NCP5030MTTXG ON Semiconductor, NCP5030MTTXG Datasheet - Page 11
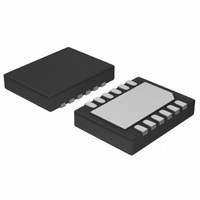
NCP5030MTTXG
Manufacturer Part Number
NCP5030MTTXG
Description
IC LED DRIVR HIGH BRIGHT 12-WDFN
Manufacturer
ON Semiconductor
Type
HBLED Driverr
Datasheet
1.NCP5030MTTXG.pdf
(14 pages)
Specifications of NCP5030MTTXG
Constant Current
Yes
Topology
PWM, Step-Down (Buck), Step-Up (Boost)
Number Of Outputs
1
Internal Driver
Yes
Type - Primary
Flash/Torch
Type - Secondary
White LED
Frequency
600kHz ~ 800kHz
Voltage - Supply
2.7 V ~ 5.5 V
Voltage - Output
2.2 V ~ 5.5 V
Mounting Type
Surface Mount
Package / Case
12-VFDFN Exposed Pad
Operating Temperature
-40°C ~ 85°C
Current - Output / Channel
900mA
Internal Switch(s)
Yes
Efficiency
87%
Operating Supply Voltage (typ)
3.3/5V
Number Of Segments
1
Operating Temperature (min)
-40C
Operating Temperature (max)
85C
Operating Temperature Classification
Industrial
Package Type
WDFN
Pin Count
12
Mounting
Surface Mount
Operating Supply Voltage (min)
2.7V
Operating Supply Voltage (max)
5.5V
Operating Supply Voltage
2.7 V to 5.5 V
Maximum Supply Current
5 mA
Maximum Operating Temperature
+ 85 C
Mounting Style
SMD/SMT
Minimum Operating Temperature
- 40 C
Lead Free Status / RoHS Status
Lead free / RoHS Compliant
Other names
NCP5030MTTXG
NCP5030MTTXGOSTR
NCP5030MTTXGOSTR
Available stocks
Company
Part Number
Manufacturer
Quantity
Price
Company:
Part Number:
NCP5030MTTXG
Manufacturer:
SHARP
Quantity:
1 000
Current Selection
selected currents I
mode, So I
should one need 200 mA for low current mode and 800 mA
for high current mode, R
the following below:
current mode then I
2 and 3, R2 should be selected regarding the following
equation:
to:
PANASONIC ERJ3BQF1R0V (1.0 W 1% 0603)
PANASONIC ERJ3BQFR30V (300 mW 1% 0603)
PANASONIC ERJ3BQJ1R0V (1.0 W 5% 0603)
PANASONIC ERJ3BQJR30V (300 mW 5% 0603)
Analogue Dimming
LEDs at a specific operating current, as the color shift as the
bias current. As a consequence, it is recommended to dim
the LED current by Pulse Width Modulation techniques. A
low frequency PWM signal can be applied to the CTRL
input. LED brightness can be changed by varying the duty
cycle. To avoid any optical flicker the frequency must be
higher than 100 Hz and preferably less than 300 Hz.
Figure 22 shows an application schematic to drive two
An active low logic level of M1 enables the low current
So an active high logic level M1 on gate enables the high
Some recommended resistors include, but are not limited
In white LED applications, it is desirable to operate the
R 2 +
R 2 +
R 2 + 300 mW
FLASH/TORCH
2
Figure 22. Two Current Selections
= 0 and I
200 mV
R 1 +
I FLASH * I 1
800 mA * 200 mA
NTHS5404
F BV
1
200 mV
FLASH
F BV
and I
1
I 1
I LED + I 1 ) I 2
NCP5030
= I
1
+
LED
2
V
= I
.
should be selected according to
OUT
* R DSON_M1
V
200 mV
200 mA
1
S
= 200 mV / R
R2
+ I
I
2
* 33 mW
2
M1
and according Equation
+ 1.0 W
LED
I
R1
1
R
1
SENSE
. For example,
http://onsemi.com
(eq. 2)
(eq. 3)
(eq. 4)
11
Because of the soft−start function set at 1000 ms (nominal),
higher frequency would cause the device to remain active
with lower than expected brightness. Nevertheless, in this
case a dimming control using a filtered PWM signal can be
used. In addition, for DC voltage control the same
technique is suitable and the filter is taken away. Please
refer to “NPC5030 Dimming Control Application Note”.
Inductor Selection
when choosing an inductor: the value of the inductor, the
saturation current and the DCR. Firstly, we need to check
if the inductor is able to handle the peak current without
saturating. Therefore, we have to consider that the
maximum peak inductor current is in Buck−Boost mode
when V
operating V
higher when this device supplies the maximum required
current. In this case, the DC−DC converter is supposed to
operate in Continuous Conduction Mode (CCM) so the
dotted curve in Figure 23 gives the inductor peak current
as a function of load current:
losses in the coil and must be lower than 100 mW to limit
excessive voltage drop. In addition, as DCR is reduced,
overall efficiency will improve. Some recommended
inductors are included but are not limited to:
TDK VLF5014AT−4R71R1
TDK RLF7030T−4R7M3R4
COPPER BUSSMANN FP3−4R7
MURATA LQH43CN4R7M03L
NIC: NIP16W4R7MTRF
Switch Current Limit
current in the inductor according to external R
which is connected between PCA input and the ground.
This allows the user to reduce the peak current being drawn
Three main electrical parameters need to be considered
Finally, an acceptable DCR must be selected regarding
This safety feature is clamping the maximum allowed
2.5
1.5
0.5
Figure 23. Inductor Peak Currents Vs. I
2
1
0
100
OUT
200
IN
is closed T
. Obviously, the peak current inductor is
300
Switch Current Limit
Setup by R
400
BOOST
Operating Inductor Peak Current
I
out
500
PCA
(mA)
threshold for the lower
600
700
OUT
PCA
800
(mA)
resistor,
900