a8902 Allegro MicroSystems, Inc., a8902 Datasheet - Page 8
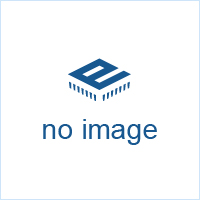
a8902
Manufacturer Part Number
a8902
Description
3-phase Brushless Dc Motor Controller/driver With Back-emf Sensing
Manufacturer
Allegro MicroSystems, Inc.
Datasheet
1.A8902.pdf
(12 pages)
Available stocks
Company
Part Number
Manufacturer
Quantity
Price
Company:
Part Number:
a8902CLB
Manufacturer:
ALLEGRO
Quantity:
1 704
Part Number:
a8902CLB
Manufacturer:
ALLEGRO/雅丽高
Quantity:
20 000
Company:
Part Number:
a8902CLBA
Manufacturer:
ALLE
Quantity:
2 670
Company:
Part Number:
a8902CLBA
Manufacturer:
LT
Quantity:
2 677
Part Number:
a8902CLBA
Manufacturer:
ALLEGRO/雅丽高
Quantity:
20 000
Company:
Part Number:
a8902CLBTR
Manufacturer:
INTEL
Quantity:
6 842
Part Number:
a8902CLBTR
Manufacturer:
ALLEGRO/雅丽高
Quantity:
20 000
via the FILTER terminal, an analog voltage input. Maximum current
limit is also provided, and is controlled in four steps via the serial port.
Output current is sensed via an internal sense resistor (R
voltage across the sense resistor is compared to one-tenth the voltage
at the FILTER terminal less the filter threshold voltage, or to the maxi-
mum current limit reference, whichever is lower. This transcon-
ductance function is I
nominally 0.2
loop speed control system. This system monitors motor speed via
internal or external digital tachometer signals, generates a precision
speed reference, determines the digital speed error, and corrects the
motor current via an internal charge pump and external filtering compo-
nents on the FILTER terminal.
cycles of FCOM (the number of motor poles must be selected via the
serial port). TACH is then a jitter-free signal that toggles once per
motor revolution. The rising edge of TACH triggers REF, a precision
speed reference derived by a programmable counter. The duration of
REF is set by programming the counter to count the desired number of
OSC cycles
8
8902–A
3-PHASE BRUSHLESS DC
MOTOR CONTROLLER/DRIVER
C
R
ERROR SLOW
F1
F1
Current Control. The A8902CLBA provides linear current control
Speed Control. The A8902CLBA includes a frequency-locked
A once per revolution TACH signal can be generated by counting
FROM FLL
FCOM
OSC
FILTER
C
F2
ERROR FAST
POWER UP
(3 x MOTOR POLES)
FROM FLL
CHARGE
PUMP
COUNTER
V
DD
COUNT
FIXED
4-BIT
I c
I d
and V
D20 &
D21
SPEED-CONTROL
SECTOR
INITIALIZATION
S
R
PROGRAMMABLE
ERROR FAST
FROM FLL
SERIAL PORT
OUT
Q
FILTERTH
+
–
REGISTER
COUNTER
x1
ONCE-AROUND
D5–D18
1.85 V
14-BIT
YANK
PULSE
= (V
FILTER
V
is approximately 1.85 V.
DD
D19
MUX
REF
-V
MAX CURRENT LIMIT
–
+
FILTERTH
FROM
SERIAL PORT
REGISTER
D3 AND D4
MUX
C
RES
) / 10R
2
SEQUENTIAL
10
LOGIC
CHARGE
BOOST
PUMP
115 Northeast Cutoff, Box 15036
Worcester, Massachusetts 01615-0036 (508) 853-5000
LINEAR
CURRENT CONTROL
S
+
–
, where R
ERROR
TACH
ERROR
TACH
SLOW
REF
FAST
REF
S
TACH
). The
Dwg. EP-045
S
is
V
R
BB
Dwg. EP-046
S
OUT
where the total count (number of oscillator
cycles) is equal to the sum of the selected
(programmed low) count numbers corre-
sponding to bits D5 through D18.
difference in falling edges of TACH and
REF. The speed error signals control the
error-correcting charge pump on the FILTER
terminal, which drive the external loop com-
pensation components to correct the motor
current.
signal, such as sector or index pulses, may
be used to create the TACH signal, rather
than the internally derived once around. To
use this mode, the signal is input to the
SECTOR terminal, and the sector mode must
be enabled via the serial port. When Switch-
ing from the once-around mode to sector
mode, it is important to monitor the SYNC
signal on DATA OUT, and switch modes only
when SYNC is low. This ensures making the
transition without disturbing the speed control
loop. The speed reference counter should be
reprogrammed at the same time.
improve the acquire time of the speed control
loop, there is an automatic feature controlled
by an internal YANK signal. The motor is
started at the maximized programmed current
by bypassing the FILTER terminal. The
FILTER terminal is clamped to an internal
reference (the filter threshold voltage),
initializing it near the closed loop operating
point. YANK is enabled at startup and stays
high until the desired speed is reached. Once
the first error-fast occurs, indicating the motor
crossed through the desired speed, YANK
goes low. This releases the clamp on the
FILTER terminal and current control is
returned to FILTER. This feature optimizes
speed acquire and minimizes settling. The
Current Control Block Diagram illustrates the
YANK signal and its effects.
total count =
The speed error is detected as the
Sector Mode. An external tachometer
Speed Loop Initialization (YANK). To
desired
desired motor speed (rpm)
60 x f
OSC