ADC121S625EVAL/NOPB National Semiconductor, ADC121S625EVAL/NOPB Datasheet - Page 18
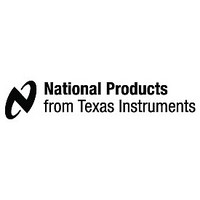
ADC121S625EVAL/NOPB
Manufacturer Part Number
ADC121S625EVAL/NOPB
Description
BOARD EVALUATION FOR ADC121S625
Manufacturer
National Semiconductor
Datasheet
1.ADC121S625CIMMNOPB.pdf
(20 pages)
Specifications of ADC121S625EVAL/NOPB
Number Of Adc's
1
Number Of Bits
12
Sampling Rate (per Second)
200k
Data Interface
Serial
Inputs Per Adc
1 Differential
Input Range
±VREF
Power (typ) @ Conditions
2.25mW @ 200kSPS
Voltage Supply Source
Single Supply
Operating Temperature
-40°C ~ 85°C
Utilized Ic / Part
ADC121S625
Lead Free Status / RoHS Status
Lead free / RoHS Compliant
Other names
ADC121S625EVAL
www.national.com
Applications Information
series resistor can help in this case). Keep in mind that while
the AD121S625 draws very little current from the reference
on average, there are higher instantaneous current spikes at
the reference input that must settle out while SCLK is HIGH.
Because these transient spikes can be almost as high as
20mA, it is important that the reference circuit be capable of
providing this much current and settle out during the mini-
mum 1.5 clock sampling period. Be sure to observe the
minimum SCLK HIGH and LOW times.
The reference input of the ADC121S625, like all A/D convert-
ers, does not reject noise or voltage variations. Keep this in
mind if the reference voltage is derived from the power
supply. Any noise and/or ripple from the supply that is not
rejected by the external reference circuitry will appear in the
digital results. While high frequency noise can be filtered out
as described above, voltage variation due to supply ripple
(50Hz to 120Hz) can be difficult to remove. The use of an
active reference source can ease this problem. The LM4040
and LM4050 shunt reference families and the LM4120,
LM4121 and LM4140 low dropout series reference families
offer a range of choices for a reference source.
The GND pin on the ADC121S625 should be connected to
the ground plane at a quiet point. While there are many
opinions as to the best way to use power and ground planes,
we have looked into this in great detail and have concluded
that all methods can work well up to speeds of about 30MHz
to 40MHz if there is strict adherence to the individual
method. However, many of these methods lead to excessive
EMI/RFI, which is not acceptable from a system standpoint.
Generally, good layout and interconnect techniques can pro-
vide the provide excellent performance required while mini-
mizing EMI/RFI, often without the need for shielding.
We recommend a single ground plane and the use of two or
more power planes. The power planes should all be in the
same board layer and will define, for example, the analog
board area, general digital board area and high power digital
board area. Lines associated with these areas should al-
ways be routed within their respective areas. There are rules
for those cases where a line must cross to another area, but
that is beyond the scope of this document.
Avoid connecting the GND pin too close to the ground point
for a microprocessor, microcontroller, digital signal proces-
sor, or other high power digital device.
7.0 APPLICATION CIRCUITS
The following figures are examples of ADC121S625 typical
application circuits. These circuits are basic ones and will
generally require modification for specific circumstances.
(Continued)
18
7.1 Data Acquisition
Figure 3 shows a basic low cost, low power data acquisition
circuit. Maximum clock rate with a minimum sample rate can
reduce the power consumption further.
7.2 Motor Control
Figure 4 is a motor control application that isolates the digital
outputs of the AD121S625 instead of isolating the analog
signal from the motor. As shown here, the reference voltage
for the AD121S625 is 150mV, and the analog input of the
AD121S625 is connected directly to the current sense resis-
tor. Keeping isolation amplifiers out of the signal path en-
ables a greater system signal-to-noise ratio. However, three
optical isolators are needed to isolate the A/D converters
rather than an isolation amplifier. For three-phase motors,
three of these circuits are needed.
7.3 Strain Gauge Interface
Figure 5 shows an example of interfacing a strain gauge or
load cell to the AD121S625. The same voltage used to bias
the strain gauge is used as a source for the reference
voltage, providing ratiometric operation and making the sys-
tem immune to variations in the source voltage. Of course,
there is no immunity to noise on the reference source or on
the strain gauge source. The value of the divider resistors to
provide the reference voltage for the ADC121S625 may
need to be changed to provide the desired reference voltage
for the specific application.
FIGURE 3. Low cost, low power Data Acquisition
System
20132763