MAX11068EVKIT+ Maxim Integrated Products, MAX11068EVKIT+ Datasheet - Page 75
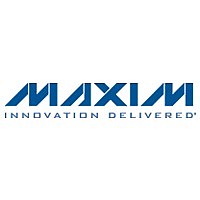
MAX11068EVKIT+
Manufacturer Part Number
MAX11068EVKIT+
Description
KIT SMART BATT MEASUREMENT 12CH
Manufacturer
Maxim Integrated Products
Specifications of MAX11068EVKIT+
Main Purpose
Power Management, Battery Monitor, Car
Utilized Ic / Part
MAX11068
Primary Attributes
Monitors Current, Voltage, Temperature
Secondary Attributes
1 ~ 12 Cell- Li-Ion, 1 ~ 12 Cell- NiMH
Lead Free Status / RoHS Status
Lead free / RoHS Compliant
Embedded
-
After the SMBus ladder modules are configured for com-
munication, they should be configured for operation:
1) Perform a READALL to check device status:
2) Clear the ALRTACK status for the last device using a
3) Clear the RSTSTAT bit on all devices so that future
4) Change configuration registers as necessary with
5) When the device is fully configured, initiate a measure-
WRITEDEVICE or WRITEALL command.
power-cycle events can be detected. This also
allows the last device in the daisy-chain to begin
generating the heartbeat signal.
WRITEALL commands:
ment conversion by setting bit 0 of the SCANCTRL
register (address 0x0D).
a) The RSTSTAT bit should be set in all devices to
b) The last device in the chain shows an ALRTACK
a) Change the broadcast address in register 0x0F if
b) Configure the undervoltage and overvoltage cell
c) Configure the mismatch threshold if required in
d) Configure the undertemperature and overtem-
e) Configure the auxiliary input-acquisition settling
f) Enable the cell input channels that are used for
g) Configure cell-voltage alert enables.
h) Set desired alarm enable flags in the ADCCFG
a different one is required.
thresholds in registers 0x18 to 0x1B.
register 0x1C.
perature thresholds used for thermistor measure-
ments, if required.
time in the ACQCFG register if necessary.
measurement and enable auxiliary channels that
are used.
and FMEA registers.
signify a POR event has occurred.
fault because there is no device above it to
acknowledge its communication.
12-Channel, High-Voltage Sensor, Smart
Data-Acquisition Interface
6) When the first conversion is complete, process the
7) Continue monitoring the system status while initiating
If the default broadcast address must be changed for
an application, the host should manage the process
carefully since the READALL and WRITEALL commands
rely on this address for proper operation. Although
a WRITEALL command can be used to change the
address at any time, it is recommended that a broadcast
address change not be performed until after the SMBus
ladder is fully initialized so that subsequent ROLLCALL
or READALL commands may be used to verify the
address change for all devices.
With the device in a fully initialized state, the new broad-
cast address is written to the BROADCAST ADDRESS
register (address 0x0F) using a WRITEALL command,
although a series of WRITEDEVICE commands may be
used as well. Prior to changing the broadcast address,
the host should save the original address in case it is
needed later in the process. Once the WRITEALL com-
mand is issued, it must be verified. The most straightfor-
ward way of accomplishing this is to issue a ROLLCALL
command and count the number of active devices using
the new address. If the count matches what is expected,
the broadcast address change was successful for all
modules. If the count is incorrect, at least one device
rejected the WRITEALL command and the count signi-
fies which module is not responding to the new address.
A WRITEDEVICE command may be used to rewrite to
individual modules, or another WRITEALL command
may be sent to the old broadcast address. After updating
the missing modules, the ROLLCALL procedure should
again be used to make sure all devices are responding
to the new broadcast address. See Figure 48.
cell and auxiliary input channel data and take any
necessary actions.
new measurements.
Broadcast Address
Changing the
75