XC5202-6PQ100C Xilinx Inc, XC5202-6PQ100C Datasheet - Page 18
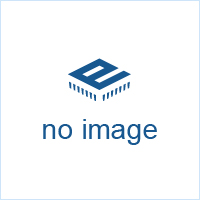
XC5202-6PQ100C
Manufacturer Part Number
XC5202-6PQ100C
Description
IC FPGA 64 CLB'S 100-PQFP
Manufacturer
Xilinx Inc
Series
XC5200r
Datasheet
1.XC5206-5PQ208C.pdf
(73 pages)
Specifications of XC5202-6PQ100C
Number Of Logic Elements/cells
256
Number Of Labs/clbs
64
Number Of I /o
81
Number Of Gates
3000
Voltage - Supply
4.75 V ~ 5.25 V
Mounting Type
Surface Mount
Operating Temperature
0°C ~ 85°C
Package / Case
100-BQFP
Case
QFP100
Dc
99+
Lead Free Status / RoHS Status
Contains lead / RoHS non-compliant
Total Ram Bits
-
Other names
122-1132
Available stocks
Company
Part Number
Manufacturer
Quantity
Price
Company:
Part Number:
XC5202-6PQ100C
Manufacturer:
XILINX
Quantity:
182
Company:
Part Number:
XC5202-6PQ100C
Manufacturer:
XILINX
Quantity:
5 530
Company:
Part Number:
XC5202-6PQ100C
Manufacturer:
XILINX
Quantity:
5 510
Company:
Part Number:
XC5202-6PQ100C
Manufacturer:
XILINX
Quantity:
875
Part Number:
XC5202-6PQ100C
Manufacturer:
XILINX/赛灵思
Quantity:
20 000
XC5200 Series Field Programmable Gate Arrays
XC5200-Series devices can also be configured through the
boundary scan logic. See XAPP 017 for more information.
Data Registers
The primary data register is the boundary scan register.
For each IOB pin in the FPGA, bonded or not, it includes
three bits for In, Out and 3-State Control. Non-IOB pins
have appropriate partial bit population for In or Out only.
PROGRAM, CCLK and DONE are not included in the
boundary scan register.
state captures all In, Out, and 3-State pins.
The data register also includes the following non-pin bits:
TDO.T, and TDO.O, which are always bits 0 and 1 of the
data register, respectively, and BSCANT.UPD, which is
always the last bit of the data register. These three bound-
ary scan bits are special-purpose Xilinx test signals.
The other standard data register is the single flip-flop
BYPASS register. It synchronizes data being passed
through the FPGA to the next downstream boundary scan
device.
The FPGA provides two additional data registers that can
be specified using the BSCAN macro. The FPGA provides
two user pins (BSCAN.SEL1 and BSCAN.SEL2) which are
the decodes of two user instructions, USER1 and USER2.
For
(BSCAN.TDO1 and BSCAN.TDO2) allow user scan data to
be shifted out on TDO.
(BSCAN.DRCK) is available for control of test logic which
the user may wish to implement with CLBs. The NAND of
TCK and RUN-TEST-IDLE is also provided (BSCAN.IDLE).
Instruction Set
The XC5200-Series boundary scan instruction set also
includes instructions to configure the device and read back
the configuration data. The instruction set is coded as
shown in
Table 7: Boundary Scan Instructions
7-100
Instruction I2
0
0
0
0
1
1
1
1
I1
these
0
0
1
1
0
0
1
1
Table
I0
0
1
0
1
0
1
0
1
instructions,
7.
CONFIGURE
SAMPLE/PR
READBACK
Reserved
Selected
BYPASS
EXTEST
USER 1
USER 2
ELOAD
Test
Product Obsolete or Under Obsolescence
Each EXTEST CAPTURE-DR
two
The data register clock
TDO Source
Readback
BSCAN.
BSCAN.
Register
Bypass
DOUT
TDO1
TDO2
Data
corresponding
DR
DR
—
User Logic
User Logic
Pin/Logic
Pin/Logic
Disabled
I/O Data
Source
DR
—
—
pins
Bit Sequence
The bit sequence within each IOB is: 3-State, Out, In. The
data-register cells for the TAP pins TMS, TCK, and TDI
have an OR-gate that permanently disables the output
buffer if boundary-scan operation is selected. Conse-
quently, it is impossible for the outputs in IOBs used by TAP
inputs to conflict with TAP operation. TAP data is taken
directly from the pin, and cannot be overwritten by injected
boundary-scan data.
The primary global clock inputs (PGCK1-PGCK4) are
taken directly from the pins, and cannot be overwritten with
boundary-scan data. However, if necessary, it is possible to
drive the clock input from boundary scan. The external
clock source is 3-stated, and the clock net is driven with
boundary scan data through the output driver in the
clock-pad IOB. If the clock-pad IOBs are used for non-clock
signals, the data may be overwritten normally.
Pull-up and pull-down resistors remain active during
boundary scan. Before and during configuration, all pins
are pulled up. After configuration, the choice of internal
pull-up or pull-down resistor must be taken into account
when designing test vectors to detect open-circuit PC
traces.
From a cavity-up view of the chip (as shown in XDE or
Epic), starting in the upper right chip corner, the boundary
scan data-register bits are ordered as shown in
The device-specific pinout tables for the XC5200 Series
include the boundary scan locations for each IOB pin.
Table 8: Boundary Scan Bit Sequence
BSDL (Boundary Scan Description Language) files for
XC5200-Series devices are available on the Xilinx web site
in the File Download area.
Including Boundary Scan
If boundary scan is only to be used during configuration, no
special elements need be included in the schematic or HDL
code. In this case, the special boundary scan pins TDI,
TMS, TCK and TDO can be used for user functions after
configuration.
To indicate that boundary scan remain enabled after config-
uration, include the BSCAN library symbol and connect pad
symbols to the TDI, TMS, TCK and TDO pins, as shown in
Figure
Bit Position
Bit 0 (TDO)
Bit N (TDI)
Bit 1
20.
...
...
...
Right-edge I/O pads (bottom to top)
Bottom-edge I/O pads (left to right)
Left-edge I/O pads (top to bottom)
Top-edge I/O pads (right to left)
November 5, 1998 (Version 5.2)
I/O Pad Location
BSCANT.UPD
...
Table
8.
R