AFBR-53D5Z Avago Technologies US Inc., AFBR-53D5Z Datasheet - Page 5
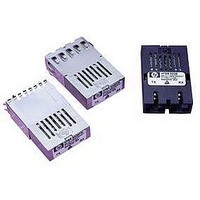
AFBR-53D5Z
Manufacturer Part Number
AFBR-53D5Z
Description
TXRX OPTICAL 5V GBE 1X9
Manufacturer
Avago Technologies US Inc.
Series
-r
Datasheet
1.AFBR-53D5EZ.pdf
(15 pages)
Specifications of AFBR-53D5Z
Applications
Ethernet
Connector Type
SC
Wavelength
850nm
Voltage - Supply
4.75 V ~ 5.25 V
Mounting Type
Through Hole
Supply Voltage
5V
Wavelength Typ
850nm
Leaded Process Compatible
Yes
Data Rate
-
Lead Free Status / RoHS Status
Lead free / RoHS Compliant
Data Rate
-
Lead Free Status / Rohs Status
Lead free / RoHS Compliant
Signal Detect
The Signal Detect circuit provides a deasserted output
signal that implies the link is open or the transmitter
is OFF as defined by the Gigabit Ethernet specification
IEEE 802.3z, Table 38.1. The Signal Detect threshold is
set to transition from a high to low state between the
minimum receiver input optional power and –30 dBm
avg. input optical power indicating a definite opti-
cal fault (e.g. unplugged connector for the receiver or
transmitter, broken fiber, or failed far-end transmitter or
data source). A Signal Detect indicating a working link is
functional when receiving encoded 8B/10B characters.
The Signal Detect does not detect receiver data error or
error-rate. Data errors are determined by Signal process-
ing following the transceiver.
Electromagnetic Interference (EMI)
One of a circuit board designer’s foremost concerns is
the control of electromagnetic emissions from electron-
ic equipment. Success in controlling generated Elec-
tromagnetic Interference (EMI) enables the designer to
pass a governmental agency’s EMI regulatory standard;
and more importantly, it reduces the possibility of inter-
ference to neighboring equipment. There are three op-
tions available for the AFBR-53D5Z with regard to EMI
shielding which provide the designer with a means to
achieve good EMI performance. The EMI performance
of an enclosure using these transceivers is dependent
on the chassis design. Avago Technologies encourages
using standard RF suppression practices and avoiding
poorly EMI-sealed enclosures.
The first configuration is a standard AFBR-53D5Z fiber-
optic transceiver that has no external EMI shield. This
unit is for applications where EMI is either not an issue
for the designer, or the unit resides completely inside
a shielded enclosure, or the module is used in low den-
sity, extremely quiet applications.
The second configuration, option E, is for EMI shielding
applications where the position of the transceiver mod-
ule will extend outside the equipment enclosure. The
external metal shield of the transceiver helps locally to
terminate EM fields to the chassis to prevent their emis-
sions outside the enclosure. This metal shield contacts
the panel or enclosure on the inside of the aperture
on all but the bottom side of the shield and provides
a good RF connection to the panel. This option can ac-
commodate various panel or enclosure thickness, i.e.,
.04 in. min. to 0.10 in. max. The reference plane for this
panel thickness variation is from the front surface of the
panel or enclosure. The recommended length for pro-
truding the AFBR-53D5EZ transceiver beyond the front
surface of the panel or enclosure is 0.25 in. With this op-
tion, there is flexibility of positioning the module to fit
the specific need of the enclosure design. (See Figure 6
for the mechanical drawing dimensions of this shield.)
The third configuration, option F, is for applications that
are designed to have a flush mounting of the module
with respect to the front of the panel or enclosure. The
flush-mount design accommodates a large variety of
panel thickness, i.e., 0.04 in. min. to 0.10 in. max. Note
the reference plane for the flush-mount design is the in-
terior side of the panel or enclosure. The recommended
distance from the centerline of the transceiver front
solder posts to the inside wall of the panel is 0.55 in.
This option contacts the inside panel or enclosure wall
on all four sides of this metal shield. See Figure 8 for the
mechanical drawing dimensions of this shield.
The two designs are comparable in their shielding ef-
fectiveness. Both design options connect only to the
equipment chassis and not to the signal or logic ground
of the circuit board within the equipment closure. The
front panel aperture dimensions are recommended
in Figures 7 and 9. When layout of the printed circuit
board is done to incorporate these metal-shielded
transceivers, keep the area on the printed circuit board
directly under the metal shield free of any components
and circuit board traces. For additional EMI performance
advantage, use duplex SC fiber-optic connectors that
have low metal content inside them. This lowers the
ability of the metal fiber-optic connectors to couple EMI
out through the aperture of the panel or enclosure.