MCZ33976EGR2 Freescale Semiconductor, MCZ33976EGR2 Datasheet - Page 17
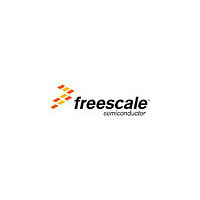
MCZ33976EGR2
Manufacturer Part Number
MCZ33976EGR2
Description
IC DRIVER DUAL GAUGE SPI 24-SOIC
Manufacturer
Freescale Semiconductor
Type
Serial Peripheral Interface (SPI) Dual Step Motor Gauge Driverr
Datasheet
1.MCZ33976EG.pdf
(41 pages)
Specifications of MCZ33976EGR2
Applications
Stepper Motor Driver, 2 Phase
Number Of Outputs
2
Current - Output
100mA
Voltage - Supply
6.5 V ~ 26 V
Operating Temperature
-40°C ~ 125°C
Mounting Type
Surface Mount
Package / Case
24-SOIC (7.5mm Width)
Supply Current
4 mA
Maximum Operating Temperature
+ 125 C
Mounting Style
SMD/SMT
Minimum Operating Temperature
- 40 C
Lead Free Status / RoHS Status
Lead free / RoHS Compliant
Voltage - Load
-
Lead Free Status / Rohs Status
Lead free / RoHS Compliant
Table 11. Return to Zero Register (RTZR)
The register bits in
logic [0] for valid commands.
RTZ event.
valid commands.
properly sequence the integrator, depending upon the
desired zeroing direction.
the selected gauge to return the pointer to zero position.
selects the gauge to be commanded.
Address 101 — Gauge Return to Zero Configuration
Register
used to configure the Return to Zero Event (refer to
page 18). It is written to modify (1) the step time, or rate at
which the pointer moves during an RTZ event, (2) the
integration blanking time, which is the time immediately
following the transition of a coil from a driven state to an open
state in the RTZ mode, and (3) the threshold of the RTZ
integration register.
development to optimize the RTZ for each application.
Selecting an RTZ step rate resulting in consistently
successful zero detections depends on a clear understanding
of the motor characteristics. Specifically, resonant
frequencies exist due to the interaction between the motor
and the pointer. This command allows movement of the RTZ
pointer speed away from these frequencies. Also, some
motors require a significant amount of time for the pointer to
settle to a steady state position when moving from one full
Analog Integrated Circuit Device Data
Freescale Semiconductor
Read
Write
Bits
RZ12:RZ5 (D12:D5) — These bits must be transmitted as
RZ4 (D4) — This bit is used to enable an unconditional
• 0 = Automatic Return to Zero
• 1 = Unconditional Return to Zero
RZ3 (D3) — This bit must be transmitted as logic [0] for
RZ2 (D2) — Return to Zero Direction bit. This bit is used to
• 0 = Return to Zero will occur in the CCW direction
• 1 = Return to Zero will occur in the CW direction
RZ1 (D1) — Return to Zero Direction. This bit commands
• 0 = Return to Zero Disabled
• 1 = Return to Zero Enabled
RZ0 (D0) — Gauge Select: Gauge 0/Gauge 1. This bit
• 0 = Selects Gauge 0
• 1 = Selects Gauge 1
Gauge Return to Zero Configuration Register (RTZCR) is
The values used for this register should be selected during
(PE7 = 0)
(PE7 = 1)
D12
–
0
Table 11
D11
–
0
are write-only.
D10
–
0
D9
–
0
D8
–
0
Table
D7
12,
–
0
Address 100
D6
–
0
step position to the next. Consistent and accurate integration
values require the pointer be stationary at the end of the full
step time.
spent at each full step during an RTZ event. Bits RC3:RC0
are used to select a ∆t ranging from 0 ms (0000) to 61.44 ms
(1111) in increments of 4.096 ms (refer to
page 18). The ∆t is multiplied by the factor M, which is
defined by bits RC12:RC11. The product is then added to the
blanking time, selected using bit RC4, to generate the full
step time. The multiplier selected with RC12:RC11 will be
1 (00), 2 (01), or 4 (10) as illustrated in the equations below.
The multiplier selected with RC12:RC11 will be 1 (00), 2 (01),
or 4 (10) as illustrated in the equations below. Note that the
RC12:RC11 value of 8 (11) is not recommended for use in a
product design application, because of the potential for an
RTZ accumulator internal overflow, due to the long time step.
The blanking time that is selected with bit RC4 determines
the time that is provided immediately following a full step
change, before enabling the integration of the non-driven coil
signal. The blanking time is either 512 µs when RC4 is logic
[0], or 768 µs when it is logic [1].The full step time is
generated using the following equations:
When D3:D0 (RC3:RC0) ≠ 0000
step time when the RC3:RC0 = 0000. The full step time
default value after a logic reset is 12.80 ms
(RC12:RC11 = 00, RC4 = 0, and RC3:RC0 = 0011).
the pointer speed is 1/(FullStep x 2) deg/s.
integrating the EMF present in the non-driven coil during the
RTZ event. The integration circuitry is implemented using a
Sigma-Delta converter resulting in the placement of a value
in the 15-bit RTZ accumulator at the end of each full step. The
value in the RTZ accumulator represents the change in flux
and is compared to a threshold. Values above the threshold
indicate a pointer is moving. Values below the threshold
indicate a stalled pointer, thereby resulting in the cessation of
the RTZ event.
two’s complement. After a full step of integration, a sign bit of
Bits RC3:RC0, RC12:RC11, and RC4 determine the time
Full Step (t) =
When D3:D0 (RC3:RC0) = 0000
Full Step (t) = blanking (t) + 2.048 ms (2)
Note In equation (2), a 2.048 ms offset is added to the full
If there are two full steps per degree of pointer movement,
Detecting pointer movement is accomplished by
The RTZ accumulator bits are signed and represented in
D5
–
0
∆
RZ4
D4
–
t x M + blanking (t)
LOGIC COMMANDS AND REGISTERS
FUNCTIONAL DEVICE OPERATION
D3
–
0
RZ2
D2
–
(1)
Table
RZ1
D1
–
13,
RZ0
D0
–
33976
17