a8902 Allegro MicroSystems, Inc., a8902 Datasheet - Page 6
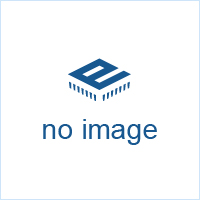
a8902
Manufacturer Part Number
a8902
Description
3-phase Brushless Dc Motor Controller/driver With Back-emf Sensing
Manufacturer
Allegro MicroSystems, Inc.
Datasheet
1.A8902.pdf
(12 pages)
Available stocks
Company
Part Number
Manufacturer
Quantity
Price
Company:
Part Number:
a8902CLB
Manufacturer:
ALLEGRO
Quantity:
1 704
Part Number:
a8902CLB
Manufacturer:
ALLEGRO/雅丽高
Quantity:
20 000
Company:
Part Number:
a8902CLBA
Manufacturer:
ALLE
Quantity:
2 670
Company:
Part Number:
a8902CLBA
Manufacturer:
LT
Quantity:
2 677
Part Number:
a8902CLBA
Manufacturer:
ALLEGRO/雅丽高
Quantity:
20 000
Company:
Part Number:
a8902CLBTR
Manufacturer:
INTEL
Quantity:
6 842
Part Number:
a8902CLBTR
Manufacturer:
ALLEGRO/雅丽高
Quantity:
20 000
the A8902CLBA are n-channel DMOS
transistors with a total source plus sink r
of typically 1 . Internal charge pump boost
circuitry provides voltage above supply for
driving the high-side DMOS gates. Intrinsic
ground clamp and flyback diodes provide
protection when switching inductive loads and
may be used to rectify motor back-EMF in
power-down conditions. An external Schottky
power diode or pass FET is required in series
with the load supply to allow motor back-EMF
rectification in power down conditions.
Running Algorithm. The A8902CLBA
provides a complete self-contained back-EMF
sensing startup and running commutation
scheme. The three half-bridge outputs are
controlled by a state machine. There are six
possible combinations. In each state, one
output is high (sourcing current), one low
(sinking current), and one is OFF (high
impedance or ‘Z’). Motor back EMF is sensed
at the OFF output. The truth table for the
output drivers sequencing is:
of the sequencer states shown. The back
EMF is examined at the OFF output by
comparing the output voltage to the motor
centertap voltage at CENTERTAP. The
motor will then either step forward, step
6
Sequencer
8902–A
3-PHASE BRUSHLESS DC
MOTOR CONTROLLER/DRIVER
State
Power Outputs. The power outputs of
Back-EMF Sensing Motor Startup and
At startup, the outputs are enabled in one
1
2
3
4
5
6
OUT
High
High
Low
Low
Z
Z
A
OUT
High
High
Low
Low
Z
Z
B
OUT
High
High
Low
Low
DS(on)
Z
Z
C
backward, or remain stationary (if in a null-torque position). If the motor
moves, the back-EMF detection circuit waits for the correct polarity
back-EMF zero crossing (output crossing through centertap). True
back-EMF zero crossings are used by the adaptive commutation delay
circuit to advance the state sequencer (commutate) at the proper time
to synchronously run the motor. Back-EMF zero crossings are indi-
cated by FCOM, an internal signal that toggles at every zero crossing.
FCOM is available at the DATA OUT terminal via the programmable
data out multiplexer.
state, then it is in a null-torque position. In this case, the outputs are
commutated automatically by the startup oscillator after a period set by
the external capacitor at C
and the motor will accelerate synchronously. Once normal synchro-
nous back-EMF commutation occurs, the startup oscillator is defeated
by pulses of pulldown current at C
prevents C
cycle and commutating.
115 Northeast Cutoff, Box 15036
Worcester, Massachusetts 01615-0036 (508) 853-5000
V
V
V
OUTA
OUTC
FCOM
OUTB
Startup Oscillator. If the motor does not move at the initial startup
In the next state, the motor will move, back EMF will be detected,
V
CTAP
ST
SOURCE ON
from reaching its upper threshold and thus completing a
t
CST
=
BACK-EMF VOLTAGE
SINK ON
FCOM TOGGLES AT
BACK-EMF ZERO CROSSING
4(V
I
ST
ST(charge)
CSTH
where
- V
ST
+ I
at each commutation, which
CSTL
ST(discharge)
) x C
ST
Dwg. WP-016-1