298D226X0010M2T Vishay, 298D226X0010M2T Datasheet - Page 11
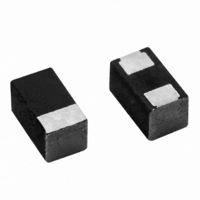
298D226X0010M2T
Manufacturer Part Number
298D226X0010M2T
Description
CAP TANT 22UF 10V 20% SMD
Manufacturer
Vishay
Series
MICROTAN™ 298Dr
Type
Moldedr
Datasheet
1.298D225X0016M2T.pdf
(12 pages)
Specifications of 298D226X0010M2T
Capacitance
22µF
Voltage - Rated
10V
Tolerance
±20%
Esr (equivalent Series Resistance)
10.00 Ohm
Operating Temperature
-55°C ~ 125°C
Mounting Type
Surface Mount
Package / Case
0603 (1608 Metric)
Size / Dimension
0.063" L x 0.033" W (1.60mm x 0.85mm)
Height
0.032" (0.80mm)
Manufacturer Size Code
M
Features
General Purpose
Voltage Rating
10 Volts
Esr
10 Ohms
Operating Temperature Range
- 55 C to + 85 C
Dimensions
0.85 mm W x 1.6 mm L
Mfr Case Code
M Case
Product
Tantalum Solid Standard Grade - Other Various
Dissipation Factor Df
40
Termination Style
SMD/SMT
Lead Free Status / RoHS Status
Lead free / RoHS Compliant
Lead Spacing
-
Lead Free Status / Rohs Status
Details
Other names
718-1718-2
Available stocks
Company
Part Number
Manufacturer
Quantity
Price
Company:
Part Number:
298D226X0010M2T
Manufacturer:
VISHAY
Quantity:
4 288
Part Number:
298D226X0010M2T
Manufacturer:
VISHAY/威世
Quantity:
20 000
298D
Vishay Sprague
GUIDE TO APPLICATION
1.
2.
2.1
2.2
3.
4.
5.
www.vishay.com
48
A-C Ripple Current: The maximum allowable ripple
current shall be determined from the formula:
where,
P =
R
A-C Ripple Voltage: The maximum allowable ripple
voltage shall be determined from the formula:
or, from the formula:
where,
P =
R
Z =
The sum of the peak AC voltage plus the applied DC
voltage shall not exceed the DC voltage rating of the
capacitor.
The sum of the negative peak AC voltage plus the
applied DC voltage shall not allow a voltage reversal
exceeding 10 % of the DC working voltage at + 25 °C.
Reverse Voltage: These capacitors are capable of
withstanding peak voltages in the reverse direction
equal to 10 % of the DC rating at + 25 °C, 5 % of the DC
rating at + 85 °C and 1 % of the DC rating at + 125 °C.
Temperature Derating: If these capacitors are to be
operated at temperatures above + 25 °C, the
permissible rms ripple current or voltage shall be
calculated using the derating factors as shown:
Power Dissipation: Power dissipation will be
affected by the heat sinking capability of the mounting
surface. Non-sinusoidal ripple current may produce
heating effects which differ from those shown. It is
important that the equivalent I
when calculating permissible operating levels. (Power
Dissipation calculated using + 25 C temperature
rise.)
TEMPERATURE
ESR
ESR
+ 125 °C
+ 25 °C
+ 85 °C
=
=
I
V
rms
V
rms
rms
given in the table in paragraph number 5
(power dissipation).
at the specified frequency.
given in the table in paragraph number 5
(power dissipation).
frequency.
Power dissipation in Watts at + 25 °C as
The capacitor equivalent series resistance
Power dissipation in Watts at + 25 °C as
The capacitor equivalent series resistance
at the specified frequency.
The capacitor impedance at the specified
=
=
=
Z
--------------- -
R
I
rms
ESR
P
--------------- -
R
ESR
P
Z
DERATING FACTOR
rms
For technical questions, contact:
M
value be established
ICRO
Solid Tantalum Chip Capacitors
1.0
0.9
0.4
T
AN
TM
Leadframeless Molded
tantalum@vishay.com
6.
7.
7.1
7.2
7.2.1 Backward and Forward Compatibility: Capacitors
8.
8.1
9.
Printed Circuit Board Materials: Molded capacitors
are compatible with commonly used printed circuit
board materials (alumina substrates, FR4, FR5, G10,
PTFE-fluorocarbon and porcelanized steel).
Attachment:
Solder Paste: The recommended thickness of the
solder paste after application is 0.007" ± 0.001"
[0.178 mm ± 0.025 mm]. Care should be exercised in
selecting the solder paste. The metal purity should be
as high as practical. The flux (in the paste) must be
active enough to remove the oxides formed on the
metallization prior to the exposure to soldering heat.
In practice this can be aided by extending the solder
preheat time at temperatures below the liquidous
state of the solder.
Soldering:
conventional soldering techniques; vapor phase,
convection reflow, infrared reflow, wave soldering
and hot plate methods. The Soldering Profile charts
show recommended time/temperature conditions for
soldering.
recommended maximum ramp rate is 2 °C per
second. Attachment with a soldering iron is not
recommended due to the difficulty of controlling
temperature and time at temperature. The soldering
iron must never come in contact with the capacitor.
with SnPb or 100 % tin termination finishes can be
soldered using SnPb or lead (Pb)-free soldering
processes.
Cleaning (Flux Removal) After Soldering: Molded
capacitors are compatible with all commonly used
solvents such as TES, TMS, Prelete, Chlorethane,
Terpene and aqueous cleaning media. However,
CFC/ODS products are not used in the production of
these devices and are not recommended. Solvents
containing methylene chloride or other epoxy
solvents should be avoided since these will attack the
epoxy encapsulation material.
When using ultrasonic cleaning, the board may
resonate if the output power is too high. This vibration
can cause cracking or a decrease in the adherence of
the termination. DO NOT EXCEED 9W/l at 40 kHz for
2 minutes.
Recommended Mounting Pad Geometries: Proper
mounting pad geometries are essential for successful
solder connections. These dimensions are highly
process sensitive and should be designed to
minimize component rework due to unacceptable
solder joints. The dimensional configurations shown
are the recommended pad geometries for both wave
and reflow soldering techniques. These dimensions
are intended to be a starting point for circuit board
designers and may be fine tuned if necessary based
upon the peculiarities of the soldering process and/or
circuit board design.
Preheating
Capacitors
is
can
Document Number: 40065
recommended.
be
Revision: 15-Jan-11
attached
The
by