ltc3612 Linear Technology Corporation, ltc3612 Datasheet - Page 14
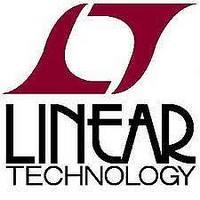
ltc3612
Manufacturer Part Number
ltc3612
Description
3a, 4mhz Monolithic Synchronous Step-down Dc/dc Converter
Manufacturer
Linear Technology Corporation
Datasheet
1.LTC3612.pdf
(28 pages)
Available stocks
Company
Part Number
Manufacturer
Quantity
Price
Company:
Part Number:
ltc3612EFE#TRPBF
Manufacturer:
PANASONIC
Quantity:
45 000
Company:
Part Number:
ltc3612EUDC
Manufacturer:
LT
Quantity:
10 000
Part Number:
ltc3612EUDC
Manufacturer:
LT/凌特
Quantity:
20 000
Part Number:
ltc3612EUDC#PBF
Manufacturer:
LINEAR/凌特
Quantity:
20 000
Company:
Part Number:
ltc3612EUDC#TRPBF
Manufacturer:
TI
Quantity:
1 665
Company:
Part Number:
ltc3612HUDC
Manufacturer:
LT
Quantity:
10 000
Company:
Part Number:
ltc3612HUDC#TRPBF
Manufacturer:
LT
Quantity:
1 042
Part Number:
ltc3612MPUDC
Manufacturer:
LINEAR/凌特
Quantity:
20 000
LTC3612
APPLICATIONS INFORMATION
Frequency Synchronization
The LTC3612’s internal oscillator can be synchronized to
an external frequency by applying a square wave clock
signal to the RT/SYNC pin. During synchronization, the top
switch turn-on is locked to the falling edge of the external
frequency source. The synchronization frequency range
is 300kHz to 4MHz. During synchronization all operation
modes can be selected.
It is recommended that the regulator is powered down
(RUN pin to ground) before removing the clock signal
on the RT/SYNC pin in order to reduce inductor current
ripple.
AC coupling should be used if the external clock genera-
tor cannot provide a continuous clock signal throughout
start-up, operation and shutdown of the LTC3612. The
size of capacitor C
on the RT/SYNC pin and is typically in the range of 10pF
to 22pF
14
Figure 2. Setting the Switching Frequency
C
SYNC
SYNC
T
R
P
T
0.4V
V
V
V
V
IN
IN
IN
IN
R
depends on parasitic capacitance
1.2V
0.3V
T
SV
RT/SYNC
SV
RT/SYNC
SV
RT/SYNC
SV
RT/SYNC
LTC3612
LTC3612
LTC3612
LTC3612
IN
IN
IN
IN
SGND
SGND
SGND
3612 F02
f
2.25MHz
f
f
1/T
f
1/T
OSC
OSC
OSC
OSC
P
P
1/R
T
Inductor Selection
For a given input and output voltage, the inductor value
and operating frequency determine the ripple current. The
ripple current ΔI
with higher inductance:
Having a lower ripple current reduces the core losses
in the inductor, the ESR losses in the output capacitors
and the output voltage ripple. A reasonable starting point
for selecting the ripple current is ΔI
The largest ripple current occurs at the highest V
guarantee that the ripple current stays below a specifi ed
maximum, the inductor value should be chosen according
to the following equation:
The inductor value will also have an effect on Burst Mode
operation. The transition to low current operation begins
when the peak inductor current falls below a level set by the
burst clamp. Lower inductor values result in higher ripple
current which causes this to occur at lower load currents.
This causes a dip in effi ciency in the upper range of low cur-
rent operation. In Burst Mode operation, lower inductance
values will cause the burst frequency to increase.
Inductor Core Selection
Once the value for L is known, the type of inductor must be
selected. Actual core loss is independent of core size for
fi xed inductor value, but it is very dependent on the induc-
tance selected. As the inductance increases, core losses de-
crease. Unfortunately, increased inductance requires more
turns of wire and therefore, copper losses will increase.
Ferrite designs have very low core losses and are preferred
at high switching frequencies, so design goals can con-
centrate on copper loss and preventing saturation. Ferrite
core material saturates “hard,” meaning that inductance
collapses abruptly when the peak design current is ex-
ceeded. This results in an abrupt increase in inductor
L =
ΔI
L
⎛
⎜
⎝
=
f
⎛
⎝ ⎜
SW
f
SW
V
• ΔI
OUT
V
OUT
• L
L
L(MAX)
increases with higher V
⎞
⎠ ⎟
• 1–
⎛
⎝ ⎜
⎞
⎟ • 1–
⎠
V
⎛
⎝ ⎜
V
OUT
IN
V
⎞
⎠ ⎟
V
OUT
IN
⎞
⎠ ⎟
L
= 0.3 • I
IN
and decreases
OUT(MAX)
IN
. To
3612f
.