LM25576MH/NOPB National Semiconductor, LM25576MH/NOPB Datasheet - Page 14
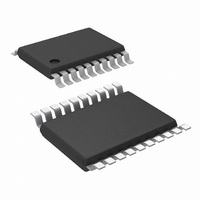
LM25576MH/NOPB
Manufacturer Part Number
LM25576MH/NOPB
Description
IC BUCK SYNC ADJ 3A 20TSSOP
Manufacturer
National Semiconductor
Series
PowerWise®, SIMPLE SWITCHER®r
Type
Step-Down (Buck)r
Specifications of LM25576MH/NOPB
Internal Switch(s)
Yes
Synchronous Rectifier
No
Number Of Outputs
1
Voltage - Output
1.23 ~ 40 V
Current - Output
3A
Frequency - Switching
200kHz, 485kHz
Voltage - Input
6 ~ 42 V
Operating Temperature
-40°C ~ 125°C
Mounting Type
Surface Mount
Package / Case
20-TSSOP Exposed Pad, 20-eTSSOP, 20-HTSSOP
Power - Output
4.2W
Current, Input Bias
3.4 mA
Current, Output
3 A
Frequency, Oscillator
50 kHz to 1 MHz
Package Type
TSSOP-20EP
Power Dissipation
1.9 W
Regulator Type
Buck, Switching
Resistance, Thermal, Junction To Case
6 °C/W
Temperature, Operating, Range
-40 to +125 °C
Voltage, Gain
70 dB
Voltage, Input
6 to 42 V
Voltage, Offset
0.7 V
Voltage, Output
7.15 V
Primary Input Voltage
42V
No. Of Outputs
1
Output Voltage
7.45V
Output Current
3A
No. Of Pins
20
Operating Temperature Range
-40°C To +125°C
Msl
MSL 1 - Unlimited
Filter Terminals
SMD
Rohs Compliant
Yes
For Use With
LM25576BLDT - WEBENCH BUILD IT BOARD LM25576LM25576EVAL - BOARD EVALUATION FOR LM25576
Lead Free Status / RoHS Status
Lead free / RoHS Compliant
Other names
*LM25576MH
*LM25576MH/NOPB
LM25576MH
*LM25576MH/NOPB
LM25576MH
Available stocks
Company
Part Number
Manufacturer
Quantity
Price
Part Number:
LM25576MH/NOPB
Manufacturer:
NS/国半
Quantity:
20 000
www.national.com
Application Information
EXTERNAL COMPONENTS
The procedure for calculating the external components is il-
lustrated with the following design example. The Bill of Mate-
rials for this design is listed in Table 1. The circuit shown in
Figure 1 is configured for the following specifications:
•
•
•
•
•
R3 (R
R
frequency applications are smaller but have higher losses.
Operation at 300kHz was selected for this example as a rea-
sonable compromise for both small size and high efficiency.
The value of R
culated as follows:
The nearest standard value of 21kΩ was chosen for R
L1
The inductor value is determined based on the operating fre-
quency, load current, ripple current, and the minimum and
maximum input voltage (V
To keep the circuit in continuous conduction mode (CCM), the
maximum ripple current I
minimum load current, or 0.5Ap-p. Using this value of ripple
current, the value of inductor (L1) is calculated using the fol-
lowing:
This procedure provides a guide to select the value of L1. The
nearest standard value (33µH) will be used. L1 must be rated
for the peak current (I
loading conditions, the peak current occurs at maximum load
current plus maximum ripple. During an overload condition
the peak current is limited to 4.2A nominal (5.1A maximum).
T
V
V
Fs = 300kHz
Minimum load current (for CCM) = 250mA
Maximum load current = 3A
sets the oscillator switching frequency. Generally, higher
OUT
IN
T
)
= 7V to 42V
= 5V
FIGURE 8. Inductor Current Waveform
T
for 300kHz switching frequency can be cal-
PK+
) to prevent saturation. During normal
RIPPLE
IN(min)
should be less than twice the
, V
IN(max)
).
20208710
T
.
14
The selected inductor (see Table 1) has a conservative 6.2
Amp saturation current rating. For this manufacturer, the sat-
uration rating is defined as the current necessary for the
inductance to reduce by 30%, at 20°C.
C3 (C
With the inductor value selected, the value of C3 (C
necessary for the emulation ramp circuit is:
Where L is in Henrys
With L1 selected for 33µH the recommended value for C3 is
330pF.
C9, C10
The output capacitors, C9 and C10, smooth the inductor rip-
ple current and provide a source of charge for transient load-
ing conditions. For this design a 22µF ceramic capacitor and
a 150µF SP organic capacitor were selected. The ceramic
capacitor provides ultra low ESR to reduce the output ripple
voltage and noise spikes, while the SP capacitor provides a
large bulk capacitance in a small volume for transient loading
conditions. An approximation for the output ripple voltage is:
D1
A Schottky type re-circulating diode is required for all
LM25576 applications. Ultra-fast diodes are not recommend-
ed and may result in damage to the IC due to reverse recovery
current transients. The near ideal reverse recovery charac-
teristics and low forward voltage drop are particularly impor-
tant diode characteristics for high input voltage and low output
voltage applications common to the LM25576. The reverse
recovery characteristic determines how long the current
surge lasts each cycle when the buck switch is turned on. The
reverse recovery characteristics of Schottky diodes minimize
the peak instantaneous power in the buck switch occurring
during turn-on each cycle. The resulting switching losses of
the buck switch are significantly reduced when using a Schot-
tky diode. The reverse breakdown rating should be selected
for the maximum V
The forward voltage drop has a significant impact on the con-
version efficiency, especially for applications with a low output
voltage. “Rated” current for diodes vary widely from various
manufacturers. The worst case is to assume a short circuit
load condition. In this case the diode will carry the output cur-
rent almost continuously. For the LM25576 this current can
be as high as 4.2A. Assuming a worst case 1V drop across
the diode, the maximum diode power dissipation can be as
high as 4.2W. For the reference design a 60V Schottky in a
DPAK package was selected.
C1, C2
The regulator supply voltage has a large source impedance
at the switching frequency. Good quality input capacitors are
necessary to limit the ripple voltage at the VIN pin while sup-
plying most of the switch current during the on-time. When the
buck switch turns on, the current into the VIN pin steps to the
lower peak of the inductor current waveform, ramps up to the
peak value, then drops to zero at turn-off. The average current
into VIN during the on-time is the load current. The input ca-
RAMP
)
IN
, plus some safety margin.
C
RAMP
= L x 10
-5
RAMP
)