ISL78200AVEZ INTERSIL [Intersil Corporation], ISL78200AVEZ Datasheet - Page 17
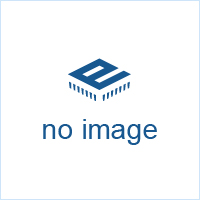
ISL78200AVEZ
Manufacturer Part Number
ISL78200AVEZ
Description
2.5A Regulator with Integrated High-Side MOSFET for Synchronous Buck or Boost Buck Converter
Manufacturer
INTERSIL [Intersil Corporation]
Datasheet
1.ISL78200AVEZ.pdf
(19 pages)
Available stocks
Company
Part Number
Manufacturer
Quantity
Price
Part Number:
ISL78200AVEZ
Manufacturer:
INTERSIL
Quantity:
20 000
Company:
Part Number:
ISL78200AVEZ-T
Manufacturer:
Intersil
Quantity:
1 750
Input Capacitors
Depending upon the system input power rail conditions, the
aluminum electrolytic type capacitor is normally needed to
provide the stable input voltage and restrict the switching
frequency pulse current in small areas over the input traces for
better EMC performance. The input capacitor should be able to
handle the RMS current from the switching power devices.
Ceramic capacitors must be used at the VIN pin of the IC and
multiple capacitors including 1µF and 0.1µF are recommended.
Place these capacitors as closely as possible to the IC.
Output Inductor
Generally the inductor should filter the current ripple to 30~40%
of the regulator’s maximum average output current. The low DCR
inductor should be selected for the highest efficiency. Also, the
inductor saturation current rating should be higher than the
highest transient expected.
Low Side Power MOSFET
In synchronous buck application, a power N MOSFET is needed
as the synchronous low side MOSFET and it must have low
r
(Vgth_min ≥ 1.2V) and Qgd. A good example is BSZ100N06LS3G.
Output Voltage Feedback Resistor Divider
The output voltage can be programmed down to 0.8V by a
resistor divider from V
V
In applications requiring the least input quiescent current, large
resistors should be used for the divider to keep its leakage
current low. 232k is a recommended for the upper resistor.
Compensation Network
With peak current mode control, type II compensation is
normally used for most of applications. However, in applications
seeking to achieve higher bandwidth, type III compensation is
good to use.
Note in applications where the PFM mode is desired, and type III
compensation network is used, the value of the capacitor
between the COMP pin and the FB pin (not the capacitor in series
with the resistor between COMP and FB) should be minimal to
reduce the noise coupling for proper PFM operation. 10pF is
recommended for this capacitor between COMP and FB at PFM
applications. A capacitor (<1nF) at the FB pin to ground also
helps proper PFM mode operation.
Boost Inductor
Besides the need to sustain the current ripple to be within a
certain range (30% to 50%), the boost inductor current at its
soft-start is a more important perspective to be considered in
selection of the boost inductor. Each time the boost starts up,
there is a fixed 500µs soft-start time when the duty cycle
increase linearly from t
start-up, the boost output voltage will jump from V
voltage (V
DS(ON)
OUT
=
, lowest Rg (Rg_typ < 1.5
0.8
IN
⋅
_boost+V
⎛
⎜
⎝
1
+
-------------- -
R
R
LOW
UP
OUT
OUT
⎞
⎟
⎠
MINON
_buck). The design target in boost
to FB according to Equation 11.
17
to ~50%. Before and after boost
Ω
recommended
)
, Vgth
IN
_boost to
(EQ. 11)
ISL78200
soft-start is to ensure the boost input current is sustained to a
minimum but capable of charging the boost output voltage to
have a voltage step equaling to V
block the inductor current increase and not high enough to be
able to charge the output capacitor to the final steady state value
(V
starting point for its selection in design. The boost inductor
current at start-up must be checked by an oscilloscope to ensure
it is under the acceptable range.
Boost Output Capacitor
Based on the same theory in boost start-up described above in
boost inductor selection, a large capacitor at boost output will
cause high inrush current at boost PWM start-up. 22µF is a good
choice for applications with buck output voltage less than 10V.
Also, some minimum amount of capacitance has to be used in
boost output to keep the system stable.
Layout Suggestions
10. Place all the peripheral control components close to the IC.
1. Put the input ceramic capacitors as close to the IC VIN pin and
2. Put the input aluminum capacitors close to IC VIN pin.
3. Keep the phase node copper area small but large enough to
4. Put the output ceramic and aluminum capacitors also close
5. Put vias (≥15) in the bottom pad of the IC. The bottom pad
6. Place the 4.7µF ceramic decoupling capacitor at the VCC pin
7. Keep the bootstrap capacitor close to the IC.
8. Keep the LGATE drive trace as short as possible and try to
9. Place the positive voltage sense trace close to the load for
IN
_boost+V
power ground connecting to the power MOSFET or diode.
Keep this loop (input ceramic capacitor, IC V
MOSFET/diode) as tiny as possible to achieve the least
voltage spikes induced by the trace parasitic inductance.
handle the load current.
to the power stage components.
should be placed in the ground copper plane with an area as
large as possible in multiple layers to effectively reduce the
thermal impedance.
and as close as possible to the IC. Put multiple vias (≥3) close
to the ground pad of this capacitor.
avoid using a via in the LGATE drive path to achieve the lowest
impedance.
tighter regulation.
OUT
_buck) within 500µs. A 6.8µH inductor is a good
FIGURE 31. PCB VIA PATTERN
OUT
_buck. A big inductor will
IN
September 22, 2011
pin and
FN7641.0