l6712a STMicroelectronics, l6712a Datasheet - Page 22
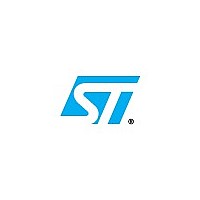
l6712a
Manufacturer Part Number
l6712a
Description
Two-phase Interleaved Dc/dc Controller
Manufacturer
STMicroelectronics
Datasheet
1.L6712A.pdf
(27 pages)
Available stocks
Company
Part Number
Manufacturer
Quantity
Price
Company:
Part Number:
l6712aQTR
Manufacturer:
STMicroelectronics
Quantity:
10 000
Part Number:
l6712aQTR
Manufacturer:
ST
Quantity:
20 000
L6712A L6712
LAYOUT GUIDELINES
Since the device manages control functions and high-current drivers, layout is one of the most important
things to consider when designing such high current applications.
A good layout solution can generate a benefit in lowering power dissipation on the power paths, reducing
radiation and a proper connection between signal and power ground can optimize the performance of the
control loops.
Integrated power drivers reduce components count and interconnections between control functions and
drivers, reducing the board space.
Here below are listed the main points to focus on when starting a new layout and rules are suggested for
a correct implementation.
I
These are the connections where switching and continuous current flows from the input supply towards
the load. The first priority when placing components has to be reserved to this power section, minimizing
the length of each connection as much as possible.
To minimize noise and voltage spikes (EMI and losses) these interconnections must be a part of a power
plane and anyway realized by wide and thick copper traces.
Figure 15. Power connections and related connections layout guidelines (same for both phases).
The critical components, i.e. the power transistors, must be located as close as possible, together and to
the controller. Considering that the "electrical" components reported in figure are composed by more than
one "physical" component, a ground plane or "star" grounding connection is suggested to minimize effects
due to multiple connections.
Fig. 15a shows the details of the power connections involved and the current loops. The input capacitance
(C
order to eliminate the stray inductance generated by the copper traces. Low ESR and ESL capacitors are
required.
I
Fig.15b shows some small signal components placement, and how and where to mix signal and power
ground planes. The distance from drivers and mosfet gates should be reduced as much as possible. Prop-
agation delay times as well as for the voltage spikes generated by the distributed inductance along the
copper traces are so minimized.
In fact, the further the mosfet is from the device, the longer is the interconnecting gate trace and as a con-
sequence, the higher are the voltage spikes corresponding to the gate PWM rising and falling signals.
Even if these spikes are clamped by inherent internal diodes, propagation delays, noise and potential
22/27
Power Connections.
IN
Power Connections Related.
HGATEx
PHASEx
LGATEx
PGNDx
), or at least a portion of the total capacitance needed, has to be placed close to the power section in
a. PCB power and ground planes areas
R
R
gate
gate
HS
LS
D
V
C
IN
IN
L
C
OUT
LOAD
SGND
PHASEx
b. PCB small signal components placement
BOOTx
VCC
C
BOOTx
+V
CC
C
VCC
HS
LS
D
V
C
IN
IN
L
C
OUT
LOAD