MAX8576 MAXIM [Maxim Integrated Products], MAX8576 Datasheet - Page 16
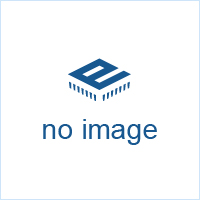
MAX8576
Manufacturer Part Number
MAX8576
Description
3V to 28V Input, Low-Cost, Hysteretic Synchronous Step-Down Controllers
Manufacturer
MAXIM [Maxim Integrated Products]
Datasheet
1.MAX8576.pdf
(18 pages)
Available stocks
Company
Part Number
Manufacturer
Quantity
Price
Company:
Part Number:
MAX8576EUB
Manufacturer:
MAXIM
Quantity:
450
Company:
Part Number:
MAX8576EUB
Manufacturer:
MAXIM
Quantity:
1 179
Part Number:
MAX8576EUB
Manufacturer:
MAXIM/美信
Quantity:
20 000
Company:
Part Number:
MAX8576EUB+
Manufacturer:
MAXIM
Quantity:
340
Company:
Part Number:
MAX8576EUB+T
Manufacturer:
MAXIM
Quantity:
5 870
Part Number:
MAX8576EUB+T
Manufacturer:
MAXIM/美信
Quantity:
20 000
3V to 28V Input, Low-Cost, Hysteretic
Synchronous Step-Down Controllers
chosen based on a prototype or evaluation circuit. As a
general rule, a smaller current ripple results in less out-
put voltage ripple. Since the inductor ripple current is a
factor of the inductor value and input voltage, the output
voltage ripple decreases with larger inductance and
increases with higher input voltages. For reliable and
safe operation, ensure that the capacitor’s voltage and
ripple-current ratings exceed the calculated values.
The response of the MAX8576–MAX8579 to a load
1transient depends on the selected output capacitors.
After a load transient, the output voltage instantly
changes by ESR times
can respond, the output voltage deviates further
depending on the inductor and output capacitor val-
ues. The controller responds immediately as the output
voltage deviates from its regulation limit (see the
Typical Operating Characteristics).
The MAX8576–MAX8579 are compatible with both alu-
minum electrolytic and ceramic output capacitors. Due
to the limited capacitance of a ceramic capacitor, it is
typically used for a higher switching frequency and
lower output current. Aluminum electrolytic is more
applicable to frequencies up to 300KHz and can sup-
port higher output current with its much higher capaci-
tance value.
Due to the much higher ESL and ESR of the aluminum
electrolytic capacitor, an RC filter (R7 and C12 of Figure
2) is required to prevent excessive ESL and ESR ripple
from tripping the feedback threshold prematurely.
Fast-switching transitions cause ringing because of
resonating circuit parasitic inductance and capaci-
tance at the switching nodes. This high-frequency ring-
ing occurs at LX’s rising and falling transitions and can
interfere with circuit performance and generate EMI. To
dampen this ringing, a series RC snubber circuit is
added across each switch. Below is the procedure for
selecting the value of the series RC circuit:
1) Connect a scope probe to measure V
2) Find the capacitor value (connected from LX to
The circuit parasitic (C
the value of the added capacitance above. The circuit
parasitic inductance (L
16
and observe the ringing frequency, f
GND) that reduces the ringing frequency by half.
______________________________________________________________________________________
L
PAR
PAR
PAR
MOSFET Snubber Circuit
(
2
I
) is calculated by:
LOAD
) at LX is then equal to 1/3
f
R
)
2
1
. Before the controller
C
PAR
R
.
LX
to GND,
The resistor for critical dampening (R
2 x f
lor the desired damping and the peak voltage excursion.
The capacitor (C
the value of C
snubber circuit is dissipated in the resistor (P
and can be calculated as:
where V
frequency. Choose an R
the specific application’s derating rule for the power
dissipation calculated.
The feed-forward capacitor, C8 (Figure 2, MAX8576/
MAX8577 with aluminum electrolytic output capacitor),
or C19 (Figure 3, MAX8578/MAX8579 with ceramic out-
put capacitor), dominantly affects the switching fre-
quency. Choose a ceramic X7R capacitor with a value
given by:
or
where F
is the parallel combination of the two feedback divider-
resistors (R1 and R3 of Figure 2, and R9 and R11 of
Figure 3).
Select the closest standard value to C8 and C19 as
possible.
The output inductor and output capacitor also affect the
switching frequency, but to a much lesser extent.
The equations for C8 and C19 above should yield with-
in ±30% of the desired switching frequency for most
applications. The values of C8 and C19 can be
increased to lower the frequency, or decreased to raise
the frequency for better accuracy.
Careful PC board layout is critical to achieve low
switching losses and clean, stable operation. The
switching power stage requires particular attention.
Follow these guidelines for good PC board layout:
C
C
19
8
R
x L
R
R
IN
S
FB
1
FB
1
PAR
is the desired switching frequency, and R
is the input voltage and f
P
RSNUB
. Adjust the resistor value up or down to tai-
PAR
F
F
1
S
1
S
SNUB
Application Information
to be effective. The power loss of the
120
PC Board Layout Guidelines
120
C
) should be at least 2 to 4 times
ns
ns
SNUB
Feed-Forward Capacitor
SNUB
V
V
V
OUT
V
OUT
IN
IN
(
power rating that meets
V
IN
)
2
SW
49 5
39 5
SNUB
.
f
.
SW
is the switching
) is equal to
1
1
V
V
OUT
V
RSNUB
OUT
V
IN
IN
FB
)