AD7890AN-2 Analog Devices Inc, AD7890AN-2 Datasheet - Page 23
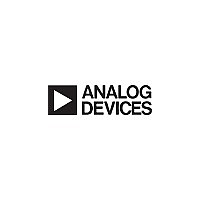
AD7890AN-2
Manufacturer Part Number
AD7890AN-2
Description
IC,Data Acquisition System,8-CHANNEL,12-BIT,DIP,24PIN,PLASTIC
Manufacturer
Analog Devices Inc
Type
Data Acquisition System (DAS)r
Datasheet
1.AD7890ARZ-10.pdf
(28 pages)
Specifications of AD7890AN-2
Rohs Status
RoHS non-compliant
Resolution (bits)
12 b
Sampling Rate (per Second)
117k
Data Interface
Serial
Voltage Supply Source
Single Supply
Voltage - Supply
0 V ~ 2.5 V
Operating Temperature
-40°C ~ 85°C
Mounting Type
Through Hole
Package / Case
24-DIP (0.300", 7.62mm)
Lead Free Status / RoHS Status
PERFORMANCE
LINEARITY
The linearity of the AD7890 is primarily determined by the on-
chip 12-bit D/A converter. This is a segmented DAC that is laser
trimmed for 12-bit integral linearity and differential linearity.
Typical relative numbers for the part are ±1/4 LSB while the
typical DNL errors are ±1/2 LSB.
NOISE
In an ADC, noise exhibits itself as code uncertainty in dc
applications and as the noise floor (in an FFT, for example) in ac
applications. In a sampling ADC like the AD7890, all information
about the analog input appears in the baseband from dc to 1/2 the
sampling frequency. The input bandwidth of the track/hold exceeds
the Nyquist bandwidth and, therefore, an antialiasing filter should
be used to remove unwanted signals above f
in applications where such signals exist.
Figure 19 shows a histogram plot for 8192 conversions of a dc
input using the AD7890. The analog input was set at the center
of a code transition. The timing and control sequence used was
as per Figure 7 where the optimum performance of the ADC is
achieved. The same performance can be achieved in self-
clocking mode where the part transmits its data after
conversion is complete. Almost all of the codes appear in the
one output bin indicating very good noise performance from
the ADC. The rms noise performance for the AD7890-2 for the
plot in Figure 19 was 81 μV. Since the analog input range, and
hence LSB size, on the AD7893-4 is 1.638 times what it is for
the AD7893-2, the same output code distribution results in an
output rms noise of 143 μV for the AD7893-4. For the AD7890-10,
with an LSB size eight times that of the AD7890-2, the code
distribution represents an output rms noise of 648 μV.
In the external clocking mode, it is possible to write data to the
control register or read data from the output register while a
conversion is in progress. The same data is presented in
Figure 20 as in Figure 19, except that in Figure 20, the output
data read for the device occurs during conversion. These results
9000
8000
7000
6000
5000
4000
3000
2000
1000
Figure 19. Histogram of 8192 Conversions of a DC Input
0
(X–4) (X–3) (X–2) (X–1)
SAMPLING FREQUENCY = 102.4kHz
T
A
= 25°C
CODE
X
(X+1) (X+2) (X+3) (X+4)
S
/2 in the input signal
Rev. C | Page 23 of 28
are achieved with a serial clock rate of 2.5 MHz. If a higher
serial clock rate is used, the code transition noise degrades from
that shown in the plot in Figure 20. This has the effect of
injecting noise onto the die while bit decisions are being made,
increasing the noise generated by the AD7890. The histogram
plot for 8192 conversions of the same dc input now shows a
larger spread of codes with the rms noise for the AD7890-2
increasing to 170 μV. This effect varies depending on where the
serial clock edges appear with respect to the bit trials of the
conversion process.
It is possible to achieve the same level of performance when
reading during conversion as when reading after conversion,
depending on the relationship of the serial clock edges to the bit
trial points (for example, the relationship of the serial clock
edges to the CLK IN edges). The bit decision points on the
AD7890 are on the falling edges of the master clock (CLK IN)
during the conversion process. Clocking out new data bits at
these points (for example, the rising edge of SCLK) is the most
critical from a noise standpoint. The most critical bit decisions
are the MSBs, so to achieve the level of performance outlined in
Figure 20, reading within 1 μs after the rising edge of CONVST
should be avoided.
Writing data to the control register also has the effect of
introducing digital activity onto the part while conversion is in
progress. However, since there are no output drivers active
during a write operation, the amount of current flowing on the
die is less than for a read operation. Therefore, the amount of
noise injected into the die is less than for a read operation.
Figure 21 shows the effect of a write operation during
conversion. The histogram plot for 8192 conversions of the
same dc input now shows a larger spread of codes than for ideal
conditions but smaller than for a read operation. The resulting
rms noise for the AD7890-2 is 110 μV. In this case, the serial
clock frequency is 10 MHz.
Figure 20. Histogram of 8192 Conversions with Read During Conversion
8000
7000
6000
5000
4000
3000
2000
1000
0
(X–4) (X–3) (X–2) (X–1)
SAMPLING
FREQUENCY = 102.4kHz
T
A
= 25°C
CODE
X
(X+1) (X+2) (X+3) (X+4)
AD7890