ISL9444EVAL3Z Intersil, ISL9444EVAL3Z Datasheet - Page 3
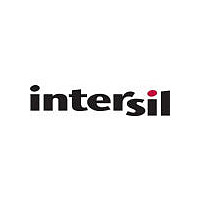
ISL9444EVAL3Z
Manufacturer Part Number
ISL9444EVAL3Z
Description
Power Management IC Development Tools ISL9444 EVALUATION BOARD 3 - 40 Ld QFN - RoHS COMPLIANT
Manufacturer
Intersil
Type
PWM Controllersr
Datasheet
1.ISL9444EVAL3Z.pdf
(16 pages)
Specifications of ISL9444EVAL3Z
Rohs
yes
Product
Evaluation Boards
Tool Is For Evaluation Of
ISL9444
Input Voltage
5.6 V to 16 V
Output Voltage
3.3 V, 5 V
Output Current
25 A
For Use With
ISL9444
Output Setting
The output voltage is set by the feedback resistor divider, R
and R
Where R
from VOx to FBx. Resistor R10, R12 and R13 are resistor jumpers
for loop gain measurement. They are not must-to-have
components. It is recommended to use 50Ω for loop gain
measurement.
Remote Sensing
By sensing the positive rail from load, significant voltage drop
along the PCB trace can be compensated.
For applications with load far from the ISL9444, it is likely that
the remote sensing trace picks up noise from the environment.
To prevent noise being coupled into the feedback loop, it is
recommended to connect the phase boosting capacitors, C
C
For applications that C
C
and C
In case the remote sensing trace become open-circuit, a default
resistor is recommended to connect the resistor R
VOUT.
The ISL9444 does not provide dedicated differential amplifier for
remote sensing.
V
R
ff2
ff
OUT
low
and C
and C
⋅
p
up
=
C
according to Equation 2.
P
.
R
---------------------------- -
low
p
low
=
ff3
is recommended for remote sensing. Please set C
R
R
is the resistor from FBx to GND, R
low
+
up
to the local output capacitors.
R
⋅
up
C
ff
×
0.7V
ffx
is not used for phase boosting, a pair of
3
up
Application Note 1799
is the resistor
up
to the local
low
(EQ. 1)
ff1
(EQ. 2)
ff
,
Transient Load Test
The ISL9444EVAL3Z provides optional load transient test
footprints for high di/dt load transient response tests. Please
refer to Figure 4 for the load transient circuit of PWM1.
1. Select a powerpak or SOIC8 MOSFET with VDSS breakdown
2. Install the load transient circuit as indicated in the
3. Apply pulse square waveform to the gate of the load transient
4. The amplitude of the square waveform set the current step
5. Monitor overshoot and undershoot at the corresponding
greater than VOUT. Select a current sensing resistor. For
accurate current sensing, please use tighter than 5%
tolerance resistors. To alleviate thermal stress, use 0.1Ω or
smaller resistance. For 25A application, a 10mΩ precision
resistor is recommended. Use an oscilloscope to monitor
voltage across R21 and the output voltage.
“Schematic (Optional Circuits and Optional Footprints)” on
page 8. R18, R20 and R22 are 10kΩ resistors for MOSFET
gate discharging.
test MOSFET, Q10. The duty cycle of the pulse waveform
should be small (<5%) to limit thermal stress on current
sensing resistor and the MOSFETs. Set the amplitude of the
square waveform below 0.5V at the beginning.
amplitude. Slowly increase the amplitude of the square
waveform and monitor the current amplitude. Adjust the
square waveform rising and falling time to set the current
step slew rate.
output.
LOAD TRANSIENT CIRCUIT 1
FIGURE 4. LOAD TRANSIENT SET-UP
DNP
R20
DNP,
10k
R21
DNP,
0.01
Q10
J5
ISTEP2
J4
VO1
December 5, 2012
AN1799.0