MAX1965TEEP Maxim Integrated, MAX1965TEEP Datasheet - Page 16
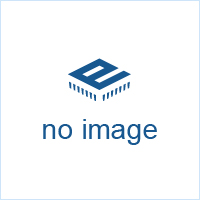
MAX1965TEEP
Manufacturer Part Number
MAX1965TEEP
Description
Current & Power Monitors & Regulators
Manufacturer
Maxim Integrated
Datasheet
1.MAX1965TEEP.pdf
(30 pages)
during startup. The soft-start period is 1024 clock
cycles (1024/f
ramps up the voltage in 64 steps. The output reaches
regulation when soft-start is completed, regardless of
output capacitance and load.
After the reference powers up, the controller begins a
startup sequence. First, the main DC-DC step-down
converter powers up with soft-start enabled. Once the
step-down converter reaches 92% of its nominal value
(V
troller powers up the first positive linear regulator. Once
the first linear regulator reaches 92% of its nominal
value (V
ers up. Once all three output voltages exceed 92% of
their nominal values, the active-high ready signal (POK)
goes high (see Power-Good Output section).
After the reference powers up, the controller simultane-
ously powers up all five output voltages. The main DC-
DC step-down converter powers up with soft-start
enabled while the linear regulators are fully activated.
However, the linear regulators’ inputs are typically con-
nected to or derived from the step-down converter out-
put voltage. Since the linear regulators are fully active,
the pass transistors immediately saturate, allowing
these output voltages to track the step-down convert-
er’s slow rising output voltage (see Typical Operating
Characteristics). Once all five output voltages exceed
92% of their nominal values, the active-high ready sig-
nal (POK) goes high (see Power-Good Output section).
POK is an open-drain output. The MOSFET turns on
and pulls POK low when any output falls below 90% of
its nominal regulation voltage. Once all of the outputs
exceed 92% of their nominal regulation voltages and
soft-start is completed, POK goes high impedance. To
obtain a logic voltage output, connect a pullup resistor
from POK to VL. A 100kΩ resistor works well for most
applications. If unused, leave POK grounded or uncon-
nected.
Thermal overload protection limits total power dissipa-
tion in the MAX1964/MAX1965. When the junction tem-
perature exceeds T
down the device, forcing DL and DH low, allowing the
IC to cool. The thermal sensor turns the part on again
after the junction temperature cools by 15°C, resulting
in a pulsed output during continuous thermal overload
Tracking/Sequencing Triple/Quintuple
Power-Supply Controllers
16
FB
______________________________________________________________________________________
> 1.145V) and soft-start is completed, the con-
FB2
> 1.145V), the second linear regulator pow-
Output Voltage Sequencing (MAX1964)
OSC
Output Voltage Tracking (MAX1965)
Thermal overload Protection
), and the internal soft-start DAC
J
= +160°C, a thermal sensor shuts
Power-Good Output (POK)
conditions. If the VL output is short-circuited, thermal
overload protection is disabled.
During a thermal event, the main step-down converter
and the linear regulators are turned off, POK goes low,
and soft-start is reset.
The step-down controller’s feedback input features dual
mode operation. Connect the output to OUT and con-
nect FB to GND for the preset 3.3V output voltage.
Alternatively, the MAX1964/MAX1965 output voltage
may be adjusted by connecting a voltage-divider from
the output to FB to GND (Figure 4). Select R2 in the
5kΩ to 50kΩ range. Calculate R1 with the following
equation:
where V
to approximately 0.75
connect OUT to GND (MAX1964) or to one of the posi-
tive linear regulators (MAX1965) with an output voltage
between 2V and 5V.
Three key inductor parameters must be specified:
inductance value (L), peak current (I
resistance (R
constant LIR, which is the ratio of inductor peak-to-peak
AC current to DC load current. A higher LIR value
allows smaller inductance, but results in higher losses
and higher output ripple. A good compromise between
size and losses is a 30% ripple-current to load-current
ratio (LIR = 0.3). The switching frequency, input volt-
age, output voltage, selected LIR determine the induc-
tor value as follows:
where f
critical and can be adjusted in order to make trade-offs
among size, cost, and efficiency. Lower inductor values
minimize size and cost, but they also increase the out-
put ripple and reduce the efficiency due to higher peak
currents. On the other hand, higher inductor values
increase efficiency, but at some point resistive losses
due to extra turns of wire will exceed the benefit gained
from lower AC current levels.
SW
SET
is 200kHz. The exact inductor value is not
= 1.236V and V
L
DC
=
). The following equation includes a
R
V
1
IN SW LOAD MAX
DC-DC Step-Down Converter
=
V
ƒ
R
OUT IN
✕
2
V
I
IN
(
V
V
V
Design Procedure
OUT
OUT
SET
(up to 20V). If V
Output Voltage Selection
-
V
(
OUT
may range from 1.236V
-
1
)
LIR
)
PEAK
Inductor Value
OUT
), and DC
> 5.5V,