OPA643 Burr-Brown, OPA643 Datasheet - Page 14
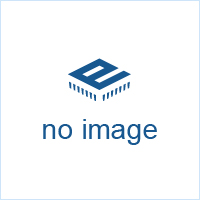
OPA643
Manufacturer Part Number
OPA643
Description
Wideband Low Distortion / High Gain OPERATIONAL AMPLIFIER
Manufacturer
Burr-Brown
Datasheet
1.OPA643.pdf
(17 pages)
Available stocks
Company
Part Number
Manufacturer
Quantity
Price
Company:
Part Number:
OPA643N/250
Manufacturer:
OSRAM
Quantity:
3 463
Part Number:
OPA643P
Manufacturer:
BB
Quantity:
20 000
Part Number:
OPA643U
Manufacturer:
TI/德州仪器
Quantity:
20 000
Part Number:
OPA643UB
Manufacturer:
BB
Quantity:
20 000
The total output noise voltage density can be computed as
the square root of the sum of all squared output noise voltage
contributors. Equation 1 shows the general form for the
output noise voltage using the terms shown in Figure 8.
Dividing this expression by the noise gain (NG = (1+R
R
voltage at the noninverting input as shown in Equation 2.
Evaluating these two equations for the OPA643 component
values shown in Figure 1 will give a total output spot noise
voltage of 13.3nV/ Hz and a total equivalent input spot
noise voltage of 2.7nV/ Hz.
Narrowband communications systems are more commonly
concerned with the Noise Figure (NF) for the amplifier. The
total input referred voltage noise expression (Equation 2
above), may be used to calculate the noise figure. Equation
3 shows the noise figure expression using the E
2 for the non-inverting configuration where the input
termination resistor R
impedance (as shown in Figure 1).
Evaluating Equation 3 for the circuit of Figure 1 gives a
Noise Figure = 15.9dB. Input transformer coupling can be
used to reduce this noise figure. A broadband pulse
transformer can provide both a noiseless voltage gain and a
more optimum source impedance to minimize the noise
figure. Figure 9 shows an example built from the circuit of
Figure 1, in which the transformer turns ratio has been set to
the closest integer for minimum noise figure. This optimum
turns ratio is calculated by:
FIGURE 9. Reduced Noise Figure Circuit.
E
E
G
O
Noise Figure
)) will give the equivalent input referred spot noise
N
R
5.7dB
N
S
= 50
OPT
E
E
NI
NI
2
2
®
Nearest Integer
1:6
I
BN
OPA643
I
BN
NF 10 log 2
R
S
R
T
2
S
has been set to match the 50 source
2
4kTR
1.8k
G = 15V/V [23.5dB]
4kTR
100
S
E
NG
S
N
OPA643
kTRs
E
2
/ I
402
N
Supply Decoupling
2
I
BN
I
BI
NG
Not Shown
BI
R
R
F
F
R
N
2
2
S
of Equation
/ 2
4kTR
50
4kTR
NG
Load
50
Eq. 1
Eq. 2
Eq. 3
Eq. 4
F
NG
F
F
/
14
DC OFFSET CONTROL
The OPA643 provides excellent DC signal accuracy due to
the combination of high open-loop gain, high common-
mode rejection, high power supply rejection, low input
offset voltage and low bias current offset errors. The high
grade (B) version of any package type provides less than
1.5mV input offset voltage. To take full advantage of this
low input offset voltage, careful attention to input bias
current cancellation is also required. The high speed input
stage for the OPA643 has a relatively high input bias current
(19 A typical into each input pin) but with a very close
match between the two input currents—typically 100nA
input offset current. The total output offset voltage may be
considerably reduced by matching the source resistances
which appear at the two inputs. For example, one way to
include bias current cancellation in the circuit of Figure 1
would be to insert a 55
inverting input after the 50 terminating resistor, R
the 50 source resistor is DC coupled, this will increase the
source resistance for the non-inverting input bias current to
80 . Since this is now equal to the resistance appearing at
inverting input (R
the bias currents to the output, leaving only the offset current
times the feedback resistor as a residual DC error term at the
output. Using a 402
will now be less than 3uA • 402
temperature range.
A fine scale output offset null, or DC operating point
adjustment, is often required. Numerous techniques are
available for introducing DC offset control into an op amp
circuit. Most of these techniques eventually reduce to setting
up a DC current through the feedback resistor. In selecting
an offset trim method, one key consideration is the impact
on the desired signal path frequency response. If the signal
path is intended to be non-inverting, the offset control is best
applied as an inverting summing signal to avoid interaction
with the signal source. If the signal path is intended to be
inverting, applying the offset control to the non-inverting
input may be considered—however, the DC offset voltage
on the summing junction will set up a DC current back into
the source which must be considered. Applying an offset
adjustment to the inverting op amp input can change the
noise gain and frequency response flatness. For a DC coupled
inverting amplifier, Figure 10 shows one example of an
offset adjustment technique that has minimal impact on the
signal frequency response. In this case, the DC offsetting
current is brought into the inverting input node through a
resistor which is much larger than the signal path resistors.
This will insure that the adjustment circuit has minimal
effect on the noise gain and hence the frequency response.
THERMAL ANALYSIS
The OPA643 will not require heatsinking under most
operating conditions. Maximum desired junction temperature
will set the maximum allowable internal power dissipation
as described below. In no case should the maximum junction
temperature be allowed to exceed 175 C.
F
|| R
G
), the circuit will cancel the gains for
feedback resistor, this output error
series resistor into the non-
= 1.2mV over the full
T
. When