters the power down mode where the system clock
is stopped, the WDT oscillator will continue to operate with
a period of approximately 65 s at 5V. The WDT oscillator
can be disabled using a configuration option to conserve
power.
Watchdog Timer - WDT
The WDT clock source is implemented using a dedi-
cated internal RC oscillator (WDT oscillator) or by the in-
struction clock, which is the system clock divided by 4.
The choice of which one is used is determined by a
configuration option. This timer is designed to prevent a
software malfunction or a sequence jumping to an un-
known location with unpredictable results. The
Watchdog Timer can be disabled by a configuration op-
tion. If the Watchdog Timer is disabled, all instructions
relating to the WDT result in no operation.
The WDT clock source will be subsequently divided by
either 2
option, to get the actual WDT time-out period. Using the
internal WDT clock source, the minimum WDT time-out
period is about 600ms. This time-out period may vary
with temperature, VDD and process variations. By se-
lecting appropriate WDT options, longer time-out peri-
ods can be implemented. If the WDT time-out is
selected to be f
about 4.7s can be achieved.
13
, 2
14
, 2
S
/2
15
16
or 2
, then a maximum time-out period of
16
, determined by a configuration
to 1M . Pin OSC2 can be
HT46R12A
August 3, 2007