ISL65426_07 INTERSIL [Intersil Corporation], ISL65426_07 Datasheet - Page 19
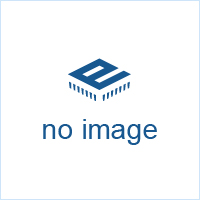
ISL65426_07
Manufacturer Part Number
ISL65426_07
Description
6A Dual Synchronous Buck Regulator with Integrated MOSFETs
Manufacturer
INTERSIL [Intersil Corporation]
Datasheet
1.ISL65426_07.pdf
(22 pages)
The filter capacitor must have sufficiently low ESL and ESR
so that ΔV < ΔV
Most capacitor solutions rely on a mixture of high frequency
capacitors with relatively low capacitance in combination
with bulk capacitors having high capacitance but limited
high-frequency performance. Minimizing the ESL of the
high-frequency capacitors allows them to support the output
voltage as the current increases. Minimizing the ESR of the
bulk capacitors allows them to supply the increased current
with less output voltage deviation.
The ESR of the bulk capacitors also creates the majority of
the output voltage ripple. As the bulk capacitors sink and
source the inductor AC ripple current, a voltage develops
across the bulk capacitor V
The recommended load capacitance recommended is based
on Equation 6.
OUTPUT INDUCTOR SELECTION
Once the output capacitors are selected, the maximum
allowable ripple voltage, V
on the inductance. See Equation 7.
Since the output capacitors are supplying a decreasing
portion of the load current while the regulator recovers from
the transient, the capacitor voltage becomes slightly
depleted. The output inductors must be capable of assuming
the entire load current before the output voltage decreases
more than ΔV
Equation 8 gives the upper limit on output inductance for the
cases when the trailing edge of the current transient causes
the greater output voltage deviation than the leading edge.
Equation 9 addresses the leading edge. Normally, the
trailing edge dictates the inductance selection because duty
cycles are usually less than 50%. Nevertheless, both
inequalities should be evaluated, and inductance should be
governed based on the lower of the two results. In each
equation, L is the output inductance and C is the total output
capacitance.
ΔV
V
L
L
C
PP
OUT
≥
≤
≈
ESR
2 C V
------------------------ - ΔV
MAX
⋅
(
ESL
ΔI
=
⋅
)
×
0.5
2
=
O
×
(
---------------------------------------------------- -
ESR
f
V
s
di
---- -
dt
×
IN
×
MAX
I
OUT
V
+
–
MAX
MAX
IN
×
[
V
ESR
. This places an upper limit on inductance.
MAX
OUT
×
(
---------------------------------------------------- -
V
.
V
–
IN
PP
(
)V
ΔI ESR
×
L
×
–
ΔI
MAX
×
100μF
OUT
V
⋅
f
PPMAX
]
OUT
s
PPMAX
×
19
V
)V
)
IN
OUT
, determines the lower limit
. See Equation 5.
(EQ. 4)
(EQ. 8)
(EQ. 5)
(EQ. 6)
(EQ. 7)
ISL65426
The other concern when selecting an output inductor is the
internally set current mode slope compensation. Designs
should not allow inductor ripple currents below 0.125 times
the maximum output current to prevent regulation issues. A
good rule of thumb for selection of the output inductance
value is 1/3 of the maximum load current for inductor ripple.
L
The rule of thumb value, see Equation 10, with fall between
the minimum inductance value calculated in Equation 7 and
the maximum values determined from Equations 8 and 9.
Input Capacitor Selection
Input capacitors are responsible for sourcing the AC
component of the input current flowing into the switching
power devices. Their RMS current capacity must be
sufficient to handle the AC component of the current drawn
by the switching power devices which is related to duty
cycle. The maximum RMS current required by the regulator
is closely approximated by Equation 11.
The important parameters to consider when selecting an
input capacitor are the voltage rating and the RMS current
rating. For reliable operation, select capacitors with voltage
ratings above the maximum input voltage. Their voltage
rating should be at least 1.25 times greater than the
maximum input voltage, while a voltage rating of 1.5 times is
a conservative guideline. The capacitor RMS current rating
should be higher than the largest RMS current required by
the circuit.
Layout Considerations
Careful printed circuit board (PCB) layout is critical in high-
frequency switching converter design. Current transitions
from one device to another at this frequency induce voltage
spikes across the interconnecting impedances and parasitic
elements. These spikes degrade efficiency, lead to device
overvoltage stress, radiate noise into sensitive nodes, and
increase thermal stress on critical components. Careful
component placement and PCB layout minimizes the
voltage spikes in the converter.
The following multi-layer printed circuitry board layout
strategies minimize the impact of board parasitics on
converter performance and optimize the heat-dissipating
capabilities of the printed circuit board. This section
highlights some important practices which should not be
overlooked during the layout process. Figure 6 provides a
top level view of the critical components, layer utilization,
and signal routing for reference.
L
I
≅
RMS MAX
≤
(
------------------------ - ΔV
(
-------------------------------------------------------------- -
1.25
V
V
(
IN
IN
ΔI
–
×
) C
)
2
V
f
⋅
s
OUT
=
×
I
-----------------------------
OUT MAX
V OUT
-----------------
)
V
×
MAX
IN
3
V
OUT
×
–
⎛
⎜
⎝
(
I
OUT MAX
ΔI ESR
⋅
)
2
+
⎛
⎝
V
----- -
12
1
IN
×
–
⎛
⎜
⎝
V IN V OUT
--------------------------------- -
V
O
L
⎞
⎠
–
×
f
s
February 21, 2007
×
V OUT
-----------------
V
(EQ. 10)
(EQ. 11)
IN
(EQ. 9)
FN6340.2
⎞ 2
⎟
⎠
⎞
⎟
⎠