HIP6302EVAL1 Intersil, HIP6302EVAL1 Datasheet - Page 3
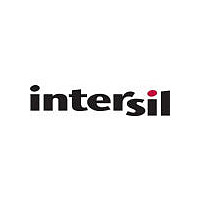
HIP6302EVAL1
Manufacturer Part Number
HIP6302EVAL1
Description
EVALUATION BOARD HIP6302
Manufacturer
Intersil
Specifications of HIP6302EVAL1
Main Purpose
DC/DC, Step Down
Outputs And Type
1, Non-Isolated
Voltage - Output
1.7V
Current - Output
35A
Voltage - Input
5V, 12V
Regulator Topology
Buck
Board Type
Fully Populated
Utilized Ic / Part
HIP6302
Lead Free Status / RoHS Status
Contains lead / RoHS non-compliant
Power - Output
-
Frequency - Switching
-
Figure 4 shows the core voltage, inductor current, and PWM
signals changing in response to the transient load current.
The upper waveform shows the core voltage deviating from
its no-load setting of 1.72V to a minimum of about 1.62V
upon the application of current. The voltage then settles to its
1.67V full-load setting. On load removal, the core voltage
peaks at a level of 1.78V before settling again to its 1.72V
no-load setting. Although the specified operating range
allows deviations as low as 1.60V and as high as 1.85V, a
minimum of 20mV is reserved to allow for the reference
tolerance and the tolerances of other components that
contribute to the overall system accuracy.
Figure 5 is a close-up showing the core-voltage, inductor-
current and PWM signals responding at the leading edge of
the transient load current. The PWM signals increase to their
maximum duty cycle of 75% on the first pulse following the
start of the transient. The inductor currents begin to increase
immediately and are carrying all of the load within 10 µ s. The
very fast transient response is due to the precision 18MHz
error amplifier and optimal compensation of the control loop.
1.7V
1.7V
0A
0A
0V
0V
0V
0V
FIGURE 5. TRANSIENT-RESPONSE LEADING EDGE
FIGURE 4. HIP6302EVAL1 TRANSIENT RESPONSE
CORE VOLTAGE, 50mV/DIV
PWM1, 10V/DIV
INDUCTOR CURRENTS, 10A/DIV
PWM1, 10V/DIV
20µs/DIV
5µs/DIV
3
CORE VOLTAGE, 50mV/DIV
PWM2, 10V/DIV
10A/DIV
INDUCTOR CURRENTS,
PWM2, 10V/DIV
Application Note AN9888
The close up in Figure 6 shows the core-voltage, inductor-
current and PWM signals changing in response to the
trailing edge of the transient load current. Again, the duty
cycles immediately decrease to zero, and the inductors
begin shedding load current at the maximum rate. Note that
the inductor currents briefly go negative as the transient
settles. The capacitors are slightly over charged at the end of
the transient, and the discharge path is in the reverse
direction through the inductors.
Overcurrent Protection
When the current out of either ISEN pin exceeds 82 µA, the
HIP6302 detects an overcurrent condition and responds by
placing the PWM outputs into a high-impedance state. This
signals the HIP6601 to turn off both upper and lower
MOSFETs in order to remedy the overcurrent condition.This
behavior is seen in Figure 7 where PWM1 goes immediately to
2.5VDC when the output current reaches approximately 50A.
The output voltage then quickly falls to zero.
1.7V
0A
0V
0V
0A
0V
0V
FIGURE 6. TRANSIENT-RESPONSE TRAILING EDGE
PWM1, 10V/DIV
FIGURE 7. OVERCURRENT BEHAVIOR
50µs/DIV
5µs/DIV
10A/DIV
INDUCTOR CURRENTS,
PWM1, 5V/DIV
OUTPUT CURRENT,
20A/DIV
PWM2, 10V/DIV
CORE VOLTAGE,
500mV/DIV
CORE VOLTAGE,
50mV/DIV