AD8109-EB Analog Devices, AD8109-EB Datasheet - Page 15
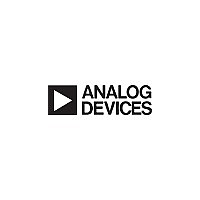
AD8109-EB
Manufacturer Part Number
AD8109-EB
Description
250MHz, 8x8 Buffered Video Crosspoint Switch(Gain=2)
Manufacturer
Analog Devices
Datasheet
1.AD8109-EB.pdf
(28 pages)
THEORY OF OPERATION
The AD8108 (G = +1) and AD8109 (G = +2) share a common
core architecture consisting of an array of 64 transconductance
(gm) input stages organized as eight 8:1 multiplexers with a
common, 8-line analog input bus. Each multiplexer is basically a
folded-cascode high-impedance voltage feedback amplifier with
eight input stages. The input stages are NPN differential pairs
whose differential current outputs are combined at the output
stage, which contains the high impedance node, compensation
and a complementary emitter follower output buffer. In the
AD8108, the output of each multiplexer is fed back directly to the
inverting inputs of its eight gm stages. In the AD8109, the
feedback network is a voltage divider consisting of two equal
resistors.
This switched-gm architecture results in a low power crosspoint
switch that is able to directly drive a back terminated video load
(150 Ω) with low distortion (differential gain and differential
phase errors are better than 0.02% and 0.02°, respectively).
This design also achieves high input resistance and low input
capacitance without the signal degradation and power dissipation
of additional input buffers. However, the small input bias current
at any input will increase almost linearly with the number of
outputs programmed to that input.
The output disable feature of these crosspoints allows larger
switch matrices to be built by simply busing together the outputs
of multiple 8 × 8 ICs. However, while the disabled output imped-
ance of the AD8108 is very high (10 MΩ), that of the AD8109
is limited by the resistive feedback network (which has a nominal
total resistance of 1 kΩ that appears in parallel with the disabled
output. If the outputs of multiple AD8109s are connected through
separate back termination resistors, the loading due to these finite
output impedances will lower the effective back termination
impedance of the overall matrix. This problem is eliminated if the
outputs of multiple AD8109s are connected directly and share a
single back termination resistor for each output of the overall
matrix. This configuration increases the capacitive loading of the
disabled AD8109s on the output of the enabled AD8109.
APPLICATIONS
The AD8108/AD8109 have two options for changing the pro-
gramming of the crosspoint matrix. In the first, a serial word of 32
bits can be provided that will update the entire matrix each time.
The second option allows for changing a single output’s program-
ming via a parallel interface. The serial option requires fewer
signals, but requires more time (clock cycles) for changing the
programming, while the parallel programming technique requires
more signals, but can change a single output at a time and requires
fewer clock cycles to complete programming.
Serial Programming
The serial programming mode uses the device pins CE, CLK,
DATA IN, UPDATE, and SER/PAR. The first step is to assert
a LOW on SER/PAR in order to enable the serial programming
mode. CE for the chip must be LOW to allow data to be clocked
into the device. The CE signal can be used to address an individual
device when devices are connected in parallel.
The UPDATE signal should be HIGH during the time that data
is shifted into the device’s serial port. Although the data will still
shift in when UPDATE is LOW, the transparent, asynchronous
latches will allow the shifting data to reach the matrix. This will
cause the matrix to try to update to every intermediate state as
defined by the shifting data.
The data at DATA IN is clocked in at every down edge of CLK.
A total of 32 data bits must be shifted in to complete the program-
ming. For each of the eight outputs, there are three bits (D0–D2)
that determine the source of its input followed by one bit (D3)
that determines the enabled state of the output. If D3 is LOW
(output disabled), the three associated bits (D0–D2) do not
matter because no input will be switched to that output.
The most significant output address data is shifted in first, then
following in sequence until the least significant output address
data is shifted in. At this point UPDATE can be taken LOW,
which will cause the programming of the device according to the
data that was just shifted in. The UPDATE registers are asyn-
chronous and when UPDATE is LOW, they are transparent.
If more than one AD8108/AD8109 device is to be serially pro-
grammed in a system, the DATA OUT signal from one device
can be connected to the DATA IN of the next device to form a
serial chain. All of the CLK, CE, UPDATE, and SER/PAR pins
should be connected in parallel and operated as described
above. The serial data is input to the DATA IN pin of the first
device of the chain, and it will ripple on through to the last.
Therefore, the data for the last device in the chain should come
at the beginning of the programming sequence. The length of the
programming sequence will be 32 times the number of devices
in the chain.
PARALLEL PROGRAMMING
When using the parallel programming mode, it is not necessary
to reprogram the entire device when making changes to the
matrix. In fact, parallel programming allows the modification of
a single output at a time. Since this takes only one CLK/UPDATE
cycle, significant time savings can be realized by using parallel
programming.
One important consideration in using parallel programming is that
the RESET signal does not reset all registers in the AD8108/AD8109.
When taken low, the RESET signal will only set each output to the
disabled state. This is helpful during power-up to ensure that two
parallel outputs will not be active at the same time.
After initial power-up, the internal registers in the device will
generally have random data, even though the RESET signal was
asserted. If parallel programming is used to program one output,
that output will be properly programmed but the rest of the device
will have a random program state depending on the internal
register content at power-up. Therefore, when using parallel
programming, it is essential that all outputs be programmed to a
desired state after power-up. This will ensure that the programming
matrix is always in a known state. From then on, parallel program-
ming can be used to modify a single, or more, output at a time.
AD8108/AD8109