ACPL-P302-000E Avago Technologies US Inc., ACPL-P302-000E Datasheet - Page 12
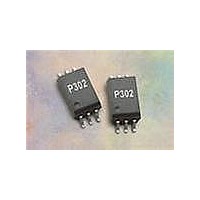
ACPL-P302-000E
Manufacturer Part Number
ACPL-P302-000E
Description
OPTOCOUPLER W/GAASP LED 6-SOIC
Manufacturer
Avago Technologies US Inc.
Datasheet
1.ACPL-P302-500E.pdf
(14 pages)
Specifications of ACPL-P302-000E
Output Type
Push-Pull, Totem-Pole
Package / Case
SO-6
Voltage - Isolation
3750Vrms
Number Of Channels
1, Unidirectional
Current - Output / Channel
400mA
Propagation Delay High - Low @ If
300ns @ 7mA
Current - Dc Forward (if)
12mA
Input Type
DC
Mounting Type
Surface Mount
Fall Time
50 ns
Rise Time
50 ns
Configuration
1 Channel
Isolation Voltage
3750 Vrms
Maximum Forward Diode Voltage
1.8 V
Minimum Forward Diode Voltage
1.2 V
Maximum Reverse Diode Voltage
5 V
Maximum Forward Diode Current
12 mA
Maximum Power Dissipation
250 mW
Maximum Operating Temperature
+ 100 C
Minimum Operating Temperature
- 40 C
Number Of Elements
1
Forward Voltage
1.8V
Forward Current
25mA
Operating Temp Range
-40C to 100C
Power Dissipation
250mW
Propagation Delay Time
700ns
Pin Count
6
Mounting
Surface Mount
Reverse Breakdown Voltage
5V
Operating Temperature Classification
Industrial
Lead Free Status / RoHS Status
Lead free / RoHS Compliant
Lead Free Status / RoHS Status
Lead free / RoHS Compliant, Lead free / RoHS Compliant
LED Drive Circuit Considerations for Ultra High CMR Per-
formance
Without a detector shield, the dominant cause of opto-
coupler CMR failure is capacitive coupling from the input
side of the optocoupler, through the package, to the
detector IC as shown in Figure 19. The ACPL-P302/W302
improves CMR performance by using a detector IC with
an optically transparent Faraday shield, which diverts the
capacitively coupled current away from the sensitive IC
circuitry. However, this shield does not eliminate the ca-
pacitive coupling between the LED and optocoupler pins
5-8 as shown in Figure 20. This capacitive coupling causes
perturbations in the LED current during common mode
transients and becomes the major source of CMR failures
for a shielded optocoupler. The main design objective of
a high CMR LED drive circuit becomes keeping the LED in
the proper state (on or off ) during common mode tran-
sients. For example, the recommended application circuit
(Figure 17), can achieve 10 kV/μs CMR while minimizing
component complexity.
Techniques to keep the LED in the proper state are dis-
cussed in the next two sections.
Figure 19. Optocoupler Input to Output Capacitance Model for Unshielded
Optocouplers.
Figure 20. Optocoupler Input to Output Capacitance Model for Shielded
Optocouplers.
CMR with the LED On (CMR
A high CMR LED drive circuit must keep the LED on during
common mode transients. This is achieved by overdriv-
ing the LED current beyond the input threshold so that
it is not pulled below the threshold during a transient. A
minimum LED current of 7 mA provides adequate margin
over the maximum I
12
1
1
2
2
3
3
1
1
2
2
3
3
C
C
C
C
C
C
C
C
LEDP
LEDP
LEDN
LEDN
LEDP
LEDP
LEDN
LEDN
C
C
LED01
LED01
SHIELD
SHIELD
C
C
LED02
LED02
FLH
of 5 mA to achieve 10 kV/μs CMR.
H
)
6
6
5
5
4
4
6
6
5
5
4
4
CMR with the LED Off (CMR
A high CMR LED drive circuit must keep the LED off (V
d V
during a -dV
flowing through C
V
veloped across the logic gate is less than V
will remain off and no common mode failure will occur.
Figure 21. Equivalent Circuit for Figure 15 During Common Mode Transient.
The open collector drive circuit, shown in Figure 22, can
not keep the LED off during a +dV
all the current flowing through C
by the LED, and it is not recommended for applications
requiring ultra high CMR
drive circuit which like the recommended application
circuit (Figure 17), does achieve ultra high CMR perfor-
mance by shunting the LED in the off state.
Figure 22. Not Recommended Open Collector Drive Circuit.
Figure 23. Recommended LED Drive Circuit for Ultra-High CMR Dead Time
and Propagation Delay Specifications.
+ 5 V
SAT
+5 V
+5 V
+5 V
+5 V
F(OFF)
Q1
Q1
Q1
of the logic gate. As long as the low state voltage de-
) during common mode transients. For example,
1
1
2
2
3
3
+
+
+
-
-
-
V
V
V
SAT
SAT
SAT
1
1
2
2
3
3
C
C
C
C
CM
LEDP
LEDP
LEDN
LEDN
I
I
LEDN
LEDN
C
C
1
2
3
·
LEDP
LEDP
/dt transient in Figure 21, the current
·
THE ARROWS INDICATE THE DIRECTION
C
C
OF CURRENT FLOW DURING - dV
LEDN
LEDN
LEDP
C
C
SHIELD
LEDP
LEDN
I
I
LEDP
SHIELD
SHIELD
also flows through the R
SHIELD
L
L
)
V
performance. The alternative
CM
LEDN
CM
CM
6
6
5
5
4
4
/ dt
/dt transient, since
6
6
5
5
4
4
must be supplied
0.1 mF
6
5
4
F(OFF)
+
+
-
-
V
the LED
SAT
CC
= 18V
R
g
and
F