DS4830EVKIT# Maxim Integrated, DS4830EVKIT# Datasheet - Page 23
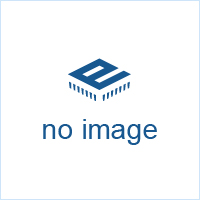
DS4830EVKIT#
Manufacturer Part Number
DS4830EVKIT#
Description
Development Boards & Kits - Other Processors DS4830 Eval Kit
Manufacturer
Maxim Integrated
Datasheet
1.DS4830EVKIT.pdf
(29 pages)
Specifications of DS4830EVKIT#
Rohs
yes
Product
Evaluation Kits
Tool Is For Evaluation Of
DS4830
Interface Type
I2C
Operating Supply Voltage
3 V to 3.6 V
Part # Aliases
90-4830T#EVK
The analog-to-digital converter (ADC) controller is the
digital interface block between the CPU and the ADC. It
provides all the necessary controls to the ADC and the
CPU interface. The ADC uses a set of SFRs for configur-
ing the ADC in desired mode of operation.
The device contains a 13-bit ADC with an input mux
(Figure
ended or eight differential inputs. Additionally, the chan-
nels can be configured to convert internal and external
temperature, V
channels can be programmed to be sample/hold inputs.
The internal channel is used exclusively to measure the
die temperature. The SFR registers control the ADC.
When used in voltage input mode, the voltage applied on
the corresponding channel (differential or single-ended)
is converted to a digital readout. The ADC can be set up
to continuously poll selected input channels (continuous-
sequence mode) or run a short burst of conversions
and enter a shutdown mode to conserve power (single-
sequence mode).
In voltage mode there are four full-scale values that can
be programmed. These values can be trimmed by modi-
fying the associated gain registers (ADCG1, ADCG2,
ADCG4, ADCG8). By default these are set to 1.2V, 0.6V,
2.4V, and 4.8V full scale.
Maxim Integrated
Figure 9. ADC Block Diagram
13-BIT ADC
9). The mux selects the ADC input from 16 single-
ADGAIN
Analog-to-Digital Converter
(START CONVERSATION)
DD
, internal reference, or REFINA/B. Two
ADCCFG
ADCONV
PGA
and Sample/Hold
MUX
ADC-S[15:0]
ADC-D[7:0][P/N]
ADC-SHP[1:0]
ADC-SHN[1:0]
ADC-REFIN[A/B]
ADC-VDD
ADC-VREF_2.5V
ADC-TEXT_A(+/-)
ADC-TEXT_B(+/-)
ADC-TINT
ADC
The ADCCLK is derived from the system clock with divi-
sion ratio defined by the ADC control register. An A/D
conversion takes 15 ADCCLK cycles to complete with
additional four core clocks used for data processing.
Internally every channel is converted twice and the aver-
age of two conversions is written to the data buffer. This
gives each conversion result in (30 x ADC Clock Period
+ 800ns). ADC sampling rate is approximately 40ksps
for the fastest ADC clock (core clock/8). In applications
where extending the acquisition time is desired, the sam-
ple can be acquired over a prolonged period determined
by the ADC control register.
Each ADC channel can have its own configuration,
such as differential mode select, data alignment select,
acquisition extension enable, ADC reference select and
external temperature mode select, etc. The ADC also
has 20 (0 to 19) 16-bit data buffers for conversion result
storage. The ADC data available interrupt flag (ADDAI)
can be configured to trigger an interrupt following a pre-
determined number of samples. Once set, ADDAI can
be cleared by software or at the start of a conversion
process.
Pin combinations A2-A3 and A12-A13 can be used for
sample/hold conversions if enabled in the SHCN register.
These two can be independently enabled or disabled
by writing a 1 or 0 to their corresponding bit locations
in SHCN register. A data buffer location is reserved for
each channel. When a particular channel is enabled,
a sample of the input voltage is taken when a signal is
issued on the SHEN pin, converted and stored in the cor-
responding data buffer.
The two sample/hold channels can sample simultane-
ously on the same SHEN signal or different SHEN signals
depending on the SH_DUAL bit in the SHCN SFR.
The sample/hold data available interrupt flag (SHnDAI)
can be configured to trigger an interrupt following sam-
ple completion. Once set, SHnDAI can be cleared by
software.
Each sample/hold circuit consists of a sampling capaci-
tor, charge injection nulling switches, and a buffer.
Also included is a discharge circuit used to discharge
parasitic capacitance on the input node and the sample
capacitor before sampling begins. The negative input
pins can be used to reduce ground offsets and noise.
Optical Microcontroller
DS4830
Sample/Hold
23