TB6588FG Toshiba, TB6588FG Datasheet - Page 5
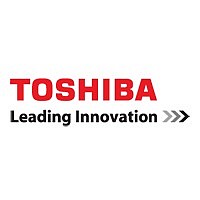
TB6588FG
Manufacturer Part Number
TB6588FG
Description
IC PWM DRVR 3PH DC MOTOR 36HSOP
Manufacturer
Toshiba
Type
3 Phase Full Wave PWM Driver for Sensorless DC Motorsr
Datasheet
1.TB6588FGOELJU.pdf
(20 pages)
Specifications of TB6588FG
Applications
DC Motor Driver, Brushless (BLDC), 3 Phase
Number Of Outputs
1
Current - Output
1.5A
Voltage - Load
7 V ~ 42 V
Voltage - Supply
7 V ~ 42 V
Operating Temperature
-30°C ~ 105°C
Mounting Type
Surface Mount
Package / Case
36-HSOP
Product
Fan / Motor Controllers / Drivers
Operating Supply Voltage
24 V
Supply Current
8 mA
Mounting Style
SMD/SMT
Function
Driver
Vopmax (vm*)
24V (50V)
Io (lpeak)
2.5A
Sinusoidal Current Wave
no
Sensor-less
yes
Speed Feedback Loop
no
Package
HSOP36
Rohs Compatible†
yes
Lead Free Status / RoHS Status
Lead free / RoHS Compliant
Available stocks
Company
Part Number
Manufacturer
Quantity
Price
Part Number:
TB6588FG
Manufacturer:
TOSHIBA/东芝
Quantity:
20 000
Part Number:
TB6588FG(O
Manufacturer:
TOSHIBA/东芝
Quantity:
20 000
Part Number:
TB6588FG(O,8,EL,JU)
Manufacturer:
TOSHIBA/东芝
Quantity:
20 000
Part Number:
TB6588FG(O,EL,JU)
Manufacturer:
TOSHIBA/东芝
Quantity:
20 000
Functional Description
1. Sensorless Drive Mode
2. Startup Operation
START
Based on the analog voltage input for a startup operation, the rotor is aligned to a known position in DC
excitation mode. Then the forced commutation signal is generated to start the motor rotation. As the motor
rotates, the back-EMF occurs in each phase of the coil.
When a signal indicating the polarity of three phase voltage of the motor, including the back-EMF, is
detected at the position signal inputs (WAVEP, WAVEM), the motor driving signal is automatically switched
from the forced commutation PWM signal to the normal commutation PWM signal that is based on the
position signal input (back-EMF). Then, a BLDC motor starts running in sensorless commutation mode.
At startup, no induced voltage is generated due to the stationary motor, and the rotor position cannot be
detected in sensorless mode. Therefore, the TB6588FG rotor is first aligned to a known position in DC
excitation mode for an appropriate period of time, and then the motor is started in forced commutation mode.
The DC excitation and forced commutation times are determined by external capacitors. These time settings
vary depending on the motor type and load, so that they should be adjusted experimentally.
The rotor is aligned to a known position specified in DC excitation mode for the period of (a), during which
the IP pin voltage decreases from V
R
duty cycles for DC excitation and forced commutation modes are determined according to the SC pin voltage.
When the motor rotation frequency exceeds the forced commutation frequency specified by FST1 and FST2,
the operation mode is switched to the sensorless mode. The duty cycle for sensorless mode is determined by
V
VSP
1
SP.
SC
. Then, operation mode is switched to forced commutation mode for the period of (b) as shown above. The
IP
(a): DC excitation time: T
(b): Forced commutation time
T
(a) (b)
FIX
FIX
T
V
UP
AD (L)
(typ.) = 0.69 × C
V
V
REF
REF
/2
REF
to V
T
UP
2
× R
REF
(typ.) = C
1
(s)
/2. The time constant for the period is determined by C
5
1
× V
SP
/4.5 µA (s)
V
V
GND
SP
SP
≥ 1.0 (V)
V
C
SP
1
VSP
SC
C
TB6588FG
2
IP
R
1
START
TB6588FG
2008-4-25
2
and