SC120 SEMTECH [Semtech Corporation], SC120 Datasheet - Page 15
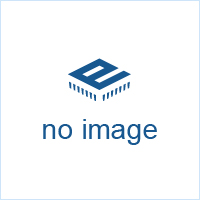
SC120
Manufacturer Part Number
SC120
Description
Low Voltage Synchronous Boost Converter
Manufacturer
SEMTECH [Semtech Corporation]
Datasheet
1.SC120.pdf
(21 pages)
Available stocks
Company
Part Number
Manufacturer
Quantity
Price
Company:
Part Number:
SC12000GH-1
Manufacturer:
AMD
Quantity:
5 510
Company:
Part Number:
SC12001GH-2
Manufacturer:
MOT
Quantity:
67
Company:
Part Number:
SC1200P
Manufacturer:
TDK
Quantity:
6 244
Part Number:
SC1200UFH-266
Manufacturer:
NS/国半
Quantity:
20 000
Part Number:
SC1201UCL-266
Manufacturer:
NS/国半
Quantity:
20 000
Part Number:
SC1201UFH-266
Manufacturer:
NS/国半
Quantity:
20 000
Applications Information (continued)
V
PSAVE exit criterion, illustrated in Figure 3, depends on the
rate of discharge of the output capacitor between PSAVE
bursts. If the time between bursts is less than 5μs, then
PWM operation resumes. The output capacitance value
will aff ect the second criterion, but not the fi rst. Reducing
the output capacitor will reduce the output load at which
PSAVE mode exits to PWM mode.
Within each on/off cycle of a PSAVE burst, the rate of
decrease of the inductor current during the off -state is
proportional to (V
the decrease in current during the off -state may not over-
come the increase in current during the minimum on-time
of the on-state, approximately 100ns. This can result in
the peak inductor current rising above the PSAVE mode
n-channel FET current limit. (Normally, when the
n-channel FET current limit is reached, the on-state ends
immediately and the off -state begins. This sets the duty
cycle on a cycle-by-cycle basis.) This inductor current rise
accumulates with each successive cycle in the burst. The
result is that the output load current that can be sup-
ported in PSAVE under this high V
greater than occurs if the 240mA current limit can be
enforced. Therefore the PSAVE exit load due to the fi rst
exit criterion (Figure 2) can increase significantly. This
OUT
< 0.98 × V
REG
, PWM operation will resume. The second
OUT
− V
Inductor
Current
V
OUT
Figure 3 — PSAVE Operation With Exit to PWM Due To Off -time < 5μs
IN
Voltage
). If V
240mA
+1.8%
+0.8%
Prog’d
-2%
0A
IN
is suffi ciently close to V
BURST
PSAVE Mode at
Moderate Load
IN
(> 5μs)
condition will be
OFF
PRELIMINARY
Higher Load
Applied
OUT
BURST
,
Time
phenomenon is advantageous. Reverting to PWM opera-
tion with high V
to the PWM minimum duty cycle. PSAVE operation avoids
this voltage rise because of its voltage-threshold on/off
control. If the load remains low enough to remain in
PSAVE, V
initally enter PSAVE mode, the initial startup load must be
small enough to cause discontinuous mode PWM opera-
tion. This PSAVE mode startup load upper limit can be
increased if needed by reducing the inductance (refer to
the section Inductor Selection). Suffi ciently large output
capacitance will prevent PSAVE exit due to the second exit
criterion (Figure 3).
PSAVE V
tance on the external FB pin network. If using external
feedback programming, it is prudent to add a small capaci-
tor between OUT and FB to the circuit board layout. When
operating the SC120 in the fi nal confi guration in PSAVE,
observe the amplitude of PSAVE ripple. If the ripple
exceeds 50mV for the expected range of input voltage, a
small-value capacitor should be tried. Capacitance on the
order of a few picofarads is often suffi cient to bring the
ripple amplitude to approximately 50mV.
PSAVE exit due to
off-time reduction
IN
OUT
(< 5μs)
can approach and even slightly exceed V
OFF
ripple may increase due to parasitic capaci-
IN
can result in V
PWM Mode at
High Load
PWM Mode
OUT
rising above V
SC120
REG
OUT
, due
. To
15