lm5025-mdc National Semiconductor Corporation, lm5025-mdc Datasheet - Page 12
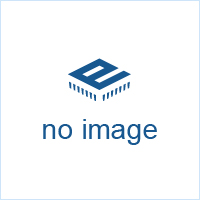
lm5025-mdc
Manufacturer Part Number
lm5025-mdc
Description
Active Clamp Voltage Mode Pwm Controller
Manufacturer
National Semiconductor Corporation
Datasheet
1.LM5025-MDC.pdf
(16 pages)
www.national.com
Current Limit
the PWM comparator will produce the first output pulse at
OUT_A. After the first pulse occurs, the softstart current
source will revert to the normal 20µA level. Fully discharging
and then slowly charging the SS capacitor protects a con-
tinuously over-loaded converter with a low duty cycle hiccup
mode.
These two modes of over-current protection allow the user
great flexibility to configure the system behavior in over-load
conditions. If it is desired for the system to act as a current
source during an over-load, then the CS1 cycle-by-cycle
current limiting should be used. In this case the current
sense signal should be applied to the CS1 input and the CS2
input should be grounded. If during an overload condition it is
desired for the system to briefly shutdown, followed by soft-
start retry, then the CS2 hiccup current limiting mode should
be used. In this case the current sense signal should be
applied to the CS2 input and the CS1 input should be
grounded. This shutdown / soft-start retry will repeat indefi-
nitely while the over-load condition remains. The hiccup
mode will greatly reduce the thermal stresses to the system
during heavy overloads. The cycle-by-cycle mode will have
higher system thermal dissipations during heavy overloads,
but provides the advantage of continuous operation for short
duration overload conditions.
In some systems it is possible utilize both modes concur-
rently, whereby slight overload conditions activate the CS1
cycle-by cycle mode while more severe overloading acti-
vates the CS2 hiccup mode. Operating both modes concur-
rently, requires that the slope of the inductor current be
Oscillator and Sync Capability
The LM5025 oscillator is set by a single external resistor
connected between the RT pin and GND. To set a desired
oscillator frequency (F), the necessary RT resistor can be
calculated from:
where F is in kHz and RT in kΩ.
The RT resistor should be located very close to the device
and connected directly to the pins of the IC (RT and GND).
A unique feature of LM5025 is the ability to synchronize the
oscillator to an external clock with a frequency that is either
higher or lower than the frequency of the internal oscillator.
The lower frequency sync frequency range is 80% of the free
running internal oscillator frequency. There is no constraint
on the maximum SYNC frequency. A minimum pulse width of
100ns is required for the synchronization clock . If the syn-
chronization feature is not required, the SYNC pin should be
connected to GND to prevent any abnormal interference .
The internal oscillator can be completely disabled by con-
necting the RT pin to REF. Once disabled, the sync signal
RT = (5725/F)
(Continued)
1.026
12
sufficient to reach the CS2 threshold before the CS1 function
turns off the main output switch. This requires a high dv/dt at
the current sense pin. The signal must be fast enough to
reach the second level threshold before the first threshold
detector (CS1) turns off the gate driver. Excessive filtering on
the CS pin, an extremely low value current sense resistor or
an inductor that does not saturate with excessive loading
may prevent the second level threshold from ever being
reached.
A small RC filter, located near the controller, is recom-
mended for each of the CS pins. Each CS input has an
internal FET which discharges the current sense filter ca-
pacitor at the conclusion of every cycle, to improve dynamic
performance. This same FET remains on an additional 50ns
at the start of each main switch cycle to attenuate the leading
edge spike in the current sense signal.
The LM5025 CS comparators are very fast and may respond
to short duration noise pulses. Layout considerations are
critical for the current sense filter and sense resistor. The
capacitor associated with the CS filter must be placed very
close to the device and connected directly to the pins of the
IC (CS and GND). If a current sense transformer is used,
both leads of the transformer secondary should be routed to
the filter network , which should be located close to the IC. If
a sense resistor in the source of the main switch MOSFET is
used for current sensing, a low inductance type of resistor is
required. When designing with a current sense resistor, all of
the noise sensitive low power ground connections should be
connected together near the IC GND and a single connec-
tion should be made to the power ground (sense resistor
ground point).
will act directly as the master clock for the controller. Both the
frequency and the maximum duty cycle of the PWM control-
ler can be controlled by the SYNC signal (within the limita-
tions of the Volt x Second Clamp). The maximum duty cycle
(D) will be (1-D) of the SYNC signal.
Feed-Forward Ramp
An external resistor (R
V
The slope of the signal at the RAMP pin will vary in propor-
tion to the input line voltage. This varying slope provides line
feedforward information necessary to improve line transient
response with voltage mode control. The RAMP signal is
compared to the error signal at the COMP pin by the pulse
width modulator comparator to control the duty cycle of the
main switch output. The Volt Second Clamp comparator also
monitors the RAMP pin and if the ramp amplitude exceeds
2.5V the present cycle is terminated. The ramp signal is
reset to GND at the end of each cycle by either the internal
clock or the Volt Second comparator,which ever occurs first.
IN
and GND are required to create the PWM ramp signal.
FF
) and capacitor (C
FF
20086914
) connected to